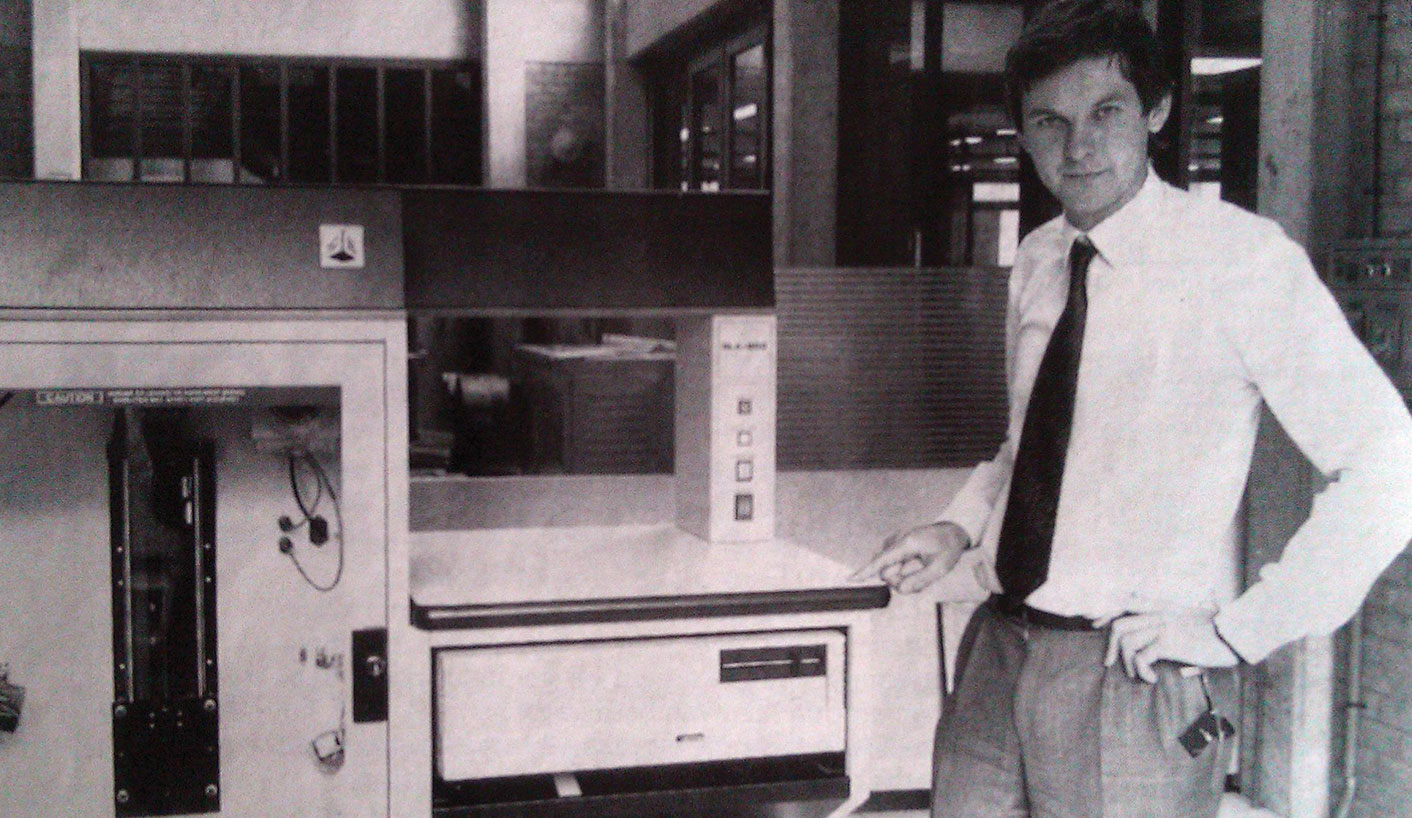
A Man, a Machine, a Mission
From the very beginning, Wilfried Vancraen had a clear goal in mind. He knew 3D Printing could make a difference in the world, but it had to be used effectively and responsibly. Starting out with one Stereolithography machine in a small office at the Catholic University of Leuven, Fried started developing Materialise’s first applications and 3D printing software.
Mapping the Anatomy in 3D
With his background in Biomechanics, Fried saw an obvious link between sliced image data and 3D printing technology. Using 3D Printing in healthcare was an obvious step – together with Bart Van der Schueren, one of Materialise’s first employees and now CTO, the team created specific software that would help Materialise produce anatomical models for doctors using CT image data. Materialise Mimics was born, and we later introduced it on the market so that other companies and hospitals could benefit from it as well.
Tackling the First Hiccups with In-House Software
From the very start, one particular problem kept resurfacing: the difficulty of making files readable for the 3D printer. The only technology which was available at the time was Stereolithography, which still had a long way to go in terms of user-friendliness. Our current Executive Vice President, Johan Pauwels, then a freshly graduated student, rolled up his shirt sleeves and set about creating software that would make files 3D printable, as well as implementing features such as support generation to optimize designs for printing. It worked so well for us that we thought we might as well share it with the rest of the industry; and today Materialise Magics is a benchmark for data preparation software in the market.
Printing Detailed One-Off Components with Vacuum Casting
Vacuum Casting opened fascinating new possibilities for product development. 3D Printing was a great deal less sophisticated then than it is today, and at the time there was a demand for small prototype series made with higher quality materials. The technique involves creating one master part – which we did using Stereolithography – and then casting several copies of it with a silicone mold. By combining 3D Printing and the more traditional Vacuum Casting, Materialise was able to start quickly producing small batches of 20-30 plastic components of the highest possible quality with all the design freedom of 3D Printing.
Stereolithography Printing … in Multiple Colors
With the introduction of color printing, it was possible to make each anatomical model even more personal and informative. We were the first company in history to provide multiple colors in a single Stereolithography model, and this technology allowed us to highlight certain parts of the anatomy such as nerves or tumors, making it easier for surgeons to plan operations.
Supporting Dental Surgery from Digital Planning to Drill Guides
From anatomical models, we progressed to actually making 3D-printed guides which could be used during surgery to show surgeons exactly where they needed to cut and drill the bone to apply implants. We focused on Dental healthcare in particular, and created Materialise SimPlant software, which allowed the surgeon to virtually plan their surgery before even looking at the patient – and then based on this virtual anatomical model, we would 3D print the customized drill guides required for the operation.
NextDay: Our Online Ordering Service before ‘Online’ Existed
In 1997, the internet was taking its first fledgling steps into mainstream consciousness. Ever the tech geeks, we immediately saw how it could be a useful tool for our prototyping and manufacturing services. As one of the first online ordering systems, Materialise NextDay was launched (later becoming Materialise OnSite), allowing our customers to instantly send over data, which we would then turn into prints and ship by the next day. We automated most of the production process and seriously optimized our internal production capacity – all of which allowed us to get prints to the customer in record speed.
Enabling Functional Prototype Testing with Laser Sintering
We acquired our first Laser Sintering printers, which enabled us to move into a whole new world of different applications. Our aim was to produce truly functional prototypes for product testing, from one-off models to small series, using our new technology to create meaningful applications of 3D Printing.
Mammoth Machines Raise the Bar for Large Prints
Sometimes, size really does matter. In the year 2000, printer bed sizes on the market simply weren’t large enough for the projects our customers were commissioning, particularly prototypes for the automotive industry. So we decided to build our very own Mammoth Stereolithography machines. Currently among of the largest machines for Stereolithography, the Mammoth printer can produce an entire car dashboard in one build.
RSM Revolutionizes the Hearing Aid Industry
Customizing hearing aids used to be quite the labor-intensive process, and production was slow and expensive. Together with Phonak, we developed Rapid Shell Modeling software, which automated the design process of each patient-specific hearing aid shell until it took under 10 minutes to create a shell. The file is then printed out, creating a hearing aid which perfectly fits the customer. Our co-creative partnership changed an entire industry, as 99% of the world’s hearing aids are now made with 3D Printing.
.MGX Enters the Design Scene with Bold New Creations
.MGX by Materialise set out to prove that 3D Printing could not only be used for prototypes, but for sophisticated end-use products too – from lamps to furniture and sculptures. Designs like the iconic One_Shot by designer Patrick Jouin also explored new possibilities afforded by 3D Printing, such as integrated hinges, and woke the manufacturing industry up to the fact that 3D Printing was now capable of real manufacturing and ready to make the shift.
Filaments and Functional Models: FDM Comes to Materialise
In December 2003, we brought Fused Deposition Modeling (FDM) printing into our production facilities. Although slower, FDM offered parts with a high degree of strength and structural stability, using true production-grade thermoplastics like ABS, which gave the technology certain advantages over Laser Sintering. By expanding our variety of technologies on offer, we were able to serve our customers better while improving and adapting our software to include this new technology.
Editing in STL Becomes a Reality
Before Materialise 3-matic came along, editing files in STL (the most common file format read by 3D printers) was tricky at best. Engineers needed to go back to their CAD program, make the changes there, and then convert to STL again. It was just as time-consuming as it sounds and in 2004 we commercialized Materialise 3-matic, which enabled users throughout the 3D printing industry to edit in STL directly.
Materialise OnSite: A Step Up from NextDay
By 2004, the internet had matured considerably. We knew that it was time to expand our online ordering services to reflect the needs of our customers. Enter Materialise OnSite, the new version of NextDay, which allowed the customer to virtually follow the process of their order. OnSite also offered our entire range of 3D printing technologies, as opposed to just Stereolithography.
RapidFit: The Game-Changer in Automotive Tooling
A good prototype should mimic the end part as closely as possible. But while shipping larger prototypes to our customers in the automotive industry, we were faced with the challenge of getting these parts to their destination without deforming. We came up with an innovative solution of 3D-printed jigs and fixtures which held the parts in place, and which we could adapt to each different build. This evolved to become RapidFit, which now combines these jigs and fixtures in one standardized system which is used for quality testing in the automotive sector.
Titanium Skull Implants That Act Like Bone
We acquired OBL, a company specialized in the creation of custom CMF implants. Paired with our expertise in 3D Printing, we were able to start manufacturing 3D-printed cranio-maxillofacial implants in titanium, which enabled the surgeon to achieve a much more anatomically correct final result than with a standard implant. The intricate porous structure, made possible with 3D Printing’s freedom of design, allows the implant to behave like natural bone and mimics its mechanical and thermal properties; even facilitating bone ingrowth. This significantly increased the level of comfort for patients undergoing cranio-maxillofacial after surgery.
Less Invasive, More Personalized Surgical Knee Guides
After the success of SimPlant, it made sense to expand Medical 3D Printing to the field of orthopedics. We started printing out surgical guides for knee surgeries in particular, which would enable surgeons to cut and drill bone through precisely calculated openings. This helped make surgery more precise and predictable, leading to improved patient outcomes.
Simplifying Cranio-Maxillofacial Surgery and Introducing Dedicated Clinical Engineers
What we did for knee surgery we then did for cranio-maxillofacial surgery. Recognizing the complexity of ordering anatomical models at the time, Materialise introduced a simpler web-based system that revolutionized CMF. Users were now able to visualize the patient’s anatomy in 3D and then order the relevant model with Materialise SurgiCase. We also introduced dedicated clinical engineers, who work together with doctors on each specific case to design the necessary guides and implants.
Automated Support Structure Speeds Up 3D Printing Production
To further improve the 3D printing process, we created Materialise e-Stage to automate the design of support structures for Stereolithography models, increasing efficiency. Again, the idea for this software module sprung from an obstacle we encountered on our own production floor. As our Stereolithography offer expanded, we saw that it would not be feasible to keep hiring extra staff just to create support structures manually. So we challenged our software developers to come up with a program which created these structures automatically – helping us and our customers save time and use less material as a result.
Presenting Patient-Specific Hip Implants
From anatomical models and surgical guides, we progressed to patient-specific implants for the hip. In challenging surgeries, these implants help patients walk again. We focused on complex hip surgeries with our aMace implants. The implants fit the patient’s anatomy exactly and are designed with a specialized structure that encourages bone ingrowth.
i.materialise Brings 3D Printing to the Public
At this point, 3D Printing was growing outside of the manufacturing industry and the first desktop 3D printers were starting to get attention. We wanted to make it possible for anyone and everyone to print their ideas using professional-quality equipment, so we launched a brand new online platform called i.materialise. People with an eye for design and a head full of ideas were now able to create, share, and sell designs from a single platform.
Crystallizing Motion with Iris van Herpen’s 3D-Printed Dresses
Dutch fashion designer Iris van Herpen launched her Crystallization collection, working together with Materialise and designer Daniel Widrig to create one of the first 3D-printed fashion pieces ever to appear on a runway. We would go on to create several more 3D-printed dresses with her, exploring the possibilities of unlimited freedom of design and material properties to demonstrate to the world what 3D Printing was truly capable of.
Linking Computer to Printing Machine
There are countless different printers, made by different printer manufacturers. Each printer runs on its own specific software, created by the printer manufacturer. Of course, if anyone was starting a 3D printing production facility with more than two 3D printing technologies, it became very complex to connect to these different printers with a computer. We tackled this issue by developing the Materialise Build Processor, which enables different printers to link directly in one program: Materialise Magics. There are currently processors for more than 20 different 3D printing machine manufacturers.
Achieving a Groundbreaking Full Face Transplant
With a team of three other surgeons, Prof. Philip Blondeel at the University Hospital of Ghent successfully performed the first full face transplant in Belgium. This procedure was extremely complex due to the fact that until a donor was available, surgeons couldn’t start planning the operation. Within 24 hours of receiving a donor, the surgery was in part made possible by the use of digital imaging software ProPlan CMF and 3D-printed anatomical models and guides used to plan and execute the surgery.
Keeping the Factory Floor Organized with Streamics
At this point, the 3D printing industry was maturing and starting to work with other, highly regulated, industries. As we started producing series of end-use products, we were faced with the problem of keeping everything traceable and organized. Materialise Streamics was launched as our solution to providing an ever higher degree of quality control, traceability and automation for the 3D printing process. Instead of machine operators having to walk around our facility to check which machines were free, there was now one centralized computer system with all the information. Soon enough, this solution was also helping our customers to streamline their own 3D printing production floors.
Materialise Goes Public
We announced our IPO on NASDAQ on June 25th, 2014. This decision helped us to expand our services, enabling us to help a much wider range of customers and contribute to the growth of the 3D printing industry as a whole.
Making a Difference/A Difference in Making at BOZAR
By the time 2015 rolled around, the 3D printing industry was starting to experience a post-hype hangover. But although the idea of 3D Printing in mainstream consciousness could be misleading, we knew what the technology was really capable of. As part of the second edition of the Materialise World Conference, an event we organized to stimulate discussion about 3D Printing and awareness, we also held a 3D printing exhibition at the BOZAR museum to educate and inform the public, exploring how 3D Printing is helping individuals, enabling social change and contributing positively to the environment.
Looking Good: 3D Prints You Can Wear
Constantly on the lookout for new 3D printing applications with meaning, we produced our first collection of 3D-printed eyewear with Hoet Design Studio. We used our technology to create new, unconventional designs with enhanced customer comfort, with the Cabrio collection marking the beginning of our entry into 3D-printed wearables.
Reaching New Heights in the Aeronautics and Aerospace Market
With an EN9100 and EASA.21G certification under our belt, in addition to the ISO 9001 certification we already had, we were authorized to deliver 3D-printed end-use parts to customers such as Airbus, helping them to reduce weight and operational costs for their aircraft. Our ongoing focus on quality systems from day one made the introduction of 3D Printing into such highly regulated industries a possibility, and cemented our steps into certified end-part manufacturing.
Expanding Our Metal Printing Capacity to New Horizons
Metal 3D Printing became the latest cutting-edge printing technology on the market and soon enough we expanded our own metal capacity, which had begun earlier with the production of titanium implants for our medical customers. We were now able to start offering aluminum printing as well to our industrial customers, and opened an entire metal production facility in Bremen, Germany, on the very same location that our CEO saw his first 3D printer all those years ago. The knowledge we gained in this facility also helped us to create specialized software solutions for Metal 3D Printing.
Materialise Boosts Process Control
Process control has always been important to us, but with our entry into new markets it became a top priority. We integrated the Materialise Control Platform into our services – a software-driven hardware solution which is embedded inside the 3D printer and which gives the user an even higher degree of control over machine parameters and performance.
Materialise Adds Multi Jet Fusion to the Factory for 3D Printing
We were one of the first companies to acquire, and start testing, the new Multi Jet Fusion 3D printing technology. The printer combines powder-based technology with a jetting agent that fuses together the particles instead of a laser. Powered by our Build Processor software, the technology enabled us to start offering functional prototypes and small series with excellent surface quality and low lead times.
Transforming the Eyewear Industry with Yuniku
Working together with lens manufacturer Hoya, we introduced a radical new business model for eyewear which puts the wearer at the center of the picture. Customers are 3D scanned and their eyewear frames are customized for their unique facial anatomy and lifestyle, while preserving the ideal lens orientation.
Further Expanding Competence Centers Worldwide
In our continuous quest towards excellence, we introduced a brand new competence center in Malaysia, which will research and develop new applications for DLP printing technology. Along with seven other competence centers worldwide – which each focus on a different technology – we aim to accelerate the development of our own expertise as well as that of the 3D printing industry in general.
e-Stage for Metal Dramatically Increases Productivity
Materialise e-Stage became the first software in the world to automate support generation for titanium, stainless steel and aluminum 3D-printed parts. Based on a powerful automation algorithm, e-Stage for Metal reduces data preparation time for metal builds by up to 90% and finishing time by up to 50%, giving Metal AM users a dramatic increase in productivity. Additionally, the conditions of the machine operators increase since hardly any powder is captured inside.
ACTech Extends Materialise’s Metal Competences
The acquisition of ACTech brought together the metal competences of Materialise in additive manufacturing with the German-based company’s leading expertise in producing limited runs of highly complex metal parts. The acquisition also enabled Materialise to develop and improve its software suite for Metal 3D Printing through close collaboration with ACTech, taking advantage of learning from an active metal manufacturing environment.
Driving Growth in 3D Printing with BASF
BASF, the largest chemical producer in the world, invested $25 million in Materialise as part of a strategic alliance to identify and develop new applications. The alliance is an acknowledgment of the growth potential of the 3D printing industry, and will build on the combination of Materialise’s software and BASF’s expertise in chemicals to accelerate the development of new applications and create new business opportunities.
The Power of Simulation Brought to the Production Floor
The 2018 release of Materialise Magics software brought an integrated Simulation module. This new technology makes simulation accessible to a wider audience, helping production operators to optimize the production process without the need for expert knowledge. The Simulation module presents an opportunity for production operators to optimize their machine operations and get builds right the first time, raising their overall productivity and making it possible to scale up their operations.
Materialise Brings a New Dimension to Eyewear Customization
The COSMOS eyewear collection by Berlin-based designer fmhofmann became the first in the industry to combine a titanium 3D-printed hinge with 3D-printed PA frames, a unique combination not seen before. The same year, a partnership between Materialise, designer Sébastien Brusset and L’Amy saw a new eyewear range for automotive brand McLaren named ‘Frame Technological Innovation’ of the year at the 2018 Silmo d’Or Awards in Paris. These developments marked further evidence of 3D printing’s growing importance to the eyewear industry, and of Materialise’s commitment to advancing adoption of the technology.
Materialise Receives FDA Clearance for Diagnostic 3D-Printed Anatomical Models
Materialise became the first company in the world to receive FDA clearance for software intended for 3D printing anatomical models for diagnostic use in US hospitals. Materialise Mimics inPrint, a 3D visualization and print preparation software, thereby became the first 510k-cleared software available for hospitals seeking to set up Point-of-Care 3D printing facilities. This meant a step further in enabling patient-specific care and increasing the implementation of 3D printing at the point-of-care.
Producing the First 3D-Printed Parts to Be Placed in Airbus Aircraft Cabins
Materialise partnered with Airbus to produce the first 3D-printed parts to be placed in the cabins of Airbus’s commercial aircraft, where they are visible to passengers. The 3D-printed spacer panels, used for overhead storage compartments, are 15% lighter compared to conventionally manufactured counterparts. Using Materialise’s Certified Additive Manufacturing services, Airbus was able to realize lightweight bionic panels within tight timeframes and achieve the optimal mass for the component.
Materialise Partners with Fluidda to Develop Personalized Pulmonary Solutions
Building on the two companies expertise — Materialise with medical 3D planning and printing and Fluidda respiratory imaging technology — the partnership aims to develop more personalized solutions that can help the growing number of patients suffering from chronic obstructive pulmonary disease (COPD), asthma, and other respiratory diseases.
Cardiovascular Planning Software Suite Receives FDA Clearance
Mimics Enlight is based on the strengths of Materialise’s Mimics Innovation Suite, which has helped clinicians produce patient-specific 3D models for more than 20 years. The software is the first of its kind to include consistent methods of taking critical measurements, a direct link to a 3D print, and interactive case sharing. This enables clinicians to reliably plan and screen patients for cardiovascular procedures, particularly for transcatheter mitral valve replacements.
Engimplan Joins Materialise to Bring Benefits of Personalized 3D-Printed Implants to Brazil
Surgical planning and 3D printing are increasingly adopted by orthopedic and CMF surgeons, as they understand the positive impact of personalized implants and patient-specific solutions on surgical outcomes. The combination of Materialise’s expertise in 3D-printed medical solutions with Engimplan’s innovative product portfolio aims to accelerate the introduction of 3D-printed, personalized implants and instruments in the Brazilian market.
Using 3D Printing Technology in the Fight against COVID-19
One of the main strengths of 3D printing as a manufacturing technology is its speed. This feature is ever more important during the current COVID-19 pandemic in which our healthcare systems and everyday tasks have crossed unprecedented hurdles. In accordance with the company’s mission to create a better and healthier world, Materialise has developed new solutions, from hands-free door openers to masks to help COVID-19 patients, to help individuals stay safe and healthy.
Materialise Launches Mindware, an Advisory Service for 3D Printing
Materialise Mindware offers business managers a direct line of access to strategic, tailored advice on using 3D printing to address their business needs and challenges. Clients receive customized insights from specialists in disciplines ranging from R&D, to design and engineering, to process engineering, as well as specialists dedicated to verticals such as the medical and aerospace industries.