Powder based 3D printing,
without the lasers
HP spread waves of excitement throughout the 3D printing world with the announcement of the Multi Jet Fusion (MJF) technology. Discover the new technology that is ideal for when you need short lead times, low porosity and excellent surface quality, for functional prototypes and small series.
Why choose Multi Jet Fusion?
Multi Jet Fusion uses a fine-grained materials that allows for ultra-thin layers of 80 microns. This leads to parts with high density and low porosity, compared to parts produced with Laser Sintering. It also leads to an exceptionally smooth surface straight out of the printer, and functional parts need minimal post-production finishing. That means short lead times, ideal for functional prototypes and small series of end-parts.
Ideal applications for Multi Jet Fusion
- Low-volume production of complex end-use parts
- Prototypes for form, fit and function testing
- Prototypes with mechanical properties to rival those of injection-molded parts
- Series of small components as a cost-effective alternative to injection molding
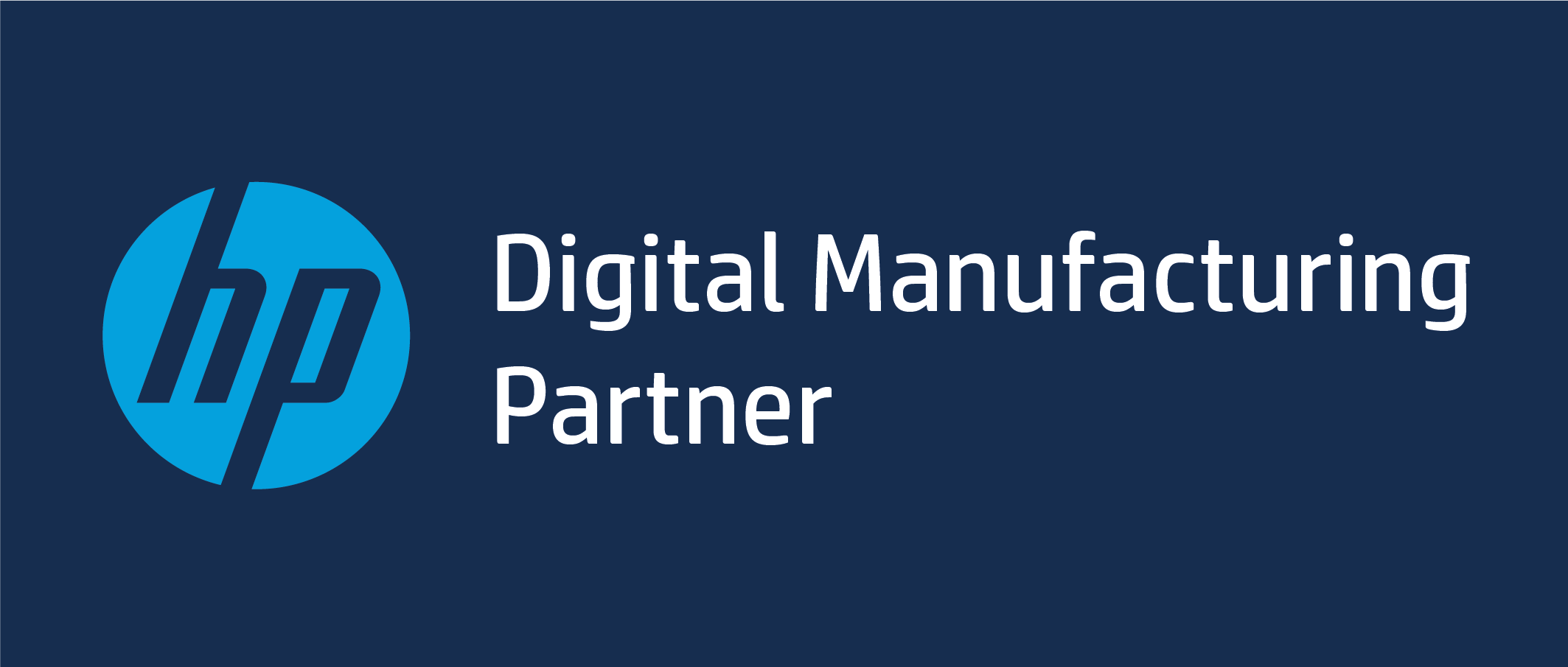
As a proud member of HP’s Digital Manufacturing Network, we’ve been fully qualified by HP and recognized for the excellence of our 3D production and quality processes.
Technical Specifications
Standard lead time |
Minimum of 4 working days, depending on part size, number of components and finishing degrees |
Standard accuracy |
PA12: ±0.3% (with a lower limit on ± 0.3 mm) |
Layer thickness |
0.08 mm |
Minimum wall thickness |
1 mm, but living hinges are possible at 0.5 mm |
Maximum build dimensions |
370 x 274 x 375 mm |
Surface structure |
Unfinished parts typically have a smooth surface, without visible layers, and a stone-grey color. Multi Jet Fusion parts can be sandblasted and colored/impregnated. |
Your 3D Printing Toolkit
How Does Multi Jet Fusion Work?
Multi Jet Fusion is a powder-based technology but does not use lasers. The powder bed is heated uniformly at the outset. A fusing agent is jetted where particles need to be selectively molten, and a detailing agent is jetted around the contours to improve part resolution. While lamps pass over the surface of the powder bed, the jetted material captures the heat and helps distribute it evenly.
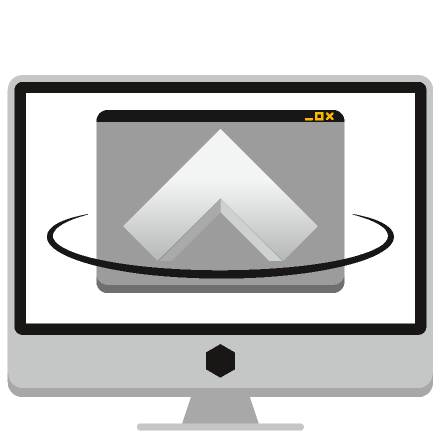
The 3D model
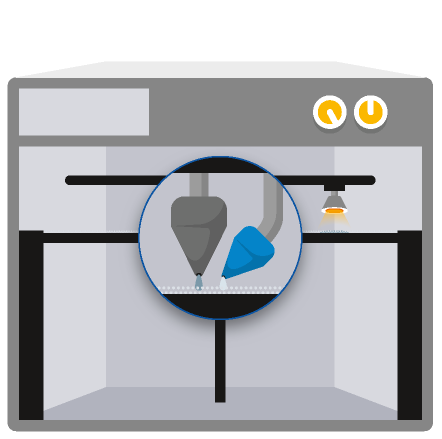
A fusing agent and a detailing agent are jetted to selectively melt powder particles and improve resolution
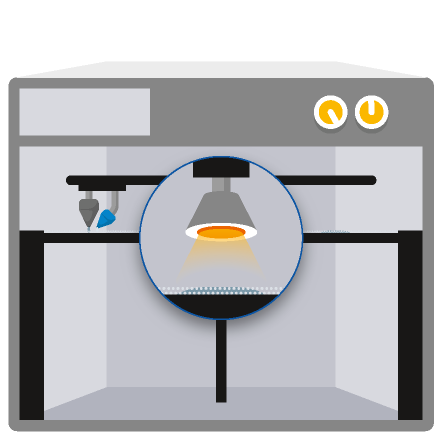
Lamps pass over the surface constantly, the jetted material captures and distributes the heat
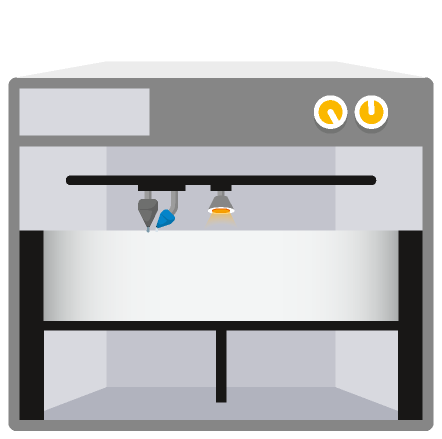
The process continues building up the part layer by layer
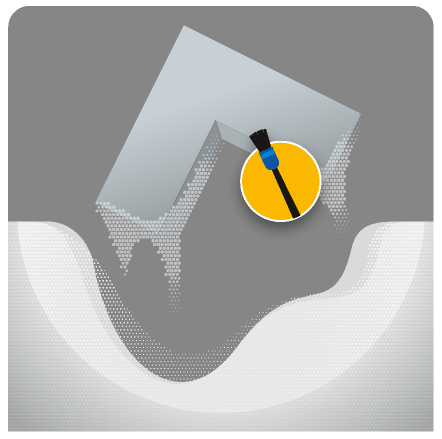
The loose powder is removed
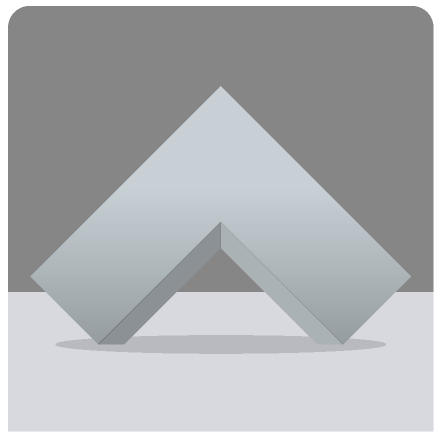
The part is finished
We'd love to hear about your projects and see how we can help.