Ultrasint TPU 90A-01, a thermoplastic polyurethane, is a fully-functional and flexible material with high elongation at break. Ultrasint TPU 90A-01 combines durable elasticity with good wear resistance and abrasion resistance, making it an ideal material for prototyping and manufacturing applications that require good shock absorption and rubber-like elasticity over a wide range of temperatures. Produced with Multi Jet Fusion technology, Ultrasint TPU 90A-01 exhibits smooth surfaces and high detail.
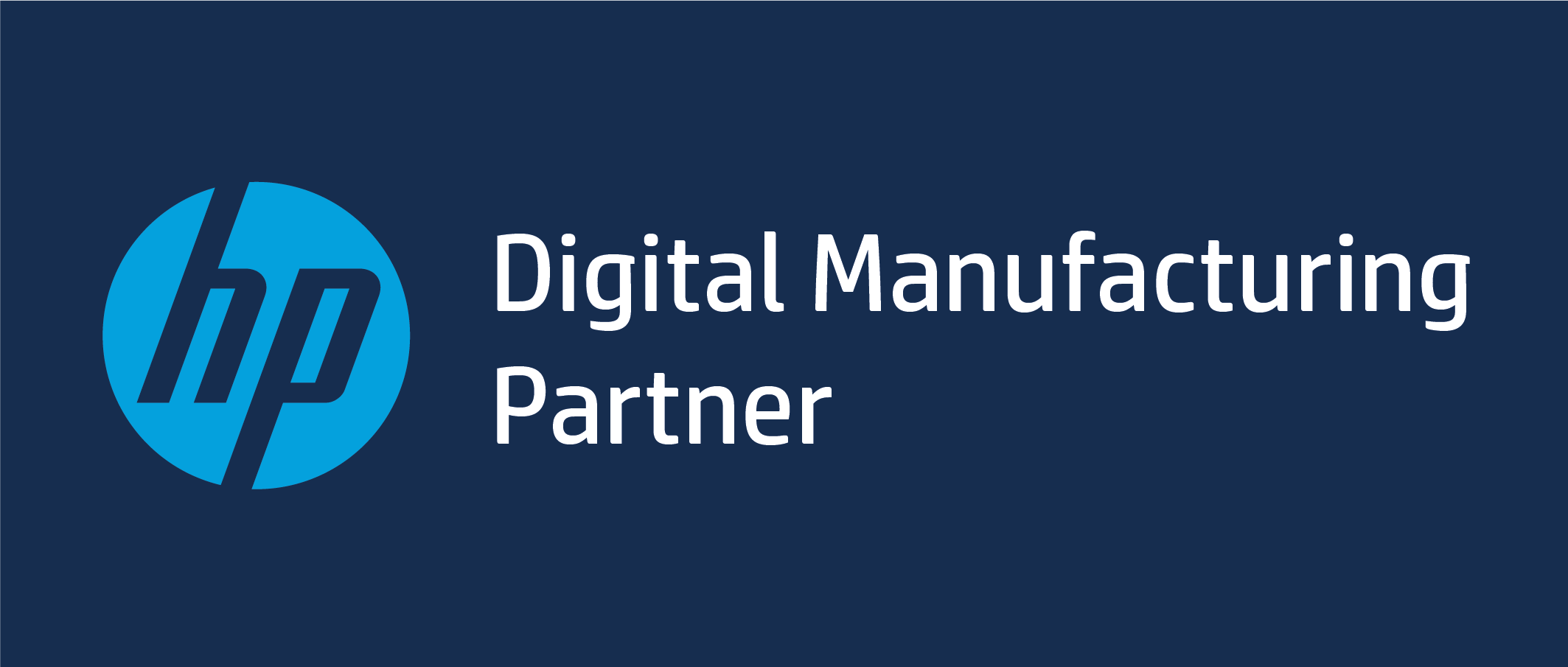
As a proud member of HP’s Digital Manufacturing Network, we’ve been fully qualified by HP and recognized for the excellence of our 3D production and quality processes.
Technical Specifications
Standard lead time | Minimum of 4 working days (online & offline orders) |
Standard accuracy | ±0.9%(XY) up to ±1.8% (Z) with lower limits on ±1 mm (XY) up to ±1.5mm (Z) |
Layer thickness | 0.1 mm |
Minimum wall thickness | 1 mm |
Maximum part dimensions | 370 x 274 x 375 mm (online & offline orders) |
Interlocking or enclosed parts? | Yes |
Surface structure | Unfinished parts typically have a smooth surface, without visible layers, and a stone-grey color. |
Datasheet
MEASUREMENT | VALUE X Y | VALUE Z | STANDARD | |
---|---|---|---|---|
Density | 1.1 | 1.1 | g/cm³ | |
Hardness Shore A | 88 | 88 | DIN ISO 7619-1 | |
Tensile Strength | 9 | 7 | MPa | DIN 53504, S2 |
Tensile Elongation at break | 220 | 120 | % | DIN 53504, S2 |
Tensile Modulus | 75 | 85 | MPa | ISO 527-2, 1A |
Flexural Modulus | 75 | 75 | MPa | DIN EN ISO 178 |
Tear resistance (Trouser) | 20 | 16 | kN/m | DIN ISO 34-1, A |
Tear resistance (Graves) | 36 | 32 | kN/m | DIN ISO 34-1, B |
Compression set B (23°C, 72h) | 20 | 20 | % | DIN ISO 815-1 |
Rebound resilience | 63 | 63 | % | DIN 53512 |
Abrasion resistance | 140 | 100 | mm3 | DIN ISO 4649 |
Charpy Impact Strength (notched, 23°C) | Partial Break | No Break | DIN EN ISO 179-1 | |
Charpy Impact Strength (notched, -10°C) | 21 | 29 | kJ/m2 | DIN EN ISO 179-1 |
Rossflex testing (100k cycles, 23°C) | No Cut Growth | ASTM D1052 | ||
Rossflex testing (100k cycles, -10°C) | No Cut Growth | ASTM D1052 | ||
Vicat/ A (10N) | 84 | 96 | °C | DIN EN ISO 306 |
Melting temperature | 120 – 150 | 120 – 150 | °C | ISO 11357 (20K/min) |
Actual values may vary with build condition
How Does Multi Jet Fusion work?
Multi Jet Fusion is a powder-based technology but does not use lasers. The powder bed is heated uniformly at the outset. A fusing agent is jetted where particles need to be selectively molten, and a detailing agent is jetted around the contours to improve part resolution. While lamps pass over the surface of the powder bed, the jetted material captures the heat and helps distribute it evenly.
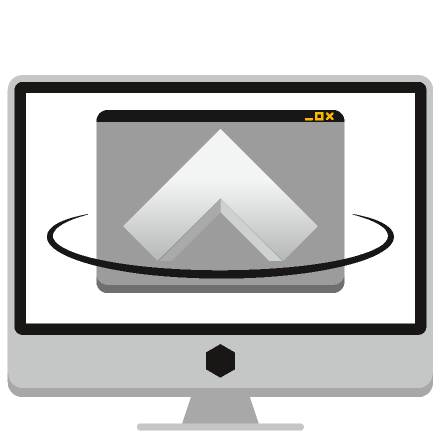
The 3D model
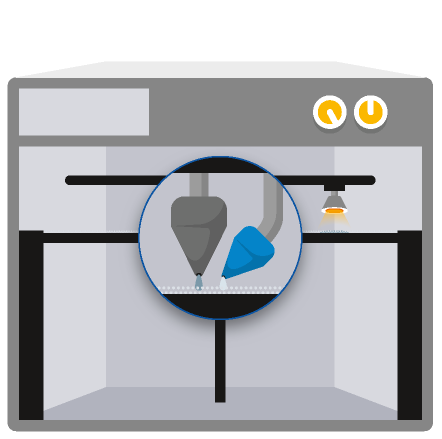
A fusing agent and a detailing agent are jetted to selectively melt powder particles and improve resolution
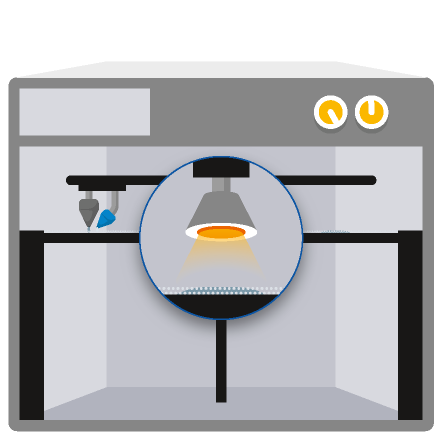
Lamps pass over the surface constantly, the jetted material captures and distributes the heat
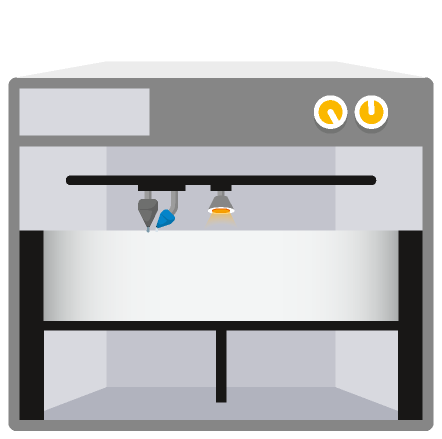
The process continues building up the part layer by layer
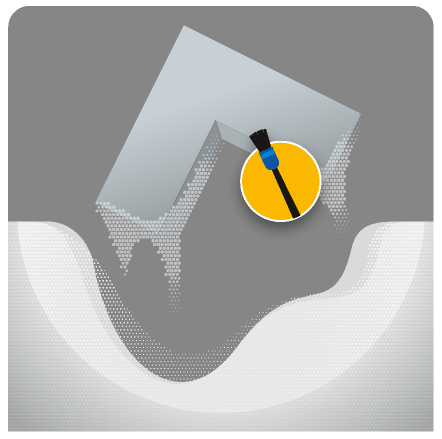
The loose powder is removed
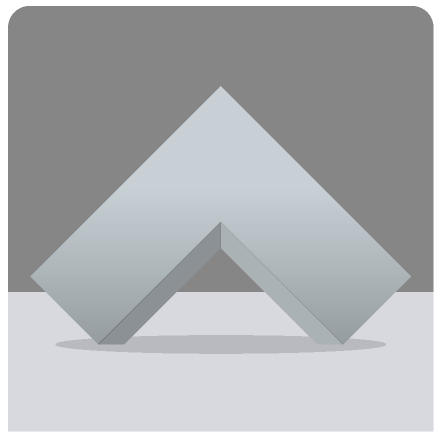
The part is finished