SOFTWARE
Japan’s Metal 3D Printing Pioneer Reduces Casting Lead Time by 90%
Koiwai offers casting services for automobile companies and was one of the first companies to take full advantage of 3D Printing in Japan. Having invested in Metal 3D Printing since 2013, the company is a leading force of innovation in Japan’s metal manufacturing industry. How did they transform their casting process? How do they deal with the challenges of mass producing metal parts? And where do they see the real value of 3D Printing?
Accurate and complex casts in one day
Koiwai has been devoted to manufacturing foundry parts for over 40 years. Until they introduced 3D printers in 2007, they mainly used wooden molds for casting. It takes about 10 days to complete the casting with this manufacturing method, because it is necessary to manufacture a sand mold after completing the wooden mold, which requires a machining tool and manual labor from a craftsman.
When customers asked for sand molds with high precision and complex shapes in a short time, Koiwai decided to incorporate 3D Printing into their casting business and as a result they greatly changed their industry practice. With 3D Printing and advanced data preparation software, Koiwai can directly form the data, so the casting is achieved without labor-intensive wooden molds. As a result, the construction period was shortened to one tenth of the time the original wood construction method took. Furthermore, by using 3D Printing, it is possible to produce sand molds of complicated shapes which were difficult to produce before.
Also read how RP Cast transformed their casting business.
What about the mass production of Metal 3D Printing?
Many products mass-produced with Metal 3D Printing are used for long-term goals, such as aircraft engine nozzles and medical implants. In order to safely use these parts, it is important to record huge amounts of information on the production process, such as which 3D printer was used, when and under which condition the parts were made, and more. Companies need to be able to access this information at any time. If you are producing large quantities of parts of equal quality using multiple 3D printers, the importance of a sophisticated quality control system is even higher.
Companies such as GE that have already begun mass-production by Metal 3D Printing have solved these problems using AM production management software Materialise Streamics. At Materialise, we use it to manage over 140 professional 3D printers. And now Koiwai will use it to supervise the additive production of their medical artificial joints, implants, rocket engine parts and automotive engine parts. Materialise Streamics will help them expand the metal production of their precision parts. The production management system is designed to strengthen the metal 3D print service for industries where high standards are demanded.
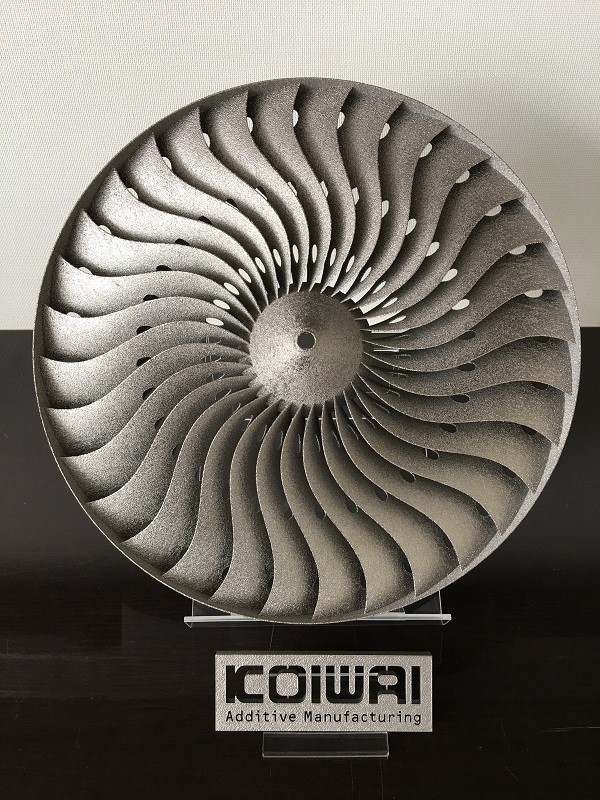
Image showing tree support (left) and block support (right)
The best application for 3D Printing
3D Printing is starting to be recognized as a major manufacturing technology. However at this moment, it is still cheaper to use conventional manufacturing techniques if you want to mass produce simple parts. The application that can really make use of the strength of 3D Printing is mass customization, which makes different products in large quantities one by one, ideally with a complicated structure that can’t be realized with other technologies. For example, lightweight or structures with an optimized topology often have very complex designs, and can only be produced using 3D Printing.
To optimize designs with lightweight structures or to make topology-optimized structures printable, Koiwai uses Materialise 3-matic software. This software also enables the user to apply aesthetic or functional textures to 3D models and customize them according to their needs. Materialise software will support Koiwai in expanding advanced manufacturing that maximizes the value of 3D Printing in Japan and Asia in general.
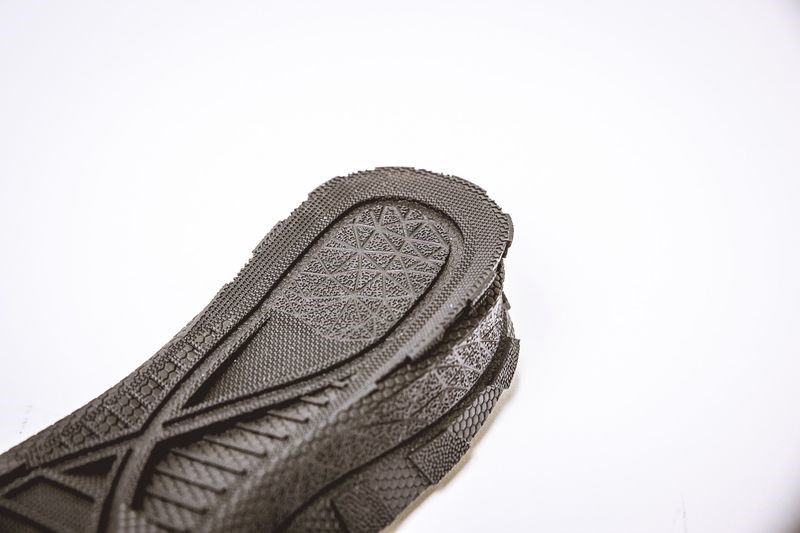
Textured master of a shoe sole, produced by Materialise using Materialise 3-matic
Koiwai has revolutionized the casting industry and has led the 3D printing industry in Japan. Both precise production control and design that maximizes the strength of 3D Printing are important factors for this technology to become even more widely spread.
Do you want to bring your 3D printing business to the next level?
Let Materialise help you achieve your goal with the power of our software. Contact us to discover the best combination of our wide range of software for your company!