Dutch company Vanderlande handles logistics automation, making processes in warehouses more efficient and streamlined. Imagine the warehouse of the future, with rows upon rows of crates that seem to know exactly where they’re going. When multinational supermarket chain Albert Heijn was looking for a new, automated layout for its main distribution center, Vanderlande stepped in to provide it. Located in Zaandam next to the Albert Heijn headquarters, the distribution center is vast and supplies hundreds of stores. Of course, that means its mechanized makeover is correspondingly intricate. Vanderlande needed to represent their highly complex automated distribution center with a scale model, so that they could clearly show their clients what the new system offered. For that, Vanderlande and Albert Heijn turned to Materialise.
3D Printing offered the ideal solution for such a complex model – not only was it less costly and faster to 3D print the model, it was also so detailed that making it with another technology would have been extremely time- and labor-intensive. “This was a massive project, with a lot of components and several stages of production and post-production. The actual printing was just one part of it. In choosing Materialise, we went for the partner who could support us at each stage, from engineering and file preparation to finishing and assembly,” says Hilbert Roukema, Albert Heijn.
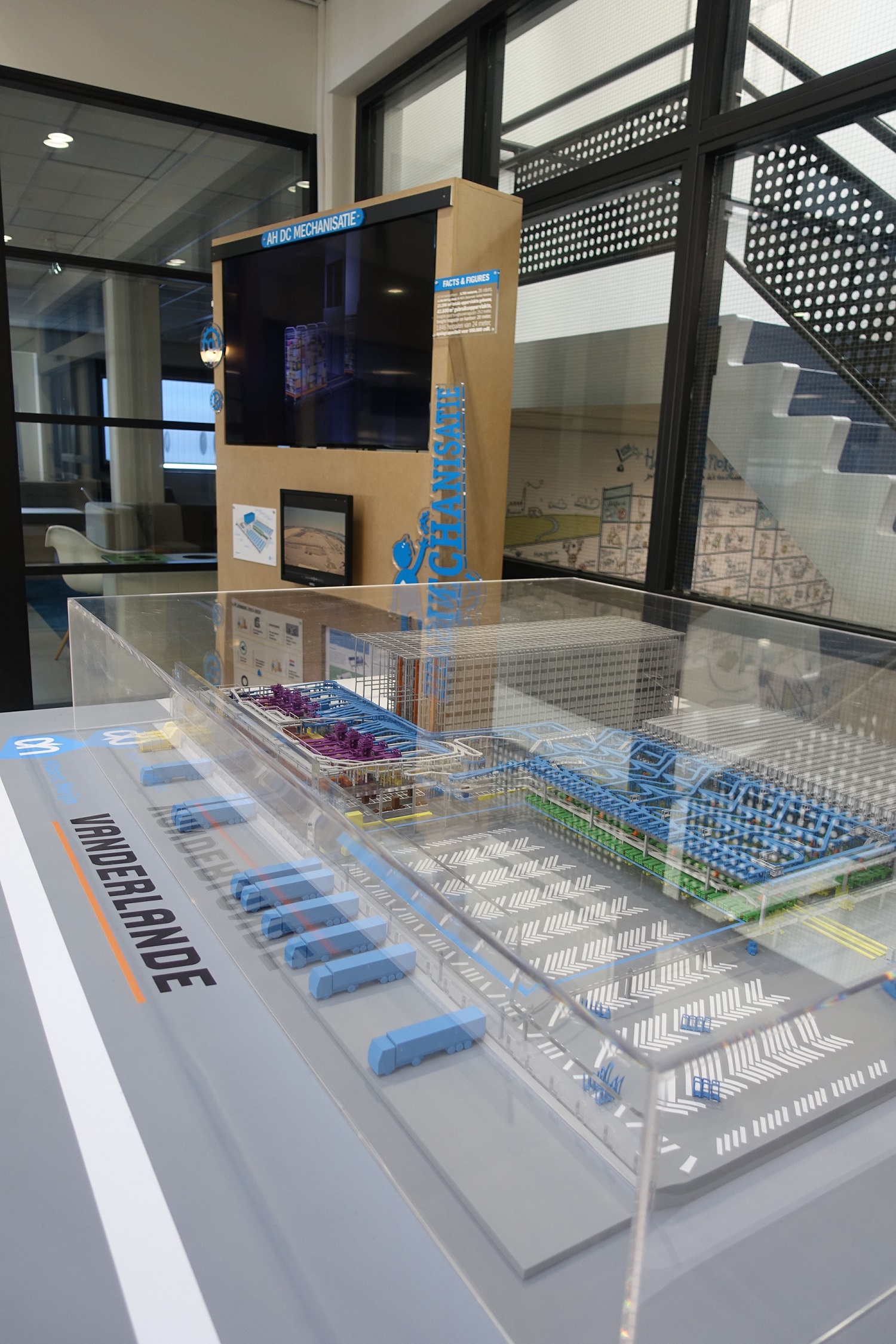
We received the architectural CAD file of the entire building from Vanderlande, and needed to prepare the file for our 3D printers. The file was absolutely massive and immensely complex, with hundreds of small, detailed parts, and no less than four layers. The biggest challenge for our project engineers from Design & Engineering was turning it into a manageable, watertight file ready for 3D Printing – but our build processors and Materialise Magics were up to the task, slicing the file into a size that our 3D printers could process.
Finally, the different components were printed in Stereolithography. A few interior details were printed in Laser Sintering. Stereolithography was chosen for most of the parts owing to two main reasons: its impeccable surface quality and the large build sizes it offers. There was a certain amount of post-processing, such as painting, polishing and assembling (each floor is separated by Plexiglas, enabling viewers to see through the entire model).
“This model has done more than its job as a maquette,” says Hilbert Roukema at Albert Heijn. “Visitors at our distribution centre will see the model to get an idea of how the distribution center works, and we will also use it to train staff about the new organization. It’s great to see such a faithful representation of the automated system!”
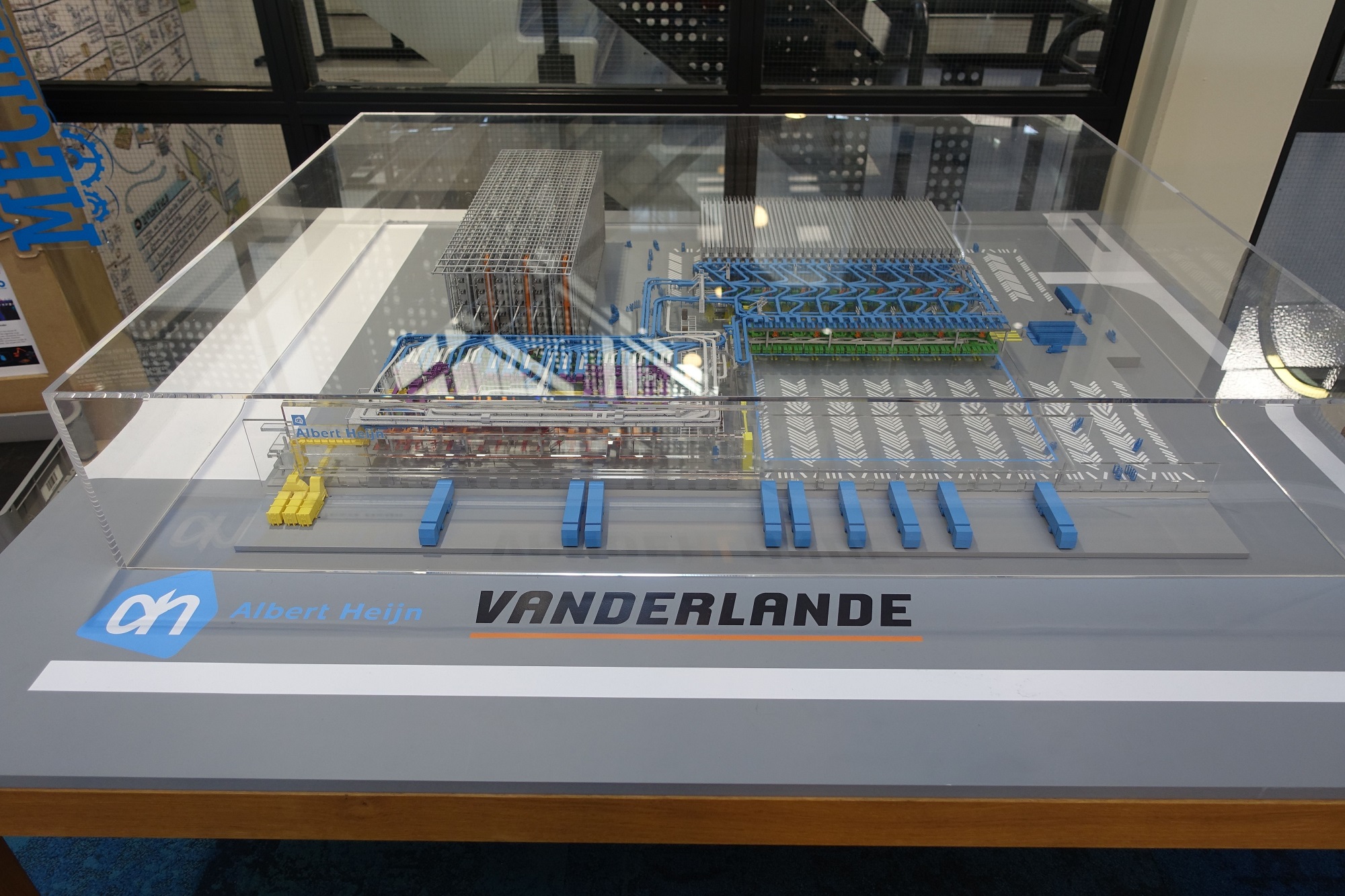