Born with Down syndrome and undergoing treatment for leukemia, at just five years old Jalanea Lowe had already faced more challenges that most of us will in a lifetime. Yet a smile has never been far from her face. A huge personality and the support of an extraordinary family has given her a passion for life that is clear. So when Jalanea was also diagnosed with Atlanto-axial instability — a dangerous point of weakness between spine and skull — clinicians at Ochsner Hospital for Children in New Orleans used 3D anatomical modeling, generated by Materialise’s Mimics inPrint software, to help plan and successfully execute a complicated procedure that would ultimately save a brave little girl’s life.
Delivering life-saving and detail for pre-op planning
Atlanto-axial instability (AAI) is a rare developmental anomaly, a weak point in the join at the top of the spine/base of the skull that results in increased mobility around the cervical vertebrae. For Jalanea, the condition meant it was proving increasingly difficult for her to hold up her head, making many every-day activities more and more impossible. She was having trouble walking and kept falling down. Worse still, the poor connection between skull and spine meant severe paralysis – even loss of life – was a real and imminent threat without immediate surgical intervention.
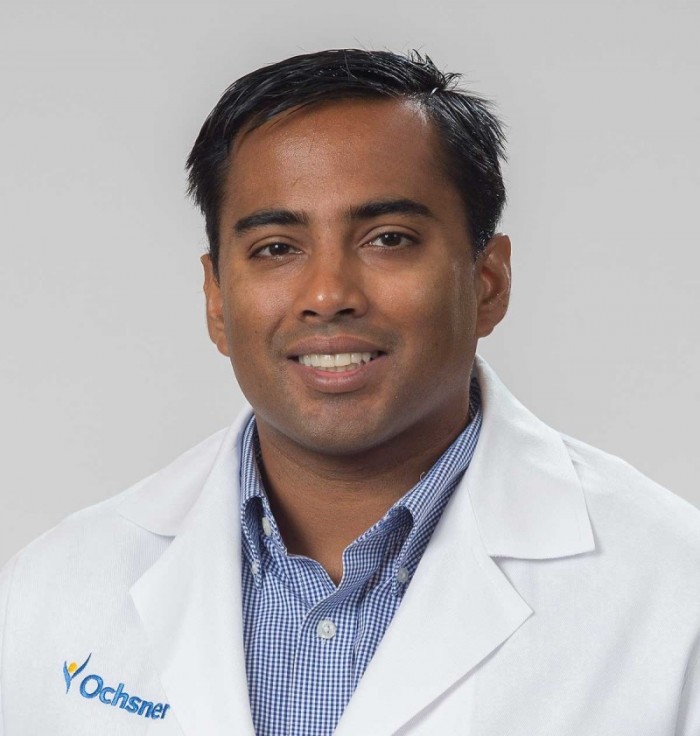
Dr. Korak Sarkar, MD, Ochsner Health System
“To help Jalanea, the team needed to remove a small piece of bone located at this critical juncture, and use screws to stabilize the area in order to prevent damage to her spinal cord,” recalls Dr Korak Sarkar, a neurologist and director of Ochsner’s ‘m3D lab’ dedicated to leveraging new technologies that support state-of-the-art patient care, education and clinical training. A simple aim, but a highly complex and delicate procedure. Paralysis was a certain risk of inaction, but could also be a potential outcome associated with the remedial action required.
“For situations like this, 3D printing or ‘medical additive manufacturing’ is ideal and exactly why we work with partners like Materialise. X-rays, MRI images and CT scans are invaluable for surgical teams in planning their approach, and are typically used in conjunction with generic anatomical models to help map out the procedure well before a patient enters theatre. 3D anatomical models created from a patient’s medical imaging files, however, take this process to the next level by allowing surgeons to see exactly what they will encounter once a patient is on the operating table.”
Turning patient data into peace of mind
In-house capabilities at Ochsner Health System’s m3D lab enable the healthcare provider to print its own 3D anatomical models using techniques such as Stereolithography (SLA) and Fused Deposition Modeling (FDM). But before any model can be created – including the FDM 3D rendering of Jalanea’s spine and skull – it must turn medical image data (DICOM files) into 3D print compatible files. A task Ochsner trusts to Materialise’s medically certified and field proven Mimics inPrint software in combination with an Ultimaker S5 printer.
“In Jalanea’s case the Ochsner team had CT, MRI and 3D echo imaging data as the starting point,” said Todd Pietila, senior biomedical engineer and business developer at Materialise. “These images were processed through inPrint’s segmentation and modeling algorithms to efficiently convert the DICOM information into 3D printable files with required supporting structures to ensure optimal printability of the anatomy. Finally, built-in verification functionality enabled the team to overlay the digital rendition of Jalanea’s model against the initial DICOM data to confirm accuracy and make final adjustments to ensure exact structural replication.”
It’s this level of verifiable accuracy that most appeals to Dr. Sarkar, and not just in terms of its value as a surgical planning aid. “As clinicians, these tools enable us to see the exact task we will face. There is of course reassurance in that. But being able to talk through the process with parents and do so holding a tangible model in your hands to clearly show the surgical steps ahead; that’s powerful. When the team showed Jalanea and her parents the replica of her skeletal structure, they told us it gave them real peace of mind. Comfort. To help people feel that way, during what is an understandably traumatic time, is incredibly inspiring and rewarding. In fact the family loved the model so much that they asked to keep it so that they could explain the process to others.”
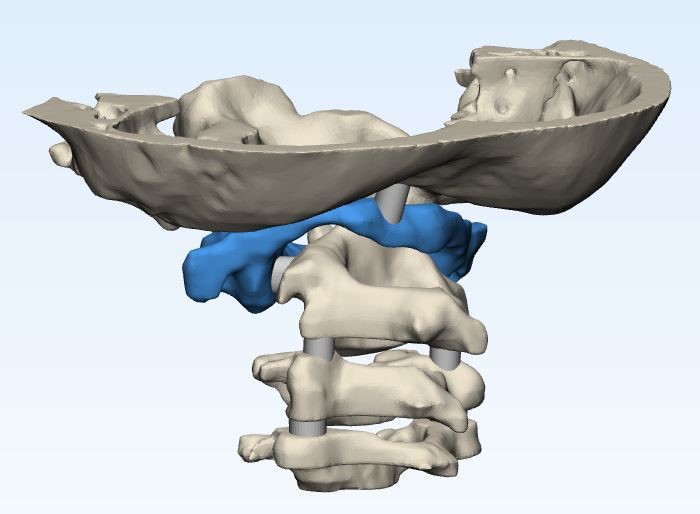
Render of the anatomical model of Jalanea’s spine and skull
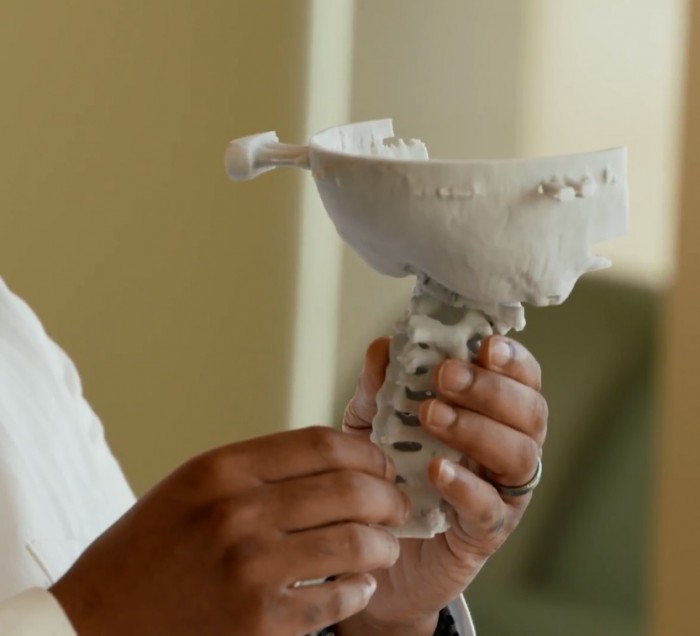
Dr. Sarkar shows the 3D-printed model
A model patient, an ideal outcome
Using the 3D model, Jalanea’s surgery was meticulously planned with all members of her clinical team clear on the specific techniques and steps required for her anatomy. The outcome was a surgical procedure that went exactly as intended. More importantly, a surgical procedure that has helped a five-year-old girl get one step closer to enjoying things she loved to do before the impact of AAI had made some of them impossible.
“Things could not have gone better in this case,” says Dr. Sarkar. “Jalanea has more battles to face but we all feel privileged to have played a part in helping her to get past at least one hurdle, empowering her to keep going and keep smiling. She was a perfect patient and using 3D printing was perfect for her.”
The 3D printing software used by Ochsner Health System integrates into the hospital’s clinical workflow which means models are automatically numbered and logged against patient files for procedural safeguarding. All data used and the 3D printing files developed to create Jalanea’s spinal model will therefore become part of her ongoing patient record, providing a complete, data-rich audit trail of her treatment for future progress assessments and also to help plan any further procedures that may be required down the line.
“Many hospitals outsource 3D anatomical model printing which is great. But for us, being able to bring that expertise in-house — thanks to the functionality and process compatibility of the software we use — means we can respond more quickly to cases like Jalanea’s and integrate this kind of ‘platform technology’ more deeply into our own existing processes. Our aim is to use 21st century technology to deliver 21st century care. Working with Materialise has helped us with this mission.”
Dr. Korak Sarkar, MD, Ochsner Health System
Materialise Mimics inPrint and compatible printers at the Point-of-Care
Point-of-care 3D printing is changing the way physicians interact with medical images. As diagnostic usage of 3D prints created at the Point-of-Care is increasing, scrutiny around the safe and effective use of this technology is required to provide healthcare providers with peace of mind. Materialise has the mission to provide products to the market that result in a better and healthier world, reflected in its ambition to create a safe environment to enable hospitals to 3D print at the Point-of-Care.
Increasing amounts of hospitals are turning to 3D printing of models as a tool to support complex cases, through multidisciplinary discussions and pre-surgical planning. The current method of choice for implementing 3D printing in hospitals is with a point of care 3D printing facility, leveraging in-house engineering and printing capabilities insides the institution.
Materialise Mimics, introduced to market in 1992 enables researchers and engineers to create accurate 3D models using medical imaging processing software. Materialise Mimics Inprint, released in 2016, allows users to create 3D printable medical models without advanced clinical engineering support. In March 2018, Materialise became the first company to receive FDA clearance for Mimics inPrint intended for 3D printing anatomical models for diagnostic use.
To further establish Materialise software as the reference in the market for 3D printing in hospitals, Materialise aims to build up the list of compatible printers and materials in the coming years. Materialise has engaged in partnerships with Formlabs, Stratasys and Ultimaker to identify compatibility for printers and materials with the Materialise Mimics inPrint software, identifying three compatible printers by performance testing.