Materialise e-Stage for Metal
Materialise e-Stage for Metal is software that automates the support generation process for metal parts. This automation allows you to reduce costs, especially those related to man hours. The powerful algorithm reduces data preparation time for metal builds by up to 90% and finishing time by up to 50%.
You can tweak the algorithm in the extensive parameter list to optimize it for your machine, material and part geometry, ensuring that all of your builds are created successfully. The support structure design allows you to remove nearly 100% of the powder from the support structure.
Save time on
Data Preparation
There’s no need to spend large parts of your time on editing metal supports. With this fully automated software for Metal 3D Printing, you`ll have:
of the time spent
on support design
Build Process
With Materialise e-Stage, you can place parts directly onto the platform, resulting in a faster build time. Afterwards, you can use a wire EDM to remove the parts from the build plate.
Support Removal
To ensure that you can easily break off support, Materialise e-Stage generates needle-thin contact points. The flexible grid structure makes it possible to remove parts from the support structure without any tools. Support removal has never been so easy.
reduction in support
removal time
Finishing the Parts
With Materialise e-Stage, support structures are generated only where needed and even avoid contact with the part as much as possible to keep finishing work to a minimum.
reduction in part
finishing time
“The support structures generated by Materialise e-Stage led to the same high quality standards as the previous process. The difference is the huge increase in speed for support generation and removal,”
– Clément Barret, AM manager of volum-e
Improve Production
Reduce the risk of build crashes
Since the support generated by e-Stage is created automatically, human errors are excluded.
Every surface that should be supported will be supported. The software also takes into account the force of the recoater (‘horizontal top load’ parameter) in order to prevent crashes caused by the recoater. In addition, it will reinforce the support connections of tall, thin parts to ensure a proper stabilization and prevent deformations while building. You can change the size of these connections in the parameter sets (‘horizontal connection height’ parameter).
Lower the powder consumption
Using the support volume estimation function, you can measure how much material is used. It is always less than it seems due to the lightweight nature of the scaffolds. By using gusset parameters, you can force part-to-part connections in order to lower the powder consumption even more. The support structure of this vacuum gripper was reduced by 63% when applying gussets. In addition, printing gussets requires less time than printing a full structure.
Maximize your build platform
Materialise e-Stage allows you to nest parts in the z-direction without touching part surfaces. You can generate one e-Stage file for all your parts, without taking into account the distance between the parts beforehand. One file per part is also possible. In that case, you can maximize your build space by limiting the width of the support structure with the ‘maximum offset around part’ parameter.
Increase the lifetime of your wire EDM
The open structure of e-Stage prevents powder from getting trapped. Since the wire EDM doesn’t get into contact with the powder, it wears less.
Fully control the support structure
In most cases, the support structure that e-Stage for Metal generates completely meets the needs of our users. In case you would like to change something, though, that is possible. You can still edit and remove the connection points after placement or even add new ones. Once the connection points have their final position, you can easily generate the corresponding support structure.
Improve operator working conditions
e-Stage’s open structure results in less trapped powder in the supports, and consequently less powder in the working area, decreasing risks related to the health and security (HSE) of the operators.
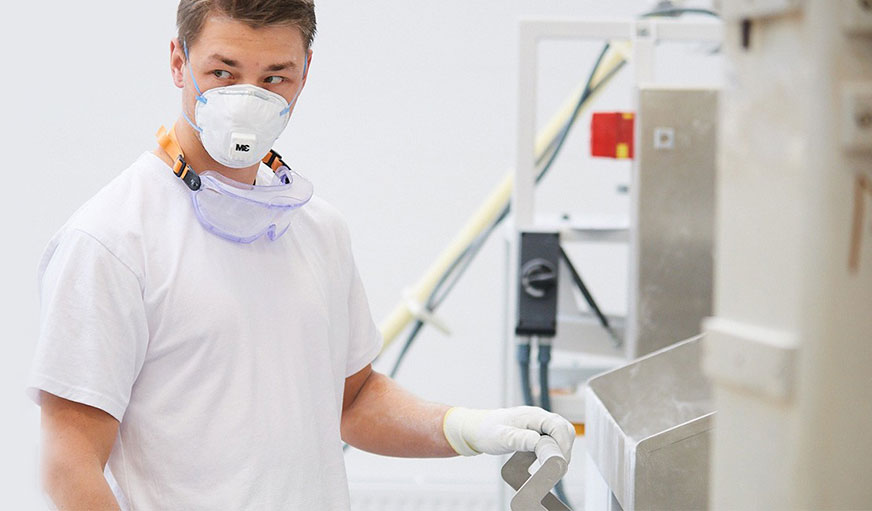