Realize, one of the largest service providers of 3D-printed parts in the Midwest, USA, helps engineers, project managers, company owners and designers make high-quality prototypes with a fast turnaround so they can evaluate their product designs. Materialise software helps them get the job done and maintain the level of service expected by their customers..
Saving Thousands of Man-Hours over the Past Four Years Realize specializes in Stereolithography technology and has no less than twelve SL systems in their recently expanded lab. As everyone familiar with SL technology knows, you need adequate support structures to ensure that your part doesn’t move in the bath of resin. Before using Materialise software, the Realize team prided themselves in using traditional methods to edit, customize, or delete, each and every support structure region. These methods are extremely time consuming and inefficient. Why spend time doing all this work by yourself if you can automate it instead? Realize took the opportunity to test Materialise e-Stage and soon developed custom profiles for all of their machine and material combinations. There’s been no looking back. They can now easily and efficiently customize their support structures while saving a significant amount of time, all with the added bonus of having reduced the number of build crashes. “It was a huge leap of faith to abandon our tried and true methods of supporting SLA parts in favor of the push-button system that is e-Stage. For more than a decade, we were in complete control of support creation, and in 2012, we went all-in based on promises of time savings and fewer build failures,” explains Todd Reese, President of Realize.
“We quickly found that the impact on our business from using this automated support generation method was huge. Time savings were noted immediately, and over the course of a few months, we had seen a dramatic decrease in the frequency of support-related build failures. To say it exceeded my expectations would be an understatement. Since switching to e-Stage, we have literally saved thousands of man-hours in build preparation time.”
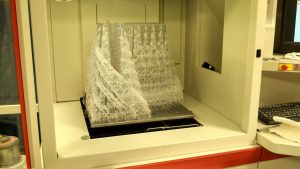
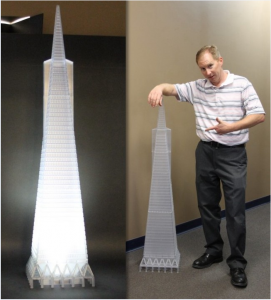
Printing Challenging Geometry Realize didn’t only save a huge amount of time, they also witnessed a significant improvement in the quality of their printed parts.
“Another shift we’ve seen in the landscape is that clients are designing and requesting more and more challenging geometries than ever before. I can think of many successfully completed projects since 2012 that would have been difficult, if not impossible, without e-Stage,” states Reese.
When architectural designer, Adam Voorhees, contacted Realize to create a scale model prototype of the Transamerica Pyramid, they were happy they could rely on our automated support generation software. The 3D-printed skyscraper of 53 inches high (134.62 cm) was successfully printed and exhibited in a museum!
All images: courtesy of Realize, Inc. Take a look at our webpage to discover more benefits offered by Materialise e-Stage. Or try out our automated support software for free!