Orthopaedic plating systems that are currently available on the market to treat bone fractures usually offer standard form plate designs, which don’t always conform to a patient’s anatomy. In the treatment of some periarticular fractures, this can be rather problematic. This fact was noted by Prof. Dr. Stockmans, who used the Mimics Innovation Suite to change the design of a hand plating system for an optimal fit to the shape of the bone. Through virtual design iterations, the complete product cycle, from concept to market, was significantly reduced compared to traditional methods for altering implant design.
Improving Traditional Plate Design
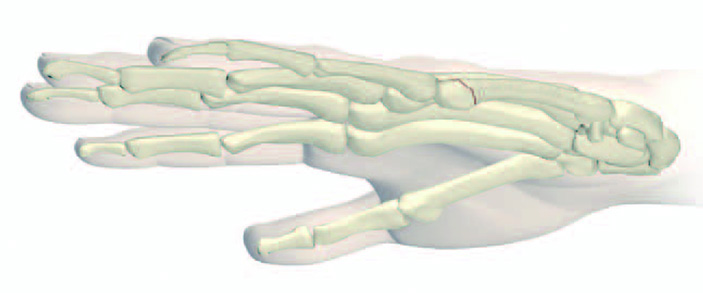
Boxer’s fracture
A fracture of the fifth metacarpal bone, which connects the little finger to the wrist, is commonly called a boxer’s fracture because the end of the little finger’s metacarpal bone breaks when bearing the brunt of the impact. To allow the fractured metacarpal to heal, it must be stabilized with a plate. Traditional hand plating systems offered by orthopaedic device companies did not offer plates with optimal contouring for the treatment of this particular fracture, resulting in unstable anchoring.
Prof. Dr. Stockmans and the medical device company Stryker addressed this problem by using the Mimics Innovation Suite to make several design changes to match the plates to the anatomical shape of the fifth metacarpal. The process began by making 3D reconstructions of the metacarpal 5 of multiple patients from their CT scans. The plate was then virtually positioned on the bone and cut into several pieces using the cutting tools available in the Mimics Innovation Suite. To attain a perfect fit to the bone, the parts were repositioned and subsequently merged to create a redesigned, anatomically correct metacarpal 5 plate.
Old metacarpal 5 plate design
Time from Design to Market
Using patient-specific data to redesign the metacarpal plate gave Prof. Dr. Stockmans confidence that the new design would correctly fit on metacarpal 5 anatomy, resulting in the required immobilization. Stryker’s design engineers used the improved design from Prof. Dr. Stockmans to develop a final design that met their anatomical and manufacturing criteria. This innovative virtual approach eliminated the need for numerous design iterations and the time-consuming and costly process of producing prototypes for validation and optimization
Redesigned metacarpal 5 plate
Thanks to the availability of patient-specific data and the powerful, user-friendly tools of the Mimics Innovation Suite, Prof. Dr. Stockmans and Stryker were able to complete the entire process – from concept to market – in less than three months! The process would normally have taken several additional months and would have required numerous prototypes and costly cadaver labs to come to a final design. The surgical simulation features in Mimics greatly reduced the time-to-market by allowing the team to verify the design and make virtual modifications. The optimized design reduced the operating time by eliminating the need for the surgeons to bend the implant during the surgery.
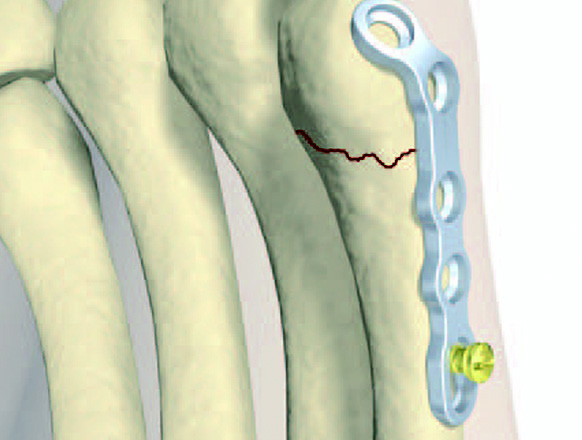
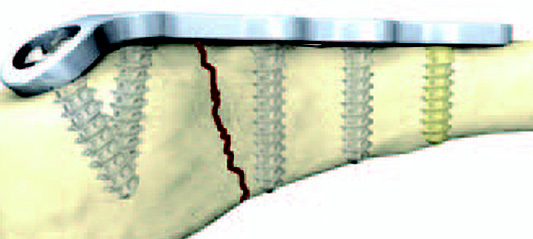
Marketed novel metacarpal 5 plate by Stryker
Medical Image-based Implant Design
By combining medical image data with advanced engineering tools, The Mimics Innovation Suite provides a dedicated platform for surgeons and design engineers to collaborate on the implants of the future. By incorporating feedback from all stakeholders, surgical procedures and patient outcomes can be greatly improved. The benefits of using medical image data as design input were nicely illustrated through this collaboration between Prof. Dr. Stockmans and Stryker.
From Several Scans to Entire Populations
Today, the industry is starting to take this concept to the next level, by using not just several scans as design input, but by instead using hundreds or even thousands of scans. This allows engineering teams to gain a thorough understanding of the anatomical variations in a target population and enables them to design devices that maximize patient coverage while ensuring an optimal fit, in a cost-efficient way. In order to bridge the gap between the large amount of information that is present in image data, and the implant design space, Materialise is offering its anatomical data mining (ADaMTM) population analysis services. Starting from a large number of scans, we extract the average bone shape as well as population variation models, thus providing medical device companies a serious head start in the design of their future devices.
The Standard in 'Engineering on AnatomyTM'
The Mimics Innovation Suite turns 3D image data into high quality digital models in an accurate and efficient way. Starting from CT, MRI or 3D Ultrasound images, the Mimics Innovation Suite offers the most advanced image segmentation, the broadest anatomical measurement options, powerful CAD tools for Engineering on Anatomy and 3D Printing, and accurate model preparation for FEA and CFD.
In this case study, the authors used the Mimics Innovation Suite to improve and significantly accelerate plate design using the following steps:
- Translate CT images into a very accurate 3D model
- Make design changes to the plate to attain a perfect fit to the bone and reduce operation time
- Virtually verify the design, thus reducing the time of the design process.
Would you like to learn more about what Mimics Innovation Suite could do for you? Simply get in touch with one of our specialists. We're looking forward to talking to you!