Making the most of Additive Manufacturing means taking a new approach to design. At Materialise, we believe that design optimization is a constant and crucial process. It’s particularly important when a part goes from traditional manufacturing techniques to 3D Printing, where the same restrictions simply do not apply. In the case of this suction gripper, our Design & Engineering team took the design through multiple stages of evolution until we had a 3D-printed part that costs less than one-third of the original, is nearly a quarter of the weight, and needs no assembly. All that while using the same material: aluminum.
From Milling and Machining…
The picture shows a suction gripper, with internal air channels visible in the front plate. When this project arrived at the Materialise engineering team’s desks, the customer had already partially optimized the part for 3D Printing. While the original part had been produced through milling followed by machining — a long, labor-intensive process — this design was intended for 3D Printing in aluminum. A steel plate, tube and connection arm would then be assembled manually.
The problem? The design was expensive, owing to heavy material usage and a need for manual assembly. The main goal for our engineering team was cost reduction. A secondary goal was to improve the gripper’s lifetime, as the customer’s experience showed that incorrect positioning of the part caused incremental damage over time.
…to Metal 3D Printing
In Additive Manufacturing, generally speaking, design complexity is not a contributor to cost. Volume is, due to the associated material usage. So Materialise engineers first took the opportunity to replace the solid space of the gripper with a leaner version, requiring drastically less material. To reduce the amount of manual assembly required, the team integrated a connection tube within the gripper design. Integrated tubes not only reduce costs, but also remove the risk of leakage.
But the part could still be made lighter, and cheaper. Besides volume, another major cost driver in metal 3D printing is support structure. Any unsupported overhangs could potentially deform during or after printing, owing to the high temperatures that the part is subjected to in the 3D printer — but supports use valuable material and raise costs. So over the next two design iterations, Materialise engineers landed upon a funnel-shaped design and a build-platform orientation that drastically reduced the support structures needed: resulting in an aluminum suction gripper that is only 60g, as opposed to the 237g original.
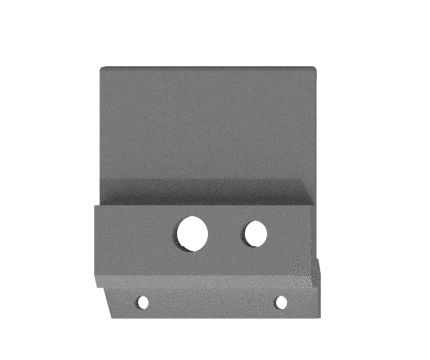
And that 60g includes a new connection arm, integrated into the single-build design, which removes the need for manual assembly. Even better, it ensures correct positioning of the part, by removing the possibility of human error, thereby helping to increase the gripper’s lifetime.
“With the volume reduction and the integrated functionality, we’ve managed to cut down the cost by 70%, with no assembly required. With thoughtful design and engineering, we were able to offer the customer a suction gripper that’s more performant and faster to manufacture, at a far lower price.”
Mathieu Cornelis, Account Manager, Materialise
Want to find out how your projects could benefit from Additive Manufacturing?
If you think that your own production line could benefit from Additive Manufacturing, but you’re not sure where to start, let us help you. Our 3DP Scan is an audit for Additive Manufacturing, held on your premises, by Materialise engineers. Our consultants will look for AM potential on the spot and provide you with a full report afterwards.