3D 프린팅의 최대 활용은 디자인에 대한 새로운 접근을 의미합니다. Materialise는 디자인 최적화는 지속적이며 중요한 프로세스라고 믿고 있습니다. 기존 방식의 제조 기술에서 3D 프린팅으로의 제작은 동일한 제한이 적용되지 않습니다. 진공 그리퍼와 같은 경우 기존 모델에서 3분의 1 비용으로 3D 프린팅하기까지 Materialise의 Design & Engineering 팀에 의해 수 차례의 발전을 필요로 하였습니다. 3D 프린팅 그리퍼의 무게는 4분의 1로 줄어들었으며 따로 조립이 필요하지 않았으며 그리퍼는알루미늄, 한가지 재질로 제작되었습니다.
절삭 그리고 기계가공으로부터…
사진과 같이 진공 그리퍼의 내부 공기 채널이 프론트 플레이트에 보이게 됩니다. Materialise의 엔지니어링 팀에게 그리퍼 프로젝트가 의뢰되었을 때 이미 파트는고객사에 의해 부분적으로 3D 프린팅을 위한 디자인 최적화가 된 상태였습니다. 알루미늄 재질의 3D 프린팅을 위한 디자인이었던 본래의 파트는 절삭 이후 기계 가공으로 제작되어 장시간의 노동 집약적인 과정을 겪어야 했으며 강판과 튜브, 연결 부분은 수작업으로 조립을 해야 했습니다.
문제점은? 디자인은 중장비 사용과 수작업으로 조립으로 인해 비용이 많이 듭니다. 엔지니어링 팀에게 주된 목표는 비용 절감으로 두 번째로는 그리퍼의 수명을 늘리는 것이었습니다. 사용자의 경험에서 부적절한 위치에 파트를 배치해 시간에 지남에 따라 계속해서 손상을 초래하였습니다.
메탈 3D 프린팅으로...
일반적으로 3D 프린팅에서 디자인 복잡성은 비용과는 상관이 없지만 재료 사용에 비용이 비례하므로 부피는 상관 관계가 있습니다. 그래서 Materialise 엔지니어들은 제일 먼저 재료가 아주 적게 필요한 필요 없는 부분을 뺀 그리퍼의 솔리드한 공간을 대체하고자 하였습니다. 수작업 조립을 줄이고자 팀은 그리퍼 디자인 내의 연결 튜브를 통합하였습니다. 통합된 튜브는 비용뿐만 절감이 아닌 누출의 위험까지 제거할 수 있었습니다.
하지만 파트는 더 가볍고 적은 비용으로 제작할 수 있었습니다. 부피를 제외한 금속 3D 프린팅에서 대표적인 비용의 원인은 서포트 구조입니다. 서포트가 생성되지 않은 파트의 부분은 3D 프린터 내에서 파트가 받는 고도의 온도 때문에 프린팅 도중 또는 이후 변형을 야기합니다. 여기서 서포트는 금속 재료를 사용 결과적으로는 비용을 증가시키는 요인이 됩니다. 그래서 잇따른 두 번의 디자인 변경 후 Materialise 엔지니어들은 깔때기 모양의 디자인을 고안하여 필요한 서포트 구조를 급격히 절감시키는 빌드 플랫폼 방향으로 프린팅할 수 있었습니다. 최종적으로 본래 디자인인 237g의 알루미늄 진공 그리퍼는 60g으로 줄어들었습니다.
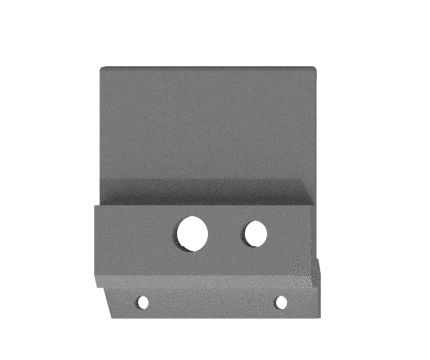
60g의 그리퍼 파트는 단일 빌드 디자인으로 결합된 연결 고리를 포함하여 수작업 조립을 필요로 하지 않게 되었습니다. 더 나아진 점은 사람이 초래할 수 있는 에러에 대한 가능성을 없애 파트의 정확한 포지션닝을 보장하여 그리퍼의 수명을 높일 수 있게 되었습니다.
“부피 절감과 통합된 기능성과 함께 조립이 필요 없이 70% 비용을 절감할 수 있었다. 사고력을 요하는 디자인과 엔지니어링으로 Materialise Engineering 팀은 고객에게 제조에 좀 더 고성능 및 빠른 진공 그리퍼를 굉장히 낮은 가격에 제공할 수 있었다.”
라고 Materialise의 Account Manager이Mathieu Cornelis라고 말했습니다.