Maksymalne wykorzystanie wytwarzania przyrostowego oznacza zastosowanie nowego podejścia do projektowania. W firmie Materialise wierzymy, że optymalizacja projektu jest ciągłym i kluczowym procesem. Ma ona szczególne znaczenie, gdy część przechodzi z tradycyjnej technologii produkcji na druk 3D, w którym takie same ograniczenia nie mają po prostu miejsca. W przypadku tego zacisku pneumatycznego nasz zespół ds. projektowania i usług inżynieryjnych przeprowadził projekt przez wiele etapów rozwoju aż do uzyskania części wyprodukowanej w technologii druku 3D, która kosztuje jedną trzecią ceny oryginału, waży jedną czwartą jego masy oraz nie wymaga montażu. A wszystko to przy użyciu tego samego materiału: aluminium.
Od frezowania i obróbki skrawaniem…
Na zdjęciu znajduje się zacisk pneumatyczny z wewnętrznymi kanałami powietrza widocznymi na płycie czołowej. Gdy projekt ten trafił na biurko zespołu inżynieryjnego Materialise, klient już częściowo zoptymalizował część pod kątem druku 3D. O ile oryginalna część została wyprodukowana poprzez frezowanie, a następnie obróbkę mechaniczną — czyli długi i pracochłonny proces — ten projekt był przeznaczony do druku 3D w aluminium. Stalowa płyta, rura oraz ramię łączące miały być następnie montowane ręcznie.
Na czym polegał problem? Projekt był kosztowny ze względu na duże zużycie materiału i konieczność ręcznego montażu. Głównym celem naszego zespołu inżynieryjnego była redukcja kosztów. Dodatkowym celem było wydłużenie żywotności zacisku, ponieważ z doświadczeń klientów wynikało, że nieprawidłowe ustawienie części powodowało z czasem stopniowe uszkodzenie.
…po druk 3D w metalu
Ogólnie rzecz biorąc, w wytwarzaniu przyrostowym złożoność konstrukcji nie ma wpływu na koszty. Taki wpływ ma za to objętość, z uwagi na wykorzystanie materiału. Dlatego inżynierowie z firmy Materialise najpierw skorzystali z możliwości zastąpienia litej części zacisku cieńszą wersją, wymagającą znacznie mniej materiału. Aby ograniczyć do minimum wymagany montaż ręczny, zespół zintegrował w konstrukcji zacisku rurę łączącą. Zintegrowane rury nie tylko zmniejszyły koszty, lecz także wyeliminowały ryzyko wycieku.
Jednak ta część mogłaby być jeszcze lżejsza i tańsza. Oprócz objętości kolejnym czynnikiem wpływającym na koszt druku 3D w metalu jest konstrukcja wsporcza. Wszelkie niepodparte, „wiszące” elementy mogą się potencjalnie odkształcić podczas lub po wydrukowaniu ze względu na wysokie temperatury, na które część jest narażona w drukarce 3D — jednak podpory zużywają cenny materiał i zwiększają koszty. W ramach kolejnych dwóch wersji projektu inżynierowie Materialise zdecydowali się na projekt w kształcie lejka oraz specjalną orientację na platformie roboczej, która znacząco zmniejszyła wymagane konstrukcje wsporcze: w efekcie powstał zacisk pneumatyczny z aluminium ważący zaledwie 60 gramów, w przeciwieństwie do ważącego 237 g oryginału.
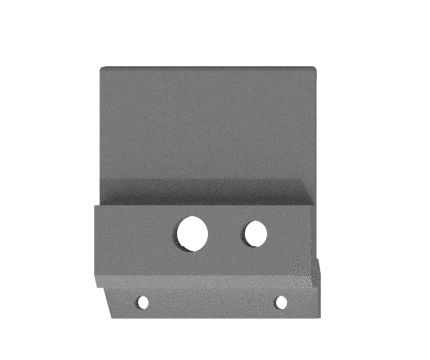
W dodatku te 60 g obejmuje nowe ramię łączące wbudowane w konstrukcję jednoczęściową, co eliminuje konieczność ręcznego montażu. Co więcej, zapewnia to prawidłowe ustawienie części, eliminując możliwość popełnienia błędu przez człowieka i przyczyniając się tym samym do wydłużenia żywotności zacisku.
„Dzięki zmniejszeniu objętości i zintegrowanej funkcjonalności udało nam się obniżyć koszty o 70% i wyeliminować konieczność montażu. Dzięki przemyślanej konstrukcji i inżynierii byliśmy w stanie zaoferować klientowi zacisk pneumatyczny o większej wydajności i prędkości produkcji, przy znacznie niższej cenie”.
Mathieu Cornelis, opiekun klienta, Materialise
Chcesz dowiedzieć się, w jaki sposób Twój projekt może skorzystać na wytwarzaniu przyrostowym?
Jeśli uważasz, że Twoja linia produkcyjna może skorzystać na wytwarzaniu przyrostowym, jednak nie wiesz, od czego zacząć, pozwól nam sobie pomóc. Nasze rozwiązanie 3DP Scan to audyt druku 3D przeprowadzany przez inżynierów z firmy Materialise w siedzibie klienta. Nasi konsultanci sprawdzą na miejscu potencjał wytwarzania przyrostowego, a następnie dostarczą pełny raport.