Volvo Car Gent i Materialise odkryły, że w przypadku zwiększenia wydajności oraz usprawnienia dostaw narzędzi i przyrządów można odblokować potencjał oszczędności, wydajności produkcji oraz innych aspektów. W jaki sposób? Korzystając z połączenia części drukowanych w technologii 3D oraz części dostępnych od ręki, aby szybciej tworzyć rozwiązania dostosowane do potrzeb. Przykładem jest przyrząd do klejenia, który łączy wszystkie poprzednie elementy w jednym uchwycie, waży o 64% mniej i może być dostarczony w ciągu zaledwie dwóch tygodni, kosztując zaledwie połowę ceny poprzedniego przyrządu.
Nowoczesne linie produkcyjne samochodów są szybkie, złożone i niezwykle dobrze zorganizowane. Opierają się one w dużej mierze na technologii i automatyzacji, ale także na niezliczonej liczbie narzędzi i sprzętu wykonanych specjalnie pod kątem konkretnej linii lub nawet poszczególnych modeli samochodów.
Te jedyne w swoim rodzaju, wykonane na miarę podzespoły rzadko są doceniane, gdy mowa o innowacjach linii produkcyjnych. Volvo Car Gent i Materialise zmieniły to podejście. Wspólnie odkryliśmy, że w przypadku zwiększenia wydajności oraz usprawnienia dostaw narzędzi i oprzyrządowania można odblokować potencjał oszczędności, wydajności produkcji oraz innych aspektów. W jaki sposób? Korzystając z połączenia części drukowanych w technologii 3D oraz części dostępnych od ręki, aby szybciej tworzyć rozwiązania dostosowane do potrzeb. Pierwszy przypadek: przyrząd do klejenia, który pomaga pracownikom umieszczać różne kombinacje logo Volvo, numeru modelu i innych informacji na bagażniku każdego nowego samochodu.
Nowy przyrząd do klejenia łączy wszystkie poprzednie elementy w jednym urządzeniu, waży o 64% mniej i może być dostarczony w ciągu zaledwie dwóch tygodni, kosztując zaledwie połowę ceny poprzedniego przyrządu.
Drukowanie linii produkcyjnych — zaczynamy od małych kroków
Niemal połowa rocznej produkcji samochodów Volvo (łącznie 533 000 sztuk w 2016 r.) opuszcza linię montażową Volvo Car Gent w Gandawie (Belgia). Zakład ten zajmuje się modelami XC60, S60 oraz V40, a także odpowiadającymi im modelami Cross Country, produkując około 57 samochodów na godzinę dla klientów z całego świata. Jest to szybkie, wymagające środowisko, które nie pozostawia miejsca na błędy.
Niewielkim, lecz kluczowym etapem montażu każdego egzemplarza Volvo jest znakowanie każdego pojazdu logo, numerem modelu oraz innymi oznaczeniami. Różnią się one w zależności od samochodu, jednak muszą być przymocowane dokładnie i spójnie, szybko oraz bez uszkodzenia lakieru bagażnika. Wcześniej czynność tę przeprowadzano przy użyciu licznych oddzielnych, niewygodnych przyrządów do klejenia — szablonów, które pracownicy podnosili do tylnej części pojazdu, a następnie nanosili odpowiednie znaki we właściwym miejscu, przy prawidłowym wyrównaniu.
Hannes Wauters, inżynier ds. sprzętu w Volvo Car Gent, stale poszukuje możliwości poprawy tego typu urządzeń i sprzętu produkcyjnego. Współpracując z Materialise, wraz ze swoim zespołem wskazał przyrządy do klejenia jako idealny przykład sprzętu do linii produkcyjnych drukowanego w technologii 3D.
Pan Hannes wyjaśnia: „W przypadku przyrządów produkcyjnych często potrzebujemy szybkiego rozwiązania, aby utrzymać pracę linii, dlatego wracamy do tradycyjnych metod produkcji — ponieważ je znamy. Zwykle nie mamy czasu na eksperymenty, jeśli jednak istnieje szansa, aby nauczyć się czegoś nowego, korzystamy z niej. Nowy przyrząd do klejenia był przeznaczony do modeli produkowanych w styczniu 2017 r., mieliśmy więc sporo czasu na opracowanie go. Mieliśmy już kilka części wydrukowanych w technologii 3D do starych przyrządów, była to więc doskonała szansa, aby wypróbować zalety metod wytwarzania przyrostowego, projektując część od początku”.
Koniec ze starymi rozwiązaniami: ciężkimi, łatwo ulegającymi uszkodzeniu i trudnymi w mocowaniu
Poprzednie przyrządy były spawane i dość ciężkie. Uchwyt był trudny w kalibracji i zapewniał tolerancję do ±2 mm. Przyrządy często się psuły w wyniku przypadkowego upuszczenia, a czas dostawy nowego uchwytu wynosił co najmniej 6 tygodni. Wymagania stawiane przed nowym przyrządem obejmowały dokładne ustawianie, powtarzalność oraz niepozostawianie śladów na lakierze. Ponadto część musiała być jednocześnie wytrzymała i lekka.
Pan Hannes kontynuuje: „Najważniejszą dla nas cechą była trwałość. Taki sprzęt jak przyrząd do klejenia musi być odporny na trudne i wymagające środowisko przemysłowe”.
Przejście na rozwiązanie modułowe: zaprojektowanie na nowo przyrządu do klejenia z zastosowaniem druku 3D
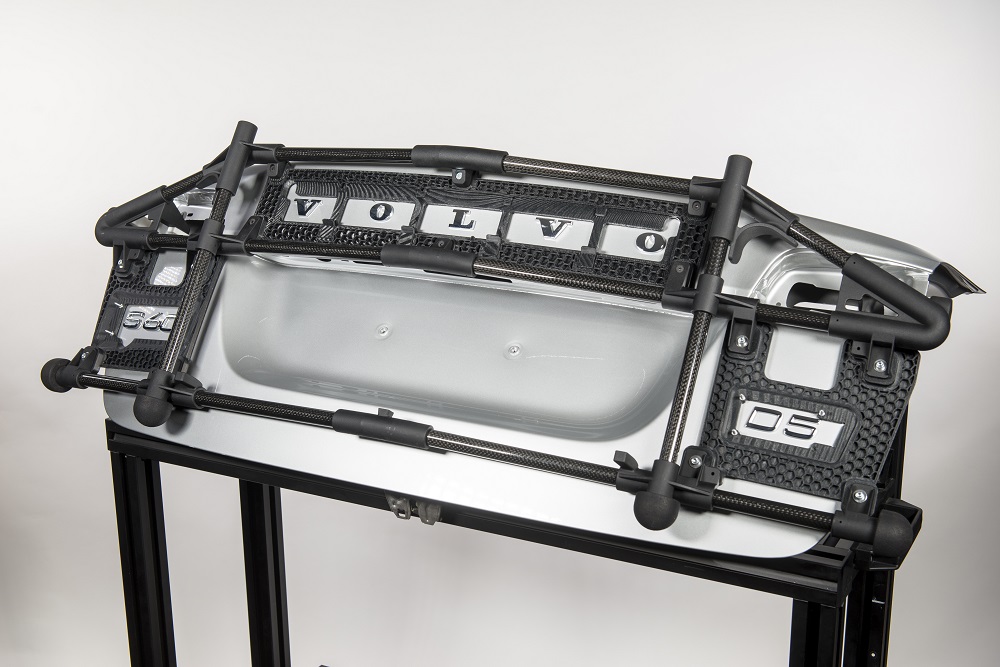
Mathieu Cornelis, menedżer ds. klienta w Materialise, wyjaśnia proces, jaki przeszła firma Materialise, aby opracować nowy projekt: „Podczas wstępnej oceny przyrządu do klejenia pod kątem potencjału druku 3D natychmiast stwierdziliśmy, że pomimo że jest to dość ciężki sprzęt, niekoniecznie musi być pojedynczą częścią drukowaną w technologii 3D. Zaczęliśmy więc szukać lekkiego, odpornego na wypaczenie i mniej wrażliwego na temperaturę materiału, dostępnego jako standardowy zapas — aby szybko uzyskać odpowiednią wielkość ramy bez zwiększania masy. Następnie mogliśmy zastosować wytwarzanie przyrostowe do wykonania mniejszych detali przyrządu”.
Zespół ds. projektowania i usług inżynieryjnych w Materialise wybrał standardową rurę z włókna węglowego pełniącą rolę podstawowej, bardzo lekkiej ramy, a następnie zaprojektował miejsca połączeń oraz podkładki miękkie i sprężyste wykonane w technologii druku 3D, aby je połączyć. Podejście modułowe oznaczało, że można było zastosować różnorodne materiały i technologie, aby wykorzystać ich specyficzne właściwości. Na przykład podkładki sprężyste zostały wydrukowane przy użyciu TPU (termoplastycznego poliuretanu) ze względu na właściwości podobne do gumy i bardzo dużą trwałość. Gwarantowało to odporność przyrządu na upadek.
Miejsca połączeń zostały wydrukowane z PA-12 (poliamidu), przeznaczonego specjalnie do złożonych, sprzężonych części. Specjalnie zaprojektowane kanały klejowe, które można było uzyskać wyłącznie przy użyciu druku 3D, między tymi miejscami połączeń a rurami z włókna węglowego, zapewniały dopasowanie mechaniczne, a także połączenie klejowe pomiędzy częściami.
Precyzyjne tolerancje i łatwa kalibracja — w jednym, eleganckim przyrządzie
Specjalny uchwyt do kalibracji zastąpił poprzedni, podatny na błędy proces kalibracji przyrządu na osobnym bagażniku samochodu, którego wymiary mogą zależeć od temperatury otoczenia. Dzięki łatwej kalibracji i znacznie dokładniejszej konstrukcji samego uchwytu nowy przyrząd do klejenia osiąga tolerancje poniżej 0,2 mm.
Wynikiem końcowym jest uchwyt kosztujący o 48% mniej, lżejszy o 64% i zapewniający szybki montaż. Łączy w sobie najlepsze cechy poszczególnych elementów, a także szablony do klejenia dla wszystkich możliwych kombinacji w pojedynczym przyrządzie. Konstrukcja modułowa sprawia, że jest łatwy w regulacji, kalibracji i naprawie.
Pan Hannes podsumowuje:„Precyzja nowego uchwytu naprawdę mnie zaskoczyła. Możemy teraz uzyskać znacznie dokładniejsze tolerancje i założyć mniejszy współczynnik odpadów/przeróbek. Nasi pracownicy na linii produkcyjnej go uwielbiają. Nowy przyrząd jest łatwiejszy w obsłudze i znacznie lżejszy. Pracownicy nie muszą się martwić, że go uszkodzą, a ergonomia znacznie wzrosła. Nie chcą już poprzedniego uchwytu!”
„Co najważniejsze, cały projekt był dla nas olbrzymią możliwością edukacyjną. Nauczył nas „myśleć przyrostowo” i zapewnił nowe kwalifikacje, które pozwolą stale usprawniać linię produkcyjną. I wreszcie, co może wydawać się niezbyt istotne, nowy uchwyt wygląda naprawdę fajnie i nowocześnie. Obserwując pracowników linii produkcyjnej, zatrzymuję się przy przyrządzie do klejenia, ponieważ wygląda tak dobrze. To niewielka rzecz, lecz sprawia, że jestem dumny ze swojej pracy”.