Niech stanie się światłość. To proste zdanie zaprzecza zawiłości rozwiązań produkcyjnych biorących udział w wytwarzaniu nowoczesnych rozwiązań oświetleniowych. Żarówki są wymagane w dużych ilościach, jednak ich podstawowa budowa wymusza precyzyjny montaż delikatnych materiałów. Dodając do tego trudne warunki powtarzalnego podgrzewania w piecu i gwałtownego chłodzenia, zużycie podczas ciągłej produkcji oraz nieustanną konieczność kontroli jakości, okazuje się, że za produkcją zwykłej żarówki kryje się znacznie więcej.
A co jeśli można uprościć ten proces? Co jeśli linia montażowa sama w sobie może być uosobieniem koncepcji „innowacyjnego myślenia” równoznacznej z produktem końcowym? Materialise oraz Philips Lighting postanowiły to sprawdzić, wykorzystując druk 3D. Współpraca zaowocowała „ponownym odkryciem” oprawki żarówki odpowiedzialnej wcześniej za uszkodzenie części oraz automatyzacją wymagających wcześniej dużych nakładów pracy serii przy użyciu lekkiej konstrukcji. Zaledwie te dwie innowacje zapewniły oszczędności kosztów rzędu 89 000 € rocznie dzięki korzyściom operacyjnym, które zapewniają.
Porozmawiajmy o Państwa projekcie.
Rozpoczęcie procesu wspólnej kreacji
Założona w 1891 roku w celu produkcji lamp żarowych oraz innych produktów elektrycznych, firma Philips wprowadza innowacje od ponad 125 lat. Zatrudniając 850 pracowników, zakład Philips Lighting w Turnhout (Belgia) odgrywa kluczową rolę w zachowaniu tej tradycji i jest powszechnie uznawany jako wyznaczający trendy lider w dziedzinie profesjonalnej technologii oświetleniowej. W rzeczywistości Philips Turnhout współpracuje z centrami badawczymi w Belgii oraz poza jej granicami nad innowacjami w dziedzinie wysokoprężnych gazowych lamp wyładowczych, od etapu pomysłu aż do produkcji.
Zainteresowany potencjałem, jaki może odblokować druk 3D – w szczególności druk w metalu – w ramach procesu produkcji, inżynier ds. projektowania fabryki Philips, Danny Van der Jonckheyd, oraz jego zespół zaprosili Materialise do zakładu, aby zyskać dogłębne zrozumienie specyficznych wymagań linii produkcyjnej Philips.
Sven Hermans, menedżer ds. rozwoju działalności w Materialise wspomina: „Należy zobaczyć linię w działaniu, aby prawdziwie docenić wymagania, napięcia i naprężenia danych elementów zespołu, a także zrozumieć presję wywieraną na personel. Będąc na terenie zakładu, przyglądaliśmy się częściom i rozmawialiśmy z operatorami linii produkcyjnych, zespołami ds. konserwacji, inżynierami fabryki – z jak największą liczbą osób, aby wskazać problemy i obszary wymagające usprawnień, które byłyby idealnie dopasowane do rozwiązań wykonanych w technologii druku 3D.
„Gdzie zastosowanie lżejszych materiałów miałoby największy wpływ? Gdzie wykonanie konstrukcji strukturalnej jest niemożliwe lub zbyt drogie przy użyciu tradycyjnych technik produkcji, aby poprawić jakość lub zmniejszyć straty? Nad tego typu zagadnieniami pracowaliśmy z zespołem z firmy Philips”.
Zmniejszenie kosztów – drukowanie w celu zapobiegania uszkodzeniom części
Pierwszą częścią wskazaną do poprawy był wspornik/uchwyt stosowany do utrzymywania lampy na miejscu i utrzymujący wbudowane przewody z dala od ciepła podczas stosowania palników spawalniczych do stopienia i uszczelnienia szklanych przewodów spalin. Powtarzalne narażenie na wysokie temperatury linii produkcyjnej w połączeniu z konstrukcją obejmującą spawane przewody z czteroelementowego zespołu wspornika oznaczały, że zużycie i uszkodzenia miały miejsce często, przy jednej lub dwóch awariach na tydzień.
Wspornik można było naprawić na terenie zakładu przy użyciu części zamiennych, które firma Philips musiała przechowywać na miejscu. Każdy wieloelementowy uchwyt był jednak trudny w usunięciu i demontażu – rozszerzające się w wyniku ciepła punkty przykręcania śrub były szczególnie problematycznym miejscem – a naprawa trwała do dwóch godzin. Tylko kilka usprawnień mogło zostać przeprowadzonych przed koniecznością zastosowania zupełnie nowej części, której dostawa wymagała do 8 tygodni.
Współpracując z Dannym Van der Jonckheydem i jego zespołem, Materialise zaprojektował i wydrukował w metalu nowy wspornik o jednoczęściowej konstrukcji, skracając czasochłonny montaż części i całkowicie usuwając problematyczne miejsca linii spawania. Podczas pierwszych trzech miesięcy korzystania, ponownie zaprojektowany wspornik nie popsuł się ani razu. To niewielka zmiana, która wprowadziła ogromną różnicę.
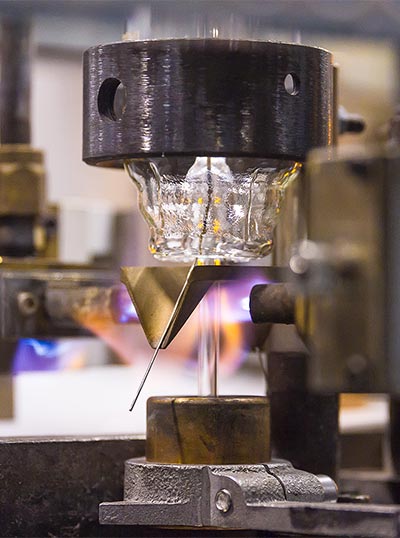
Nowy model chwytaka rozpoczyna pracę na lini produkcyjnej.
Danny wyjaśnia:
„Myśleliśmy, że rzadsza konieczność naprawy części i ułatwienie tego procesu będzie największą zaletą, jednak do tej pory nie musieliśmy wymienić żadnej. Jeśli będziemy to rozpatrywać wyłącznie pod kątem skrócenia czasu pracy techników ds. konserwacji, już teraz zaoszczędziliśmy około 9 000 €, a ponadto technicy mogą teraz skoncentrować się na faktycznych problemach technicznych”.
Ewolucja projektu elementu chwytaka (Od L – P początkowy element, Pierwszy projekt 3D, Finalny element w druku 3D)
„Mniejsza liczba usterek oznaczała, że zmniejszyliśmy również wydatki na części zamienne, a ze względu na to, że posiadamy obecnie „cyfrowe części zamienne”, które można wydrukować i dostarczyć w ciągu zaledwie 10 dni, musimy przechowywać tylko niewielką ich ilość w naszym zakładzie”.
„Poprzednie wsporniki wymagały także częstego czyszczenia, aby zapobiec powstawaniu rowków w wyniku tarcia – powodowanych przez przechodzące przewody – które mogłyby uszkodzić produkt końcowy. Musiały być usunięte z linii w celu utrzymania ich w ten sposób, co było bardzo czasochłonne. Druk 3D umożliwił stworzenie nowych stożkowych uchwytów na przewody, będących częścią wspornika, z wewnętrznymi kanałami, które wymagały mniej czyszczenia i zapewniały konserwację na miejscu”.
„Jednak największą różnicą był wpływ na nastawienie osób pracujących w naszym zakładzie. Wzbudził u wszystkich przekonanie, że możemy i powinniśmy inaczej wykonywać pewne rzeczy – podczas pierwotnego projektu miałem kontakt z ludźmi z różnych etapów produkcji, posiadającymi pomysły na inne sposoby, w jakich druk 3D może nam pomóc. Projekt ten prawdziwie zaangażował naszych pracowników”.
Odkrycie zacisku – mniej pracy, mniejsza waga, prostszy cykl
Dzięki temu nowemu nastawieniu podczas ponownego opracowania wspornika do lamp, zespół produkcyjny Philips zauważył kolejną szansę. Czy druk 3D może pomóc w automatyzacji obecnych, pracochłonnych procesów? Odpowiedź brzmi tak.
Linia wymagała wcześniej operatora maszyny – obecnego ciągle – do fizycznego umieszczania części w 12-otworowym zacisku, stosującego materiały i wyjmującego gotowe elementy. Automatyzacja tego procesu wymagała usprawnień możliwości zasysania próżniowego zacisku oraz lżejszej konstrukcji, wystarczająco wytrzymałej, aby stawić czoła naprężeniom i napięciom operacji automatycznej podczas podnoszenia i odkładania.
Danny wraz z zespołem przekonał się, że druk 3D otwiera olbrzymi potencjał pod kątem alternatywnych materiałów metalowych, tekstur i powierzchni wewnętrznych, które mogłyby zapewnić rozwiązanie. Zaczął więc pracować z Materialise, aby zaprojektować i wydrukować część, która zda ten test. Dzięki konsolidacji konstrukcji (zmniejszenie konieczności stosowania wielu pojedynczych części), stworzeniu zakrzywionych kanałów wewnętrznych (wyjątkowej zalety druku 3D) oraz wydrukowi zacisku z aluminium (AlSi10Mg), zwiększono ssanie, przy zmniejszeniu ogólnej masy podzespołu – co zapewniło szybszy, bardziej niezawodny ruch.
„Nowe możliwości zacisku usunęły konieczność ręcznego umieszczania części, co na przestrzeni roku zapewni oszczędności rzędu 80 000 € oraz znaczną liczbę godzin pracy operatora. Przede wszystkim prędkość uzyskana dzięki zmniejszeniu masy oznacza, że czas trwania cyklu również się skrócił, przy zwiększeniu produkcji – co stanowi optymalne równanie. Cały proces otworzył nasze oczy, uwolnił wyobraźnię i zapewnił sympatię wobec druku 3D w takim zakresie, że stał się, moim zdaniem, naturalnym elementem zestawu narzędzi produkcyjnych”.
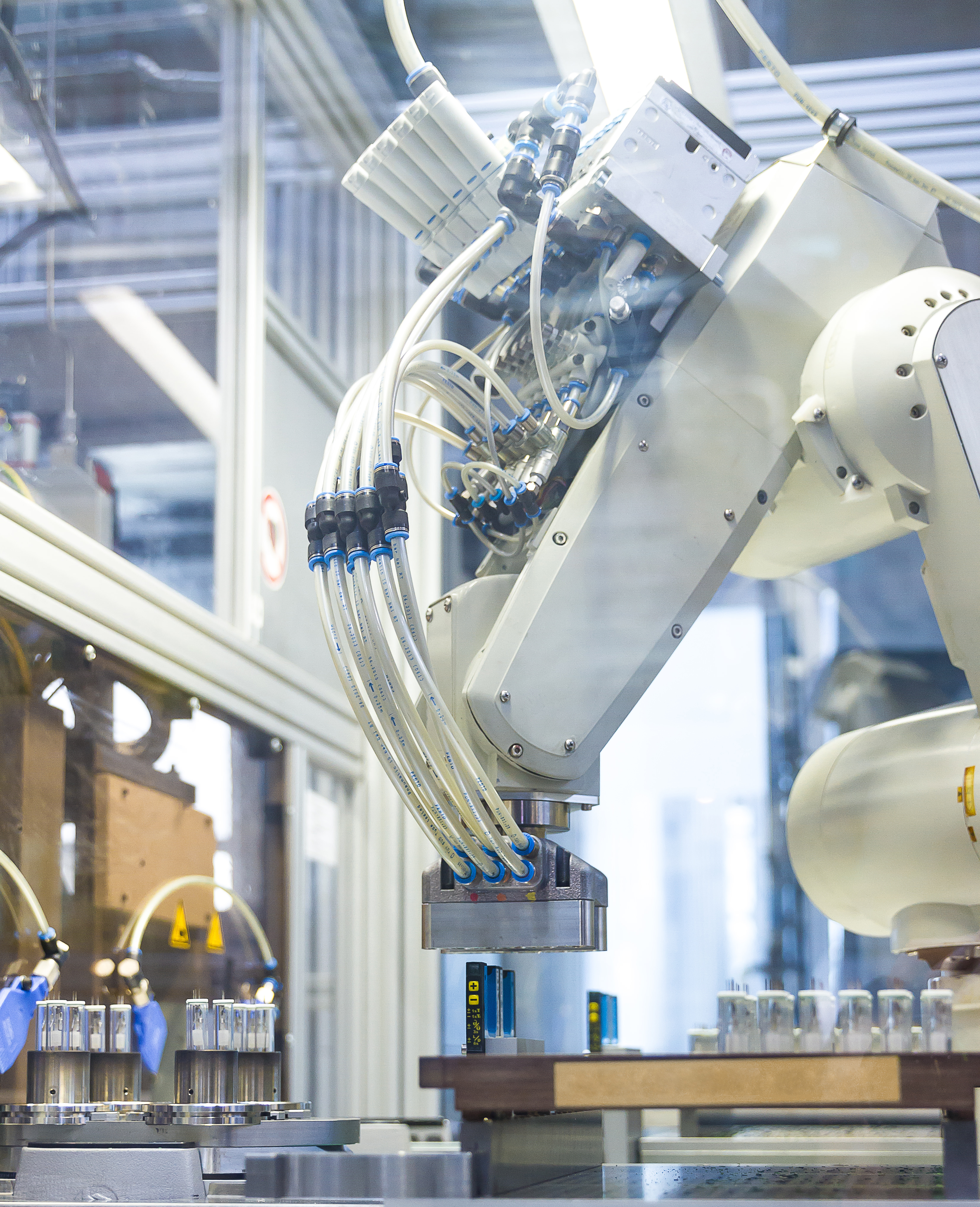
Gripper ssący wydrukowany w technologii 3D – zainstalowany na lini produkcyjnej