Quando si progetta o si realizza un componente per un veicolo aerospaziale, la sfida più complessa è rappresentata dall’ottimizzazione del peso. Inoltre, questo fattore non può essere privilegiato a scapito della robustezza o delle prestazioni del componente. Materialise Manufacturingha lavorato insieme alla divisione progettazione di Atos, azienda leader a livello mondiale nei servizi digitali, al fine di reinventare un inserto in titanio ampiamente utilizzato nel settore aerospaziale per trasferire elevati carichi meccanici in determinate strutture, come ad esempio i satelliti. Grazie a un design ottimizzato in modo intelligente e prodotto mediante tecnologie di stampa 3D in metallo, i nuovi inserti in titanio hanno un terzo del peso iniziale; alcune delle loro proprietà sono inoltre state ottimizzate.
Inserti con strutture sandwich
Questi inserti vengono in genere utilizzati come punti di montaggio per fissare i dispositivi ai satelliti. Sono inserti che spesso sostengono carichi elevati e devono sollevare strutture pesanti e di grandi dimensioni. Ciò significa che devono presentare un elevato rapporto resistenza/peso: si tratta di componenti che hanno bisogno di avere un’elevata resistenza specifica e rigidità ma un peso minimo. Gli inserti vengono co-vulcanizzati con i pannelli sandwich a struttura composita tipicamente impiegati nelle strutture aerospaziali. Gli inserti trasferiscono il carico al pannello attraverso un adesivo.
Gli inserti classici sono in genere realizzati in alluminio o in titanio, con una forma a mattoncino, in quanto vengono fabbricati a macchina. Il riempimento è compatto e questo li rende pesanti e costosi. Oltre ai costi dei materiali, i componenti pesanti contribuiscono inoltre ad aumentare i costi operativi per i veicoli aerospaziali ad ogni lancio.
La stampa 3D in metallo può tuttavia risolvere questi problemi, senza rinunciare all’uso degli stessi materiali: alluminio e titanio.
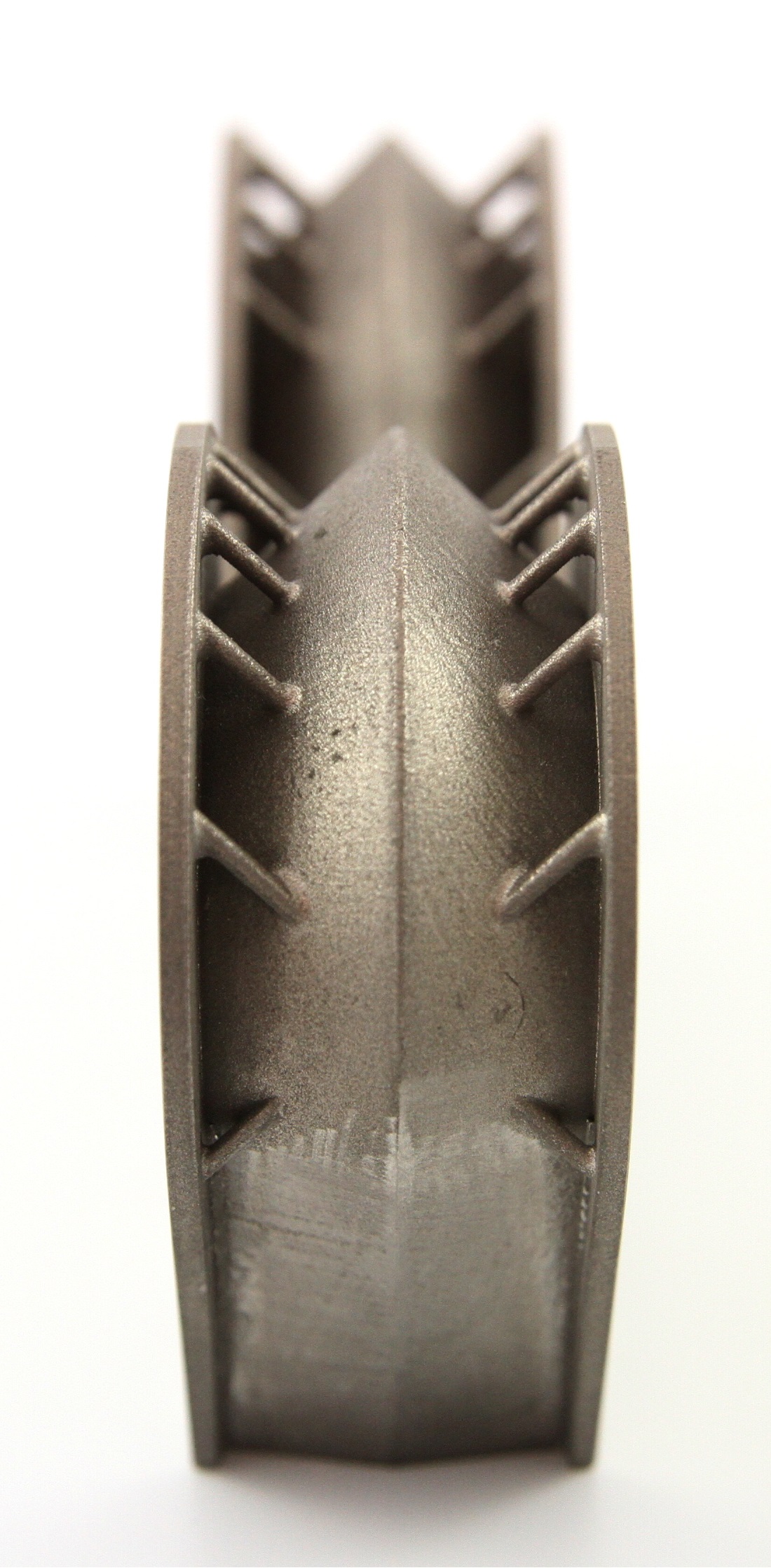
Ottimizzazione del design mediante la produzione additiva
Per i progettisti, la sfida consisteva nel migliorare dei concetti estremamente tradizionali. Il progetto è stato affrontato in modo da prendere in considerazione tutti i requisiti spaziali, dalla fase di ideazione alla produzione. Le competenze di Atos nel campo dell’ingegneria aerospaziale e della simulazione strutturale si sono rivelate utili nella progettazione di questo nuovo componente, sia per le sue parti esterne sia all’interno, migliorandone le prestazioni complessive.
Con la produzione additiva, lo spazio interno degli oggetti può essere scavato o progettato utilizzando strutture leggere, che impiegano materiale solo dove necessario. I progettisti Materialise e Atos si sono concentrati prima di tutto sulla riduzione del materiale utilizzato all’interno della parte. Adottando le tecniche avanzate dell’ottimizzazione topologica e della progettazione a reticolo, il team ha ridotto il peso dell’inserto da 1.454 a 500 grammi.
Oltre alla riduzione del peso, il team ha risolto i problemi riscontrati nel design originario riguardo alle sollecitazioni termoelastiche. Questi inserti vengono installati nel corso del processo di vulcanizzazione dei polimeri rinforzati con fibra di carbonio e sono perciò soggetti a sollecitazioni termoelastiche. Il design ottimizzato ha permesso di ridurre la vulnerabilità a tali sollecitazioni e di migliorare la distribuzione del carico, determinando una maggiore durata operativa degli inserti.
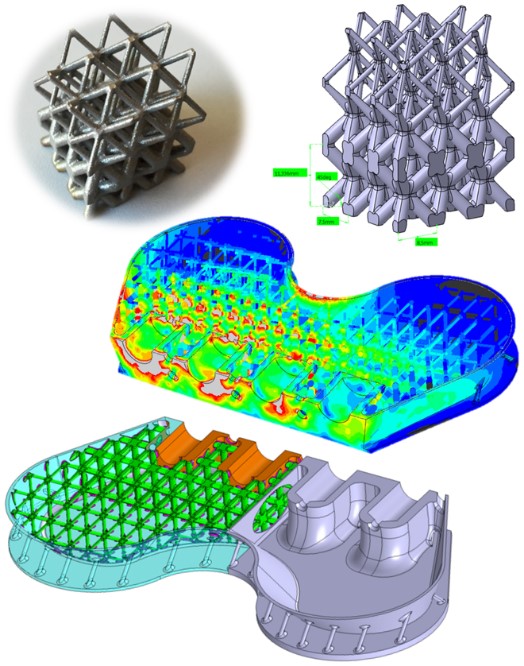
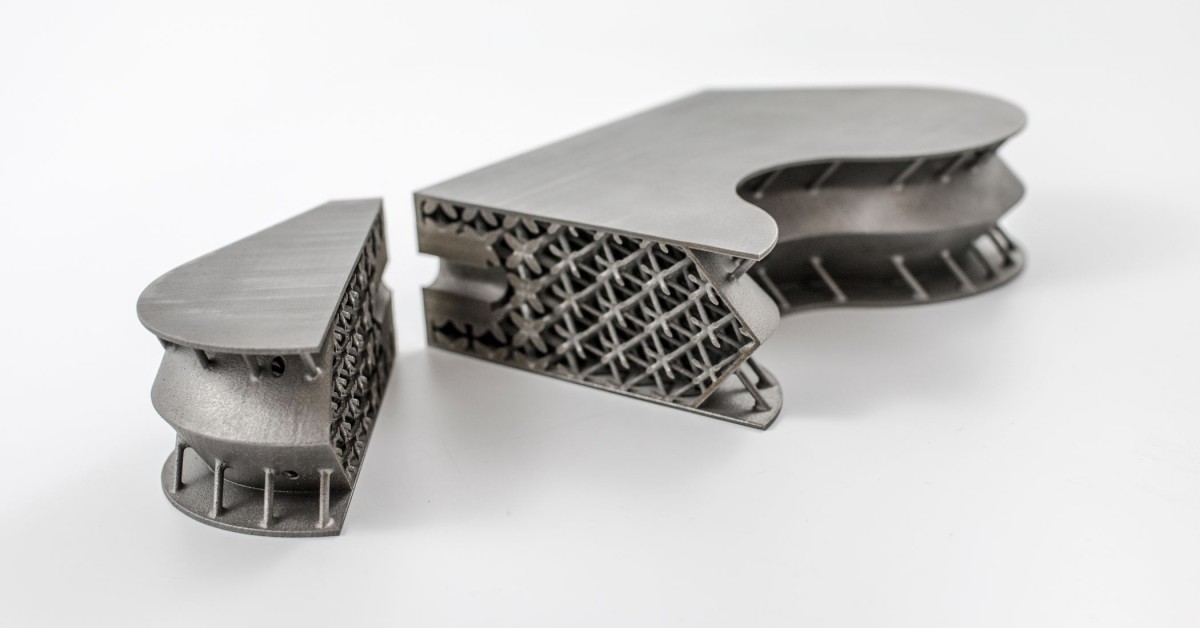
La sezione trasversale dell’inserto in titanio mostra le strutture interne alleggerite.
Utilizzando il nuovo design, sono stati realizzati due inserti in titanio (TiAl6V4), nello stabilimento Materialise per la stampa 3D in metallo di Brema. Come centro di eccellenza Materialise per la stampa 3D in metallo, specializzato sia nella produzione sia nello sviluppo software, questo stabilimento ha dimostrato, attraverso progetti come questo, la sua portata nel campo della produzione avanzata. Anche la stampa 3D in metallo ha già dimostrato il suo incredibile potenziale nel settore aerospaziale, poiché elimina la necessità di strumenti preliminari alla realizzazione ed è pertanto una tecnologia in grado di rispondere con tempi di consegna estremamente rapidi.
“La riduzione del peso permetterà di aumentare il numero di apparati utili che potranno essere impiegati nei satelliti e determinerà una considerevole riduzione dei costi ad ogni lancio. Siamo orgogliosi di questa innovazione. Creando in tempi così brevi questo prodotto complesso mediante la produzione additiva, Atos e Materialise si posizionano tra i principali fornitori di soluzioni per la stampa 3D in metallo.”
Marta García-Cosío, Mechanical Engineering Director, Atos Spagna
Grazie a questo riuscitissimo progetto e alla ricerca che ne è alla base, ci auguriamo che nel settore aerospaziale e aeronautico vengano implementati sempre più spesso componenti in metallo realizzati con tecnologie di produzione additiva.
Che cosa significa una riduzione di peso del 66% per quanto concerne il controllo dei costi nel vostro settore?
Quando si producono parti complesse eliminando meccanicamente il materiale a partire da un blocco, la maggior parte del metallo pagato finisce scartato. C’è un costoso squilibrio tra il peso del metallo acquistato e il metallo che costituisce il componente finale che “andrà in volo”. Questo è quello che chiamiamo “buy-to-fly ratio”. Leggi il whitepaper gratuito “La “buy-to-fly ratio”: come tagliare i costi con la stampa 3D in metallo” e scopri in che modo la stampa 3D in metallo può essere utile nella produzione di parti complesse.
