A la hora de diseñar o crear un componente para un equipo aeroespacial, el reto más importante es la optimización del peso. Un objetivo que no suele conseguirse mediante la reducción de la resistencia o del rendimiento de los componentes. Materialise Manufacturing trabajó mano a mano con la división de ingeniería de Atos, una empresa líder a nivel global en el sector de los servicios digitales, con el fin de rediseñar los insertos de titanio que se utilizan en el sector aeroespacial para la transferencia de cargas mecánicas elevadas en estructuras como satélites. Gracias a un diseño optimizado de forma inteligente que se ha creado mediante impresión 3D en metal, el peso de los nuevos insertos de titanio es de apenas un tercio del peso inicial, además de contar con nuevas y mejores propiedades.
Insertos en estructuras de sándwich
Estos insertos suelen utilizarse en los puntos de montaje, con el fin de fijar dispositivos a los satélites. Este tipo de insertos suelen soportar cargas elevadas y sujetan estructuras pesadas de gran tamaño. Por ese motivo, tienen que contar con una relación entre resistencia y peso alta: son piezas que cuentan con una rigidez y resistencia específica elevadas, así como con un peso mínimo. Los insertos se curan de forma conjunta con los paneles en forma de sándwich de estructura compuesta que suelen utilizarse en las estructuras aeroespaciales. El inserto transfiere la carga al panel a través de un adhesivo.
Los insertos clásicos suelen construirse en aluminio o titanio, con forma de ladrillo, ya que normalmente se fabrican para su mecanizado. Son completamente macizos, por lo que su coste, y sobre todo su peso son elevados. Además del coste financiero, el alto peso incrementa los costes operativos de los vectores de lanzamiento.
Con la impresión 3D en metal, estos problemas pueden resolverse, al mismo tiempo que permite seguir utilizando los mismos materiales: aluminio y titanio.
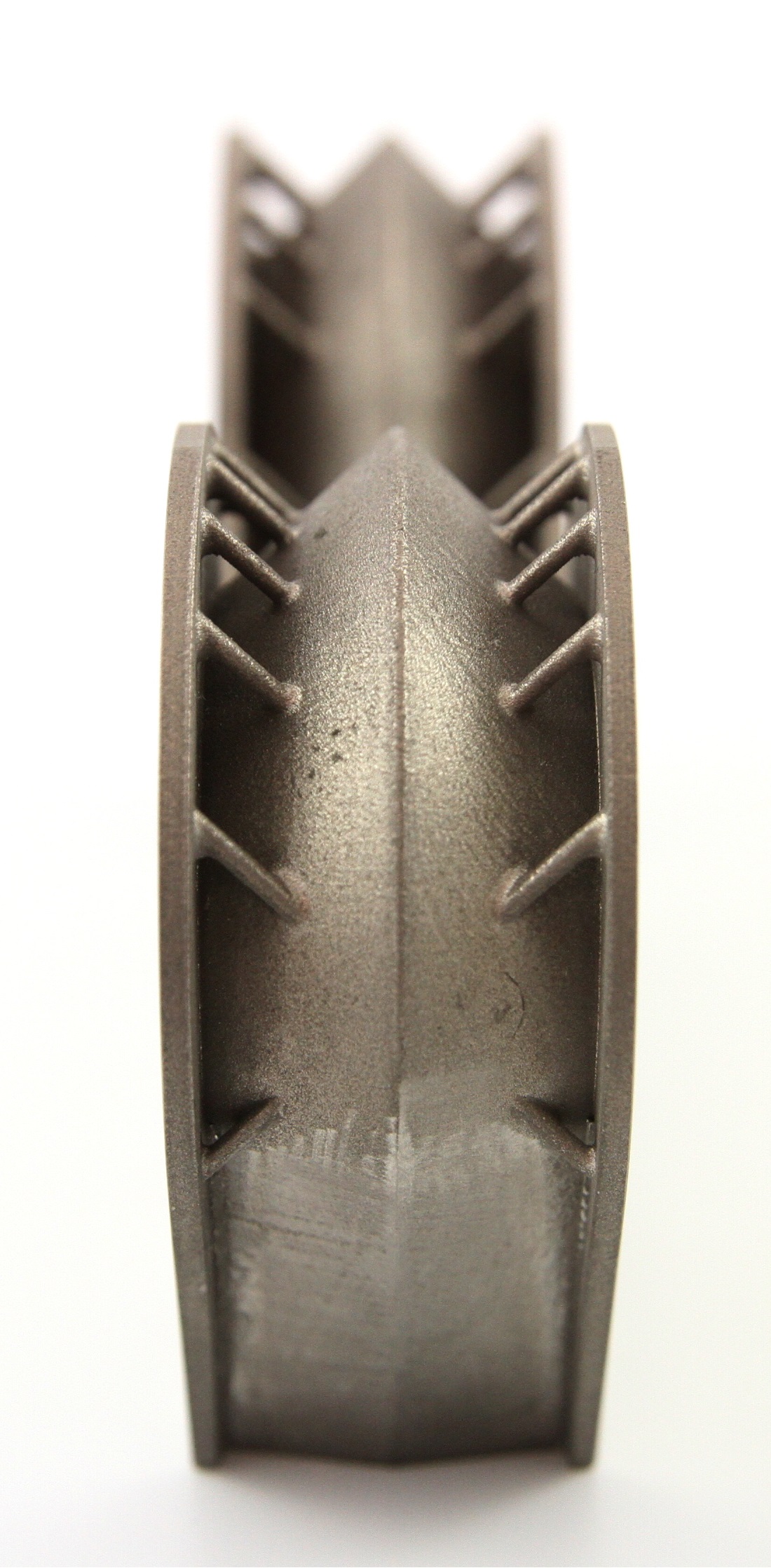
Optimización del diseño gracias a la fabricación aditiva
Los ingenieros se enfrentaron al reto de mejorar considerablemente una serie de conceptos tradicionales. El diseño se elaboró para cubrir todos los requisitos del ámbito espacial, desde la fase de concepción hasta la de fabricación. La experiencia de Atos en el ámbito de la ingeniería aeroespacial y de simulación estructural resultó muy útil para diseñar tanto el interior como el exterior de este nuevo componente, lo que permitió mejorar su rendimiento general.
Gracias a la fabricación aditiva, el espacio interior de los objetos puede ahuecarse o diseñarse con estructuras ligeras, lo que permite utilizar material solo donde es necesario. Los ingenieros datos y Materialise comenzaron a trabajar en la reducción del uso de material en el interior de la pieza. Mediante el uso de técnicas avanzadas de optimización de topologías y diseño de estructuras de entramado, el equipo consiguió reducir la masa del inserto de 1.454 a 500 gramos.
Además de la reducción de peso, el equipo también resolvió varios problemas de tensión termoelástica que presentaba el diseño original. Debido a que estos insertos se instalan durante el proceso de curado de polímeros reforzados con fibra de carbono, están sujetos a tensiones termoelásticas. El diseño optimizado ha permitido reducir las vulnerabilidades generadas por estas tensiones y mejorar la distribución de la carga, lo que ha contribuido a incrementar la vida útil de los insertos.
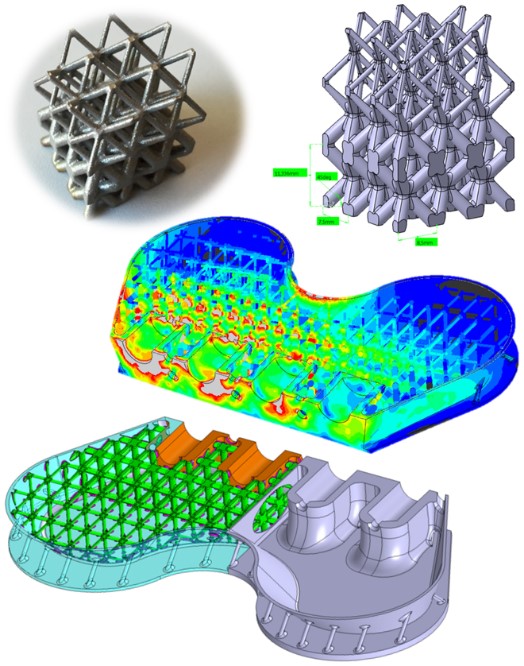
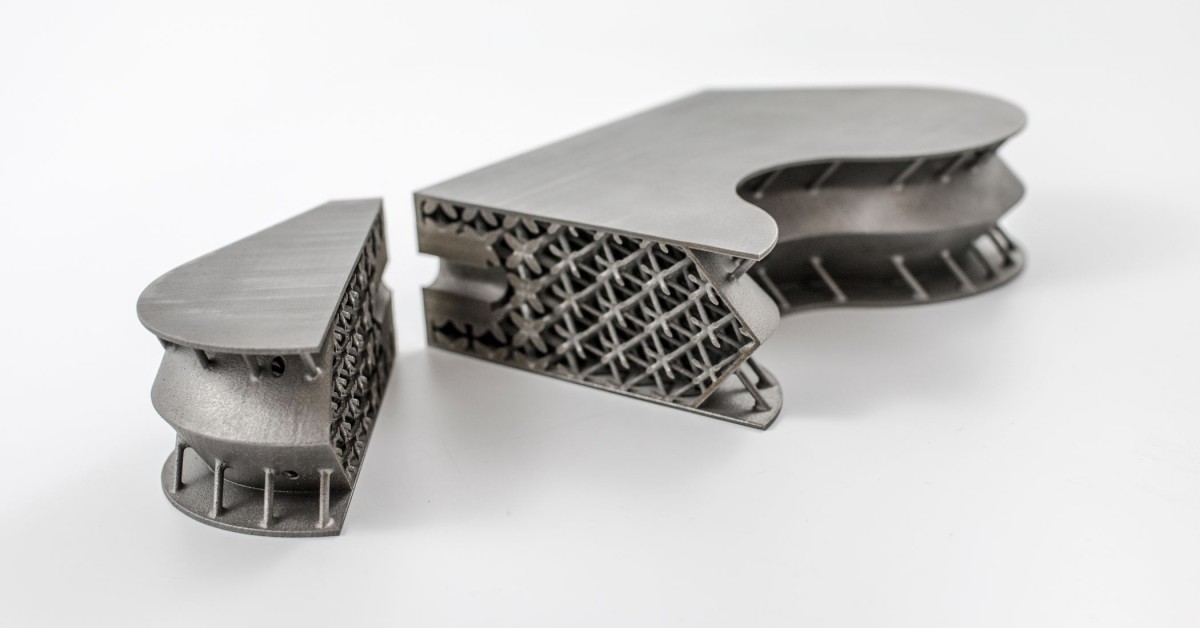
La sección transversal del inserto de titanio muestra las estructuras ligeras en su interior
Empleando este nuevo diseño, se fabricaron dos insertos de titanio (TiAl6V4) en las instalaciones de impresión 3D en metal de Materialise en Bremen. Como centro de referencia de Materialise en el campo de la impresión 3D en metal, tanto en tareas de producción como de desarrollo de software, estas instalaciones han demostrado sus capacidades en materia de fabricación avanzada mediante proyectos como este. Asimismo, la impresión 3D en metal también ha demostrado el increíble potencial de sus aplicaciones en el sector aeroespacial, ya que, debido a la ausencia de herramientas previas, esta tecnología permite ofrecer unos increíbles tiempos de entrega.
“La reducción de peso va a permitir el incremento de la carga útil en los satélites y lograr un considerable ahorro en cada lanzamiento. Estamos muy orgullosos de esta innovación. Al desarrollar este complejo producto en el campo de la fabricación aditiva en un periodo de tiempo tan breve, Atos y Materialise han conseguido situarse en una posición líder dentro de los proveedores de soluciones de impresión 3D en metal.”
Elvira Leon, directora de ingeniería mecánica de Atos Spain
Gracias a este proyecto y a todas las iniciativas de investigación que ha requerido, tenemos como objetivo incrementar la implementación de componentes de metal desarrollados mediante fabricación aditiva para el sector aeroespacial y aeronáutico.
¿Que supondría una reducción media de la masa del 66 % en lo relativo al control de costes en su sector?
Si fresa material en un bloque para obtener piezas complejas, gran parte del metal por el que paga se convierte en basura. Existe una costosa diferencia entre el peso del metal que ha adquirido y el del metal que forma parte del componente final. A esto es a lo que denominamos “Buy-to-Fly Ratio”. Lea el documento técnico gratuito “Buy-to-fly Ratio: - La clave para reducir costes en la impresión 3D en metal” y descubra cómo la impresión 3D en metal puede ayudarle en la producción de piezas complejas.
