Per gli appassionati delle due ruote, andare in bicicletta significa scalare ripide colline, correre su lunghe distanze e combattere venti incessanti. Il peso della bicicletta fa la differenza. La nuova bici da corsa di Pinarello, Dogma F, è il modello leggero che i ciclisti hanno sempre sognato.
Per creare questa bicicletta unica nel suo genere, avevano bisogno dell'aiuto di partner innovativi e delle tecnologie più all'avanguardia. I servizi completi di stampa 3D in metallo di Materialise e i flussi di lavoro su misura sono stati un importante fattore abilitante: arrivare quasi a dimezzare il peso di un componente essenziale della sella.
La sfida
Riduzione del peso dei morsetti reggisella rispettando i tempi, il budget e gli obiettivi di produzione della Pinarello
La soluzione
Stampa 3D in metallo con flusso di lavoro personalizzato presso il Materialise Metal Competence Center
Il risultato
Componenti più leggeri del 42,5% stampabili su larga scala con successo
La sfida
Nel settore del ciclismo, ogni grammo di peso fa la differenza. Ecco perché per l'ultimo prodotto Pinarello, hanno puntato su una bici da corsa che pesasse molto meno di quelle della concorrenza. Raggiungere questo obiettivo, però, significava molto più della semplice riduzione del peso, ovviamente. Il team avrebbe dovuto bilanciare questo con i costi, la qualità, la velocità di produzione e il numero di unità prodotte.
“La sfida per il dipartimento R&S di Pinarello è stata veramente quella di concentrarsi sulla riduzione del peso”, spiega Maurizio Bellin, Chief of Operations Pinarello. “Quando i ciclisti sono in salita e percorrono molti chilometri controvento, più la bici è leggera, più vanno veloce. Per questo abbiamo puntato al minimo peso possibile”.
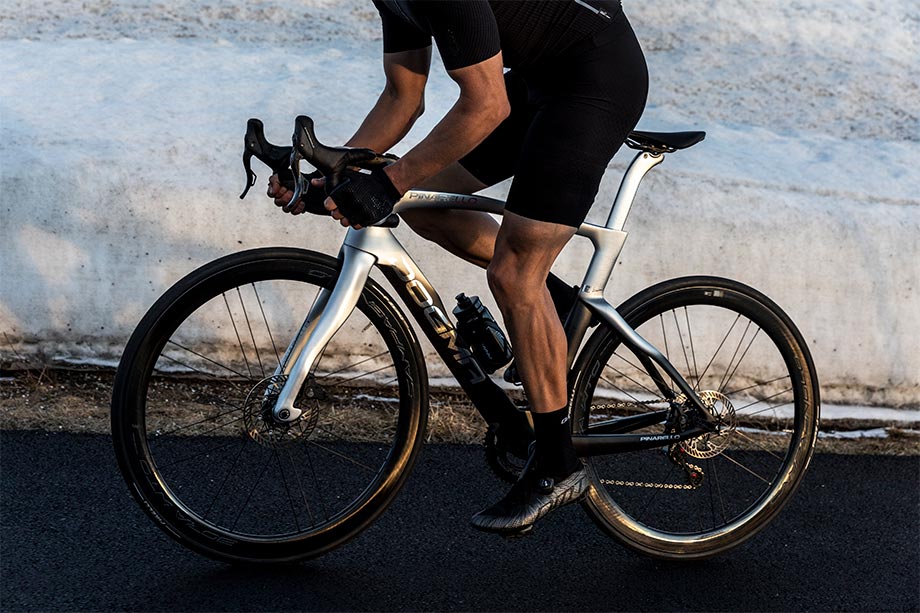
Uno dei principali obiettivi di progettazione di Pinarello per questa nuova bici era la riduzione del peso
Pinarello ha avviato il progetto collaborando con vari fornitori esperti in tecnologie che prometterssero risultati prestazionali ma leggeri. Avevano un progetto originale per i loro morsetti reggisella che utilizzava metodi di produzione tradizionali, ma, per ottenere i risultati di peso che desideravano, si sono rivolti a Materialise e alla stampa 3D.
La soluzione
Il team Materialise, grazie alla libertà di progettazione della stampa 3D in metallo, sapeva di essere in grado di creare un morsetto reggisella molto più leggero. La sfida in questo caso consisteva nel produrre i componenti su larga scala in poche settimane. I team interni di progettazione e ingegneria, software e produzione di Materialise hanno poi dovuto unirsi per raggiungere gli obiettivi di produzione.
"Nel nostro Metal Competence Center a Brema, in Germania, disponiamo di tutte le competenze di cui abbiamo bisogno sotto lo stesso tetto", spiega Philip Buchholz, Technical Project Manager di Materialise. "In queste nuove strutture, uniamo le nostre capacità di progettazione interne, la vasta conoscenza del nostro dipartimento R&S e i nostri processi di produzione industrializzati".
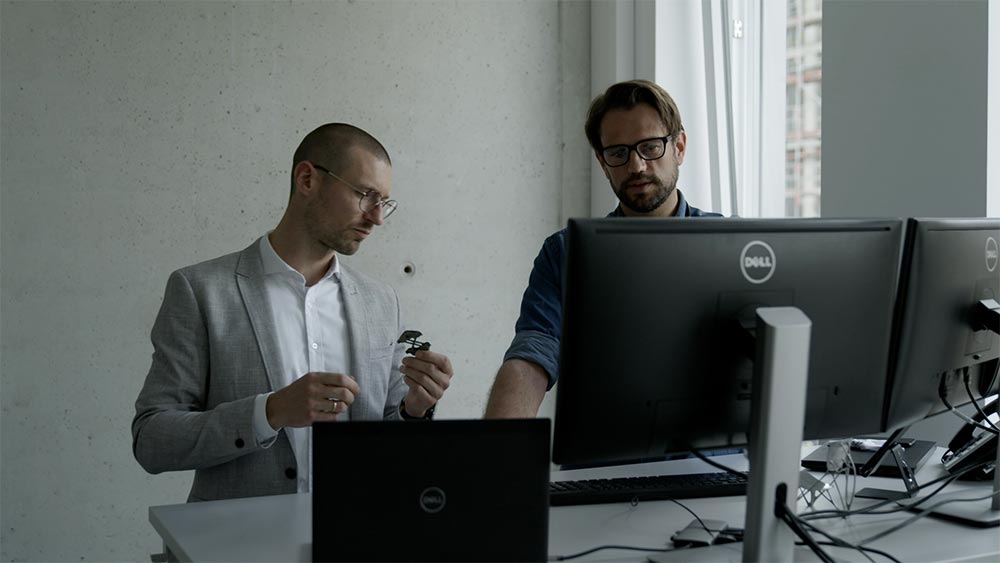
Nel nostro Metal Competence Center, possiamo combinare le conoscenze di
esperti di software, design e ingegneria per portare la stampa 3D in metallo al livello più alto
"Progetto e ingegnerizzazione sono stati realizzati in stretta collaborazione con Pinarello", afferma Tim Hermanski, Design Engineer presso Materialise. “Con ogni iterazione del progetto, abbiamo per prima cosa completato i test di simulazione virtuale. Il morsetto reggisella doveva essere leggero, ma la sua funzione richiede una forza sufficiente per sostenere il peso del ciclista. Questi test interni hanno permesso di risparmiare molto tempo garantendo stampabilità e affidabilità del componente finale”. Una volta completati i test, il team ha condiviso i progetti stampati in 3D con Pinarello per condurre la propria serie di test fisici, come le prove di fatica su un banco di prova e su strada.
Uno dei principali vantaggi della stampa 3D, in questo caso, è stato la velocità con cui si finalizza il progetto. Mentre la produzione convenzionale richiede nuovi stampi e una complessa programmazione CNC ad ogni aggiornamento del progetto, qui non è così: i design sono completamente digitali e possono quindi essere adattati rapidamente.
Oltre alla progettazione effettiva del componente, i team avrebbero dovuto affrontare la sfida di produrre così tanti componenti in così poco tempo. Il progetto richiedeva la stampa di 2.000 singoli componenti in meno di un mese, ogni mese. È stato allora che la collaborazione interna di Materialise ha dimostrato ancora una volta il suo valore. Il team ha unito le forze per creare un flusso di lavoro di produzione personalizzato e completo, inclusi l'etichettatura e il controllo qualità, ed è riuscito a raggiungere l'obiettivo.
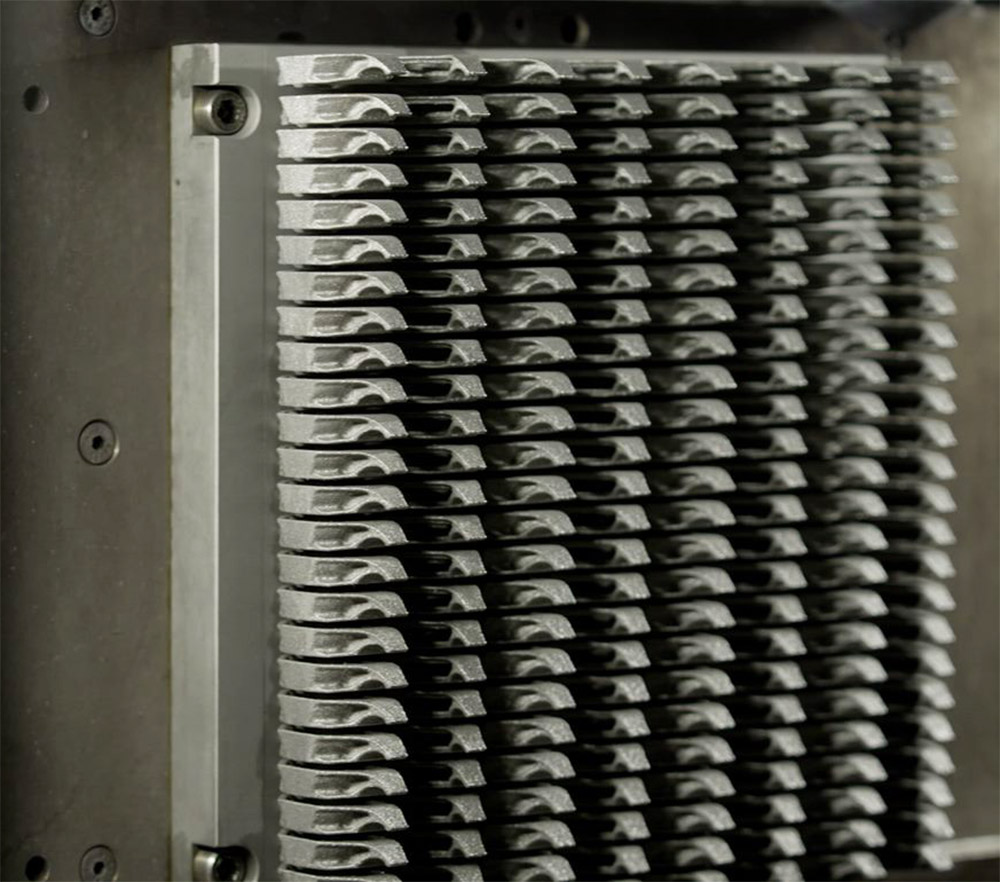
Grazie a un flusso di lavoro di produzione personalizzato,
il nostro team ha stampato 2.000 componenti in meno di un mese
"Abbiamo dovuto introdurre l'industrializzazione all'interno della nostra catena produttiva", afferma Philip. “Lo abbiamo fatto progettando un componente e una procedura che non necessitassero di strutture di supporto o passaggi di post-elaborazione manuale. L'eliminazione di questi passaggi ci ha consentito di risparmiare molto tempo durante la produzione. Abbiamo anche creato un set di parametri di stampa personalizzato che ha accelerato i tempi di stampa, si è adattato alle proprietà del materiale richiesto e ha reso il progetto fattibile, ottimizzando i costi.
“Abbiamo ottenuto tutto questo con Materialise Process Tuner, una soluzione che presenteremo sul mercato entro la fine dell'anno che "sintonizza" ampiamente lo sviluppo dei processi. Questo software, non solo accelera la configurazione dei parametri, ma riduce anche gli errori grazie all'automazione e fornisce approfondimenti e statistiche intelligenti, il tutto archiviato in un database centralizzato per operazioni future. Abbiamo sviluppato parametri di stampa ottimizzati in poche settimane, anziché in mesi. Non avremmo potuto raggiungere questo obiettivo senza il know-how combinato dei nostri team di software e D&E presso il Metal Competence Center".
Il risultato
Grazie alla stretta collaborazione con Pinarello e ai notevoli sforzi compiuti all'interno del team interno, Materialise ha fornito un componente che ha permesso a Pinarello di raggiungere il suo obiettivo.
Gli esperti di stampa 3D hanno progettato il morsetto reggisella in modo da sfruttare la libertà di progettazione della produzione additiva e hanno scelto il materiale giusto per ottenere una significativa riduzione del peso. Alla fine, il componente in titanio, stampato tramite fusione laser selettiva, è risultato più leggero del 42,5% rispetto al design originale in alluminio, realizzato mediante un processo di produzione tradizionale.
Con l'accessibilità della stampa 3D, possiamo offrire questa tecnologia a molti altri e non solo ai migliori ciclisti che gareggiano al Tour de France. Possiamo offrirla a chiunque nel mondo”.
— Maurizio Bellin, Chief of Operations, Pinarello
Anche la velocità con cui Materialise ha prodotto componenti stampati in 3D su questa scala è stata un'impresa impressionante. Ottimizzando la progettazione e snellendo i processi produttivi, il team ha fronteggiato per ogni ordine la consegna di 2.000 componenti in tre settimane, fino a 20.000 componenti. Per fare un esempio di una tale velocità, la produzione tradizionale richiede che ordini di queste dimensioni vengano effettuati da sei a dodici mesi in anticipo, soprattutto in tempi come questi in cui le catene di approvvigionamento sono influenzate da carenza di materie prime a livello globale e di capacità produttiva. Anche in questo caso il fatto di essere situati in Europa ha rappresentato un vantaggio significativo. Materialise ha garantito tempi di consegna più rapidi e consegne più sostenibili rispetto a un eventuale ordine effettuato a un produttore sito ovunque nel mondo.
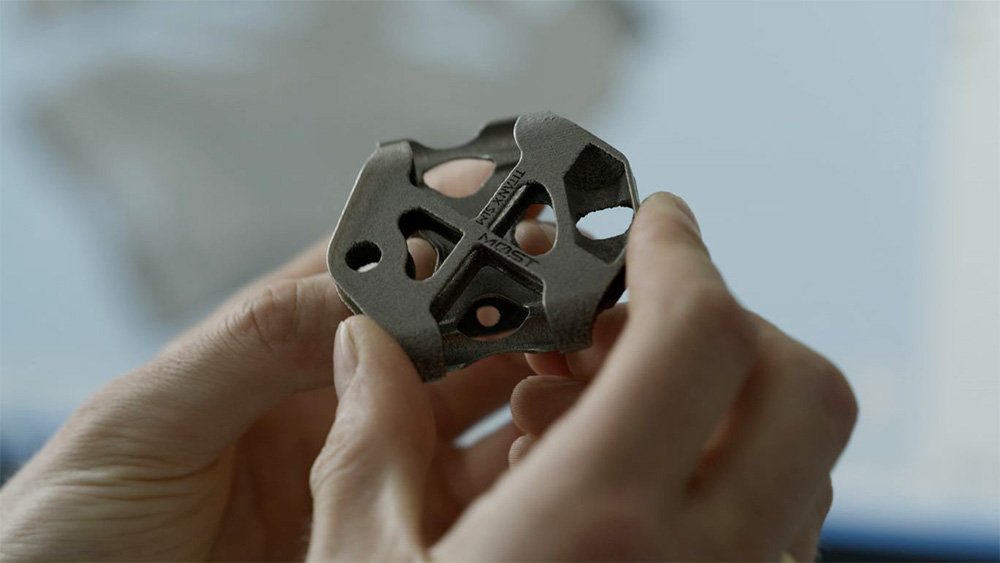
La velocità e la precisione della produzione 3DP oltre al componente finale leggero
hanno contribuito al successo della bicicletta di ultima generazione Dogma F
"Grazie a Materialise e alla nostra attenzione ai dettagli, abbiamo risparmiato 35 grammi solo sul piccolo morsetto reggisella", afferma Maurizio. “Considerando tutto ciò in prospettiva, si tratta di 8 grammi in più risparmiati rispetto alla riduzione di peso finale del reggisella stesso. I dettagli fanno la differenza. E, grazie alla stampa 3D, possiamo dimostrarlo concretamente.
“Ma non si tratta solo di risparmio di peso. Con l'accessibilità della stampa 3D, possiamo offrire questa tecnologia a molti altri e non solo ai migliori ciclisti che gareggiano al Tour de France. Possiamo offrirla a chiunque nel mondo".
Your Partner for Metal 3D Printing
Leave the complexity to the parts. As for your workflow, our one-stop-shop will keep it simple.