自転車競技愛好家にとってサイクリングとは、急な坂道を上り、長距離を疾走し、絶え間ない風と戦うことです。そのため、自転車の重量が大きな意味を持っています。「Dogma F 」はPinarello社が実現した、サイクリストが夢見てきた軽量モデルの新しいレーシングバイクです。
この唯一無二のバイクを作るために、革新的なパートナーと最新の技術が必要でした。シート部分の重量半減を実現させる大きな要因となったのはMaterialiseの金属3Dプリントサービスとオーダーメイドのワークフローでした。
課題
Pinarello社の目標である時間、予算、生産量を達成するとともに、シートクランプの軽量化を図る
ソリューション
Mateialiseコンピテンスセンターでカスタマイズされたワークフローで金属3Dプリント
結果
42.5%の軽量化と大量生産を実現
課題
自転車業界では、1gの差が大きく影響してきます。だからこそPinarello社の最新のモデルでは、他社製品のものよりも1gでも軽量化することを目標としました。もちろん軽量化以外の意味もありました。コストや品質、生産スピード、製造数などのバランスを取ることも重要でした。
Pinarello社 オペレーションのチーフ Maurizio Bellin氏は「Pinarello R&Dの課題はまさに軽量化でした」といいます。「選手が風を切って何キロも上ったりスプリントしたりする時、バイクが軽ければ軽いほど早く走れます。だからこそ、可能な限りの軽量化を目指したのです。」
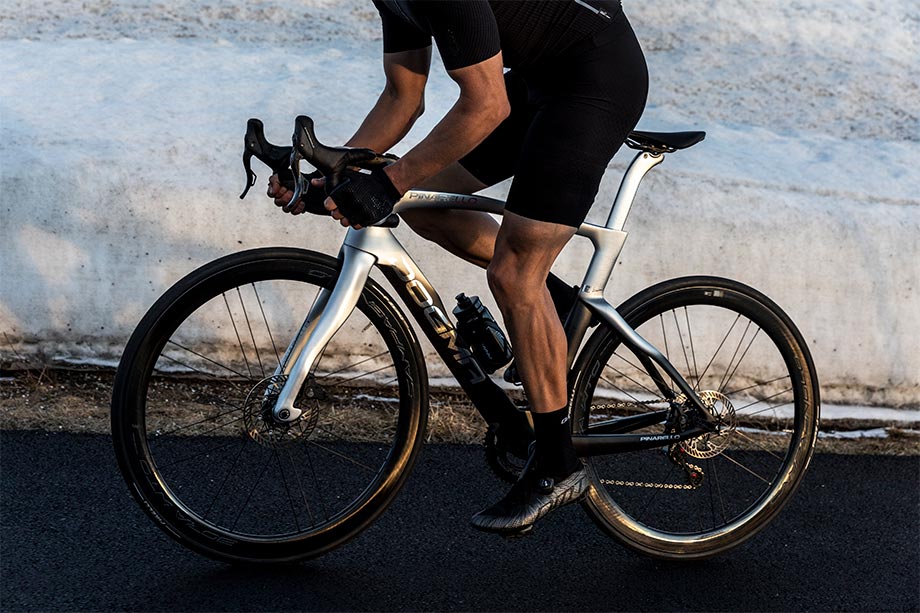
Pinarello社がこの新型バイクの設計目標に設定したのは軽量化
Pinarello社は強度と軽量化を両立させる技術に精通したサプライヤーと協力しながらプロジェクトを立ち上げました。従来の製造方法用シートクランプのデザインをもとに、軽量化を実現すべくMateialiseと3Dプリントの活用を開始したのです。
ソリューション
Materialiseチームは金属3Dプリントならではのデザインの自由度を知っているため、より軽量なシートクランプが作れると確信していました。このプロジェクトの課題は、数週間で大規模生産を実現させるということでした。Materialiseのデザインエンジニアリング、ソフトウェア、マニュファクチャリングの各チームは、目標達成のために一丸となって取り組むことが求められました。.
「ドイツのブレーメンにある私たちのメタルコンピテンスセンターには、Materialiseの専門知識が集約されています」とMaterialiseのテクニカルプロジェクトマネージャーであるPhilip Buchholzは言います。「この新しい施設では、社内のデザインスキル、開発部門の幅広い知識、製造プロセスが統合されているのです。」
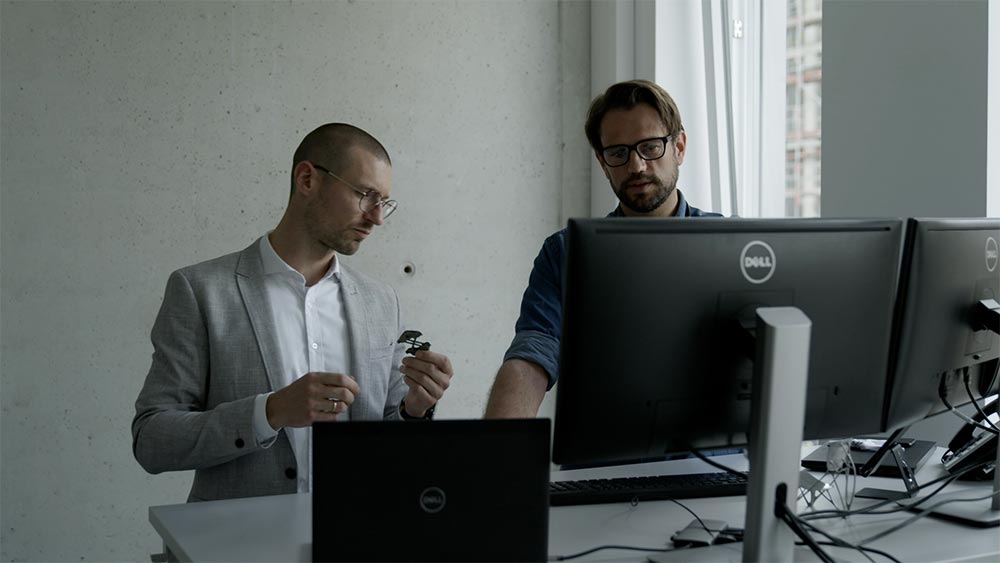
Materialiseのメタルコンピテンスセンターにて。ソフトウェア、デザイン、エンジニアリング各部門の専門家たちの知識を集めて金属3Dプリントを次のレベルへ
Materialiseのデザインエンジニア、Tim Hermanskiは、「デザイン、エンジニアリングはPinarello社との密な共同作業によって行われました」とい説明します。「デザインを繰り返す段階で、内部ではバーチャルなシミュレーションテストが実施されました。シートクランプは軽量化されていなければならず、しかし同時にサイクリストの体重を支えるための十分な強度も必要です。こうした内部テストを行うことで、最終的なパーツの造形可能性と信頼性を確保するための時間を短縮することができました。テスト完了後はチームは3DプリントしたパーツをPinarello社と共有し、独自のテストベンチやロードテスト、疲労試験などを実施しました」。
3Dプリント活用の主なメリットは、最終デザインの確定までのスピードが早いところです。従来の製造方法では、デザインに変更を加えるたびに新しい金型や複雑なCNCプログラミングを必要としていましたが、今回はそのような作業は行っていません。すべてのデザインはデジタルで行われ、調整も迅速に行われたのです。
パーツデザインに加えて、チームが取り組んだ課題は短時間で多くのパーツを造形するということでした。プロジェクトの目標は毎月、1か月以内に2,000個のパーツを造形すること。ここでいよいよMaterialiseの社内チームワークの見せどころです。チームメンバーはそれぞれが知恵を絞って、ラベリングや品質検査を含むフルサービスのカスタマイズされた生産ワークフローを作り、目標を達成したのです。
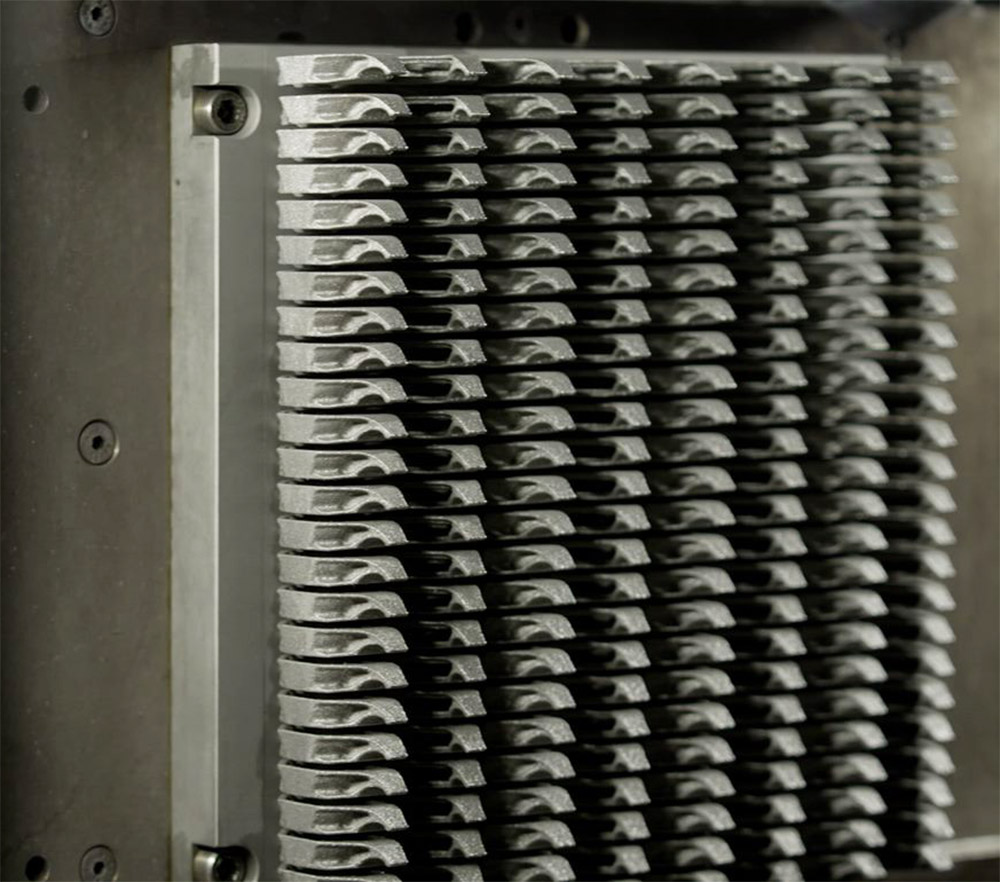
カスタムワークフローのおかげで、1か月以内に2,000個のパーツ造形が可能に
Philipはさらに言いました。「私たちは生産チェーンを産業化させる必要がありました。サポート生成や手動の後処理工程を必要としないパーツデザインとプロセスにすることで実現させました。それは造形時間の短縮にも繋がりました。カスタムパラメーターの設定が、造形時間を短縮し、必要な材料特性を満たし、そしてコストを最適化することでプロジェクトの実現性を高めたのです」。
「これを可能にしたのが Materialise Process Tuner です。このソリューションはプロセス開発を広範囲に”チューニング”するもので、2021年度に販売を開始する予定です。このソフトウェアはパラメーター設定を高速化するだけでなく、自動化によって人的ミスを減らし、今後の運用のためにデータベースで収集したデータと分析結果を集中管理します。Materialiseは最適な造形パラメータを数ヶ月ではなく数週間で開発ましたが、メタルコンピテンスセンターのソフトウェアチームとD&Eチームのノウハウを結集しなければ、このような成果は得られませんでした」。
結果
Pinarelloとの密なコラボレーションとMaterialiseチームの努力により、プロジェクトの目標を達成するパーツの提供を実現することができました。
3Dプリント専門家がデザインしたシートクランプは、AMならではの高いデザインの自由度を十分に活かし、適切な材料の使用で大幅な軽量化を実現しました。最終的にSLMで造形されたチタン製シートは、従来の製造プロセスで作られたアルミニウム製シートよりも42.5%軽量化されました。
3Dプリントが身近になったことで、ツール・ド・フランスに出場するトップ選手だけでなく、世界中の人にこの技術を提供できるようになりました。
— Pinarello社、チーフオペレーション 、Maurizio Bellin氏
Materialiseがこの規模の3Dプリントパーツの生産を実現したスピードも圧巻でした。デザインの最適化と生産プロセスの効率化で、2,000個のパーツを受注から納品まで、3週間で実現したのです。従来の製造方法だと、半年から1年前に注文が必要なスピード感で、特に世界的な現在用や生産能力の不足によって、サプライチェーンが影響を受けているこの時期にはリードタイムを長めにみる必要があります。今回は双方の拠点がヨーロッパだったこともいい結果をもたらしました。世界中のどのメーカーよりも、Materialiseはより早く、サステナブルな納品を目指します。
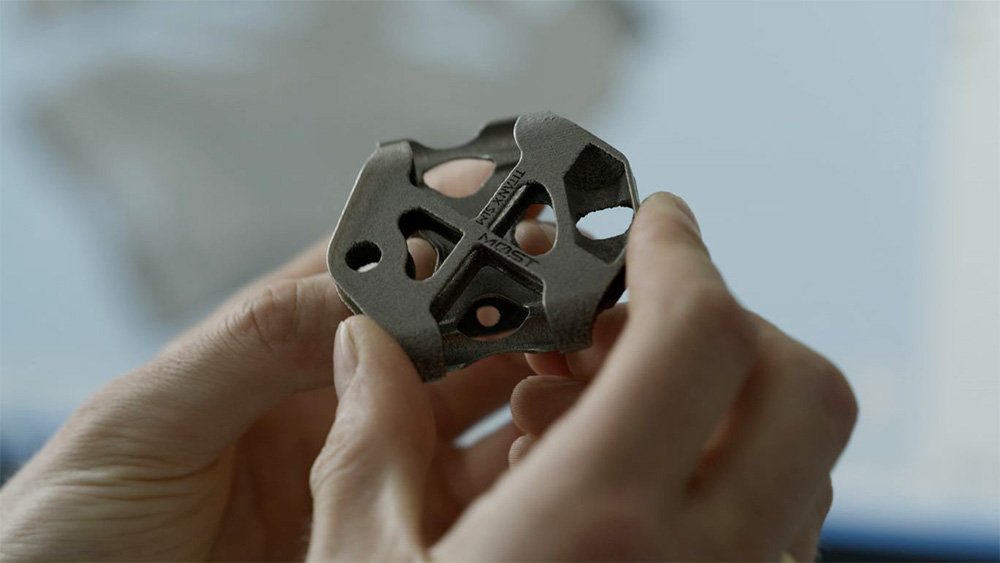
3Dプリントのスピードと精度 、軽量化された最終製品が最先端のバイク"Dogma F"を実現
「Materialiseと細部にこだわった結果、この小さなシートポストクランプだけで35gの軽量化に成功しました」とMaurizio氏は言います。「最終的な軽量化よりも8g軽くすることができたのです。細部の違いが重要であることを、3Dプリントの活用でそれを証明できたのです。しかし、軽量化だけがゴールではありません。3Dプリントの活用により、ツール・ド・フランスに出るトップ選手だけでなく、世界中の人に提供することができるようになったのです」。
Your Partner for Metal 3D Printing
Leave the complexity to the parts. As for your workflow, our one-stop-shop will keep it simple.