Para los amantes de la competición, hacer ciclismo significa remontar colinas escarpadas, correr a toda velocidad durante largas distancias y luchar contra vientos incesantes. El peso de la bicicleta marca la diferencia. La nueva bicicleta de carreras de Pinarello, Dogma F, es el modelo ligero con el que los ciclistas llevan tiempo soñando.
A fin de crear esta bicicleta única, necesitaban la ayuda de socios innovadores y la tecnología más vanguardista. Los servicios integrales de impresión 3D en metal de Materialise, así como sus flujos de trabajo personalizados, resultaron fundamentales para poder conseguirlo: reduciendo casi a la mitad el peso de un componente esencial del asiento.
Reto
Reducir el peso de las abrazaderas del sillín a la misma vez que cumplían con los objetivos en cuanto a plazos, presupuesto y producción de Pinarello
Solución
Impresión 3D en metal con un flujo de trabajo personalizado en el Metal Competence Center de Materialise
Resultado
Piezas que eran un 42,5 % más ligeras y podían imprimirse a escala con éxito
Reto
En el ciclismo de competición, cada gramo de peso importa. Por ese motivo, para el último lanzamiento de Pinarello, se centraron en una bicicleta de carreras que pesara mucho menos que las de sus competidores. Aunque, por supuesto, cumplir con este objetivo significaba mucho más que reducir el peso. El equipo necesitaba equilibrarlo con los costos, la calidad, la velocidad de producción y la cantidad de unidades fabricadas.
«El desafío para el departamento de I+D de Pinarello realmente fue centrarse en la reducción de peso», explica Maurizio Bellin, Jefe de operaciones de Pinarello. «Cuando los ciclistas van en subida y a toda velocidad durante muchos kilómetros contra el viento, cuanto más ligera sea la bicicleta, más rápido vas. Por eso queríamos conseguir el mínimo peso posible».
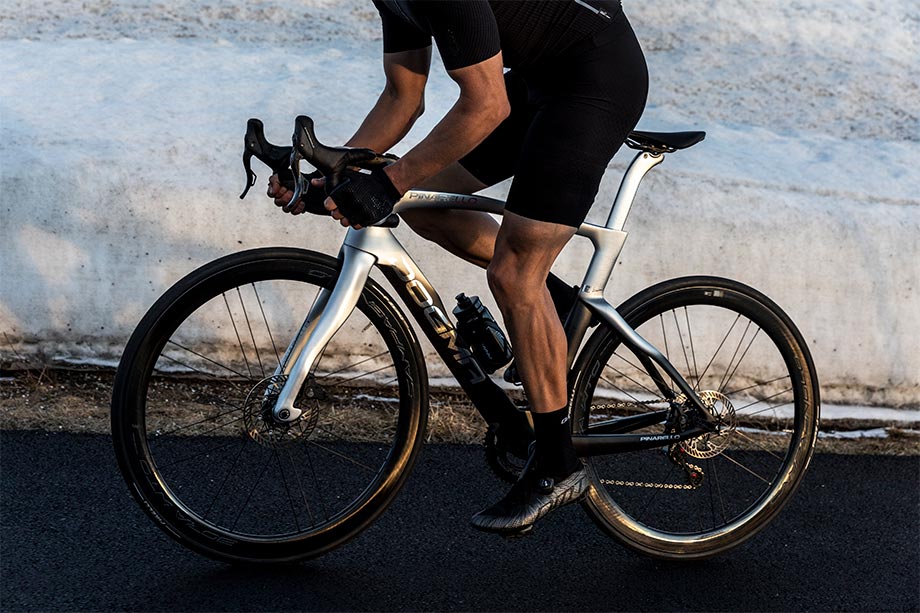
Uno de los principales objetivos de diseño de Pinarello para esta nueva bicicleta era la reducción de peso
Pinarello dio inicio al proyecto colaborando con varios proveedores con experiencia en tecnologías que prometían resultados robustos a la par que ligeros. Tenían un diseño original para sus abrazaderas de sillín que utilizaba técnicas de fabricación tradicionales, pero para alcanzar los resultados que querían en cuanto a peso acudieron a Materialise y a la impresión 3D.
Solución
El equipo de Materialise sabía que, gracias a la libertad de diseño que proporciona la impresión 3D en metal, podían crear una abrazadera mucho más ligera. El reto, en este caso, consistía en la fabricación de las piezas serie en tan solo unas semanas. Los equipos internos de diseño e ingeniería, software y fabricación de Materialise necesitaban trabajar codo con codo a fin de alcanzar los objetivos de producción.
«Nuestro Metal Competence Center en Bremen, Alemania, alberga todo el conocimiento y la experiencia necesarios bajo el mismo techo», explica Philip Buchholz, Director de proyecto técnico de Materialise. «En estas nuevas instalaciones, reunimos nuestras habilidades de diseño internas, el amplísimo conocimiento de nuestro departamento de investigación y desarrollo, y nuestros procesos de producción industrializados».
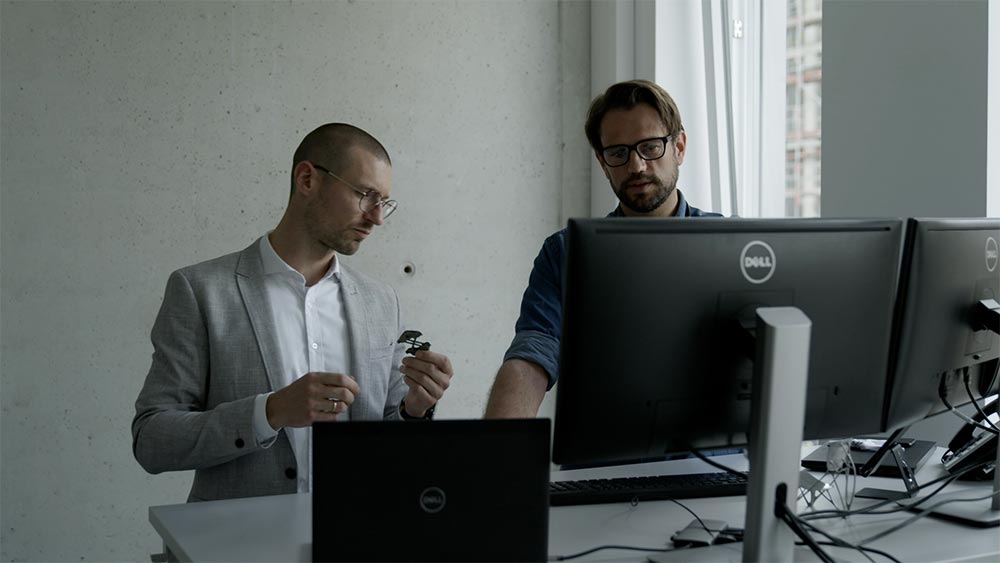
En nuestro Metal Competence Center, podemos combinar el conocimiento de
expertos en software, diseño e ingeniería y así llevar a la impresión 3D en metal al siguiente nivel
«El diseño y la ingeniería se realizaron trabajando muy estrechamente con Pinarello», declara Tim Hermanski, ingeniero de diseño de Materialise. «Con cada iteración de diseño, llevábamos a cabo pruebas de simulación virtual primero. Necesitábamos que la abrazadera del sillín fuera ligera, pero esta pieza debe tener la suficiente resistencia para sujetar el peso del ciclista. Estas pruebas internas ahorraron mucho tiempo, y ayudaron a garantizar que pudieran imprimirse y fueran fiables en la fase final». Una vez que finalizaron las pruebas, el equipo compartió los diseños impresos en 3D con Pinarello a fin de llevar a cabo su propia batería de pruebas físicas, como pruebas de fatiga en un banco de pruebas y en carretera.
Un beneficio enorme de la impresión 3D, en este caso, fue la velocidad con la que completaron el diseño. Mientras que la fabricación convencional necesita de nuevos moldes y una compleja programación de CNC durante cada actualización del diseño, cosa que no sucede aquí. Los diseños son completamente digitales y, por lo tanto, pueden ajustarse con rapidez.
Además del propio diseño de la pieza, los equipos necesitaban solucionar el reto que constituía producir tantísimas unidades en tan poco tiempo. El proyecto requería la impresión de 2000 piezas individuales en menos de un mes, cada mes. Y es en este punto donde se demostró una vez más lo valiosa que es la colaboración interna de Materialise. El equipo unió fuerzas para crear un flujo de trabajo de producción integral y personalizado, en el que se incluía el etiquetado y el control de calidad, que consiguiera alcanzar el objetivo final.
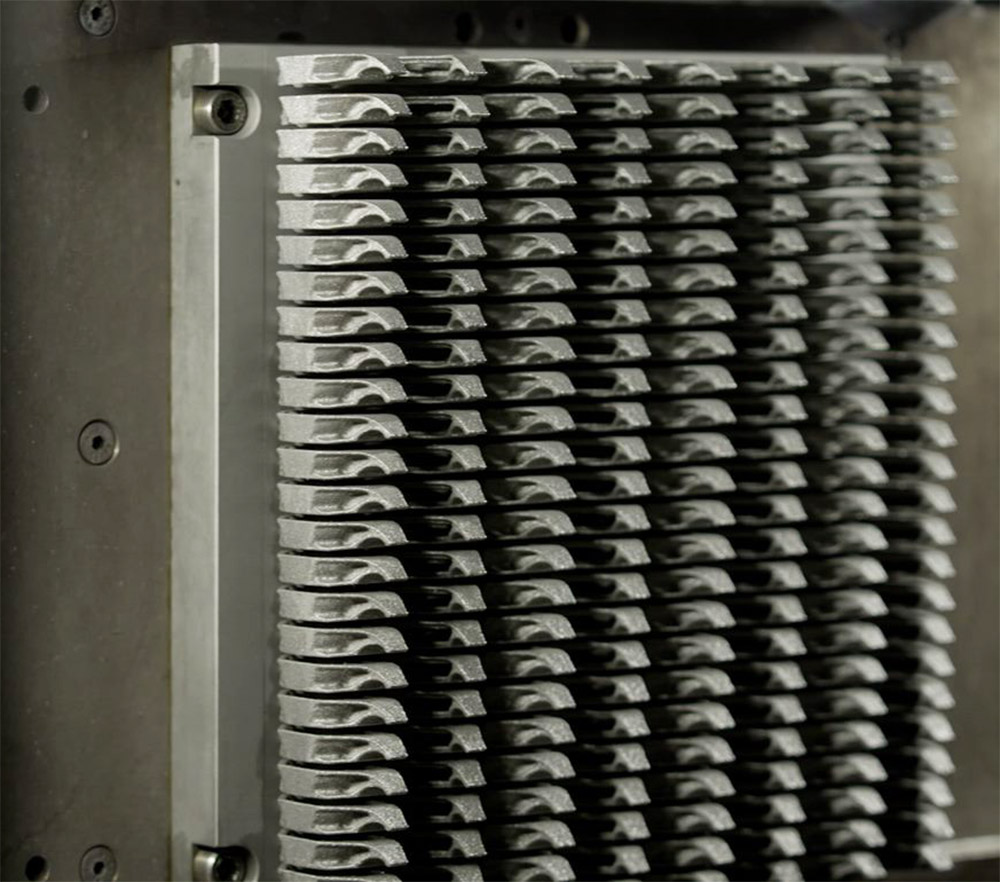
Gracias a un flujo de trabajo de producción personalizado,
nuestro equipo imprimió 2000 piezas en menos de un mes
«Tuvimos que incluir la industrialización en nuestra cadena de producción», explica Philip. «Lo hicimos diseñando una pieza y un proceso que no necesitara estructuras de apoyo o fases de posprocesamiento manual. La eliminación de estos pasos nos ahorró mucho tiempo durante la fabricación. También creamos un conjunto de parámetros de impresión personalizados que aceleraba el tiempo de impresión, cumplía con las propiedades del material requeridas, e hizo que el proyecto fuera factible optimizando los costes.
«Conseguimos todo esto con Materialise Process Tuner: una solución que vamos a sacar al mercado a finales de este año y que "afina" ampliamente el desarrollo de los procesos. Este software no solamente acelera la configuración de los parámetros, sino que también reduce errores gracias a la automatización, así como que ofrece información interna y datos estadísticos inteligentes almacenados en una única base de datos centralizada para operaciones futuras. Desarrollamos parámetros de impresión optimizados en unas pocas semanas, en lugar de meses. No hubiéramos podido conseguirlo sin el know-how combinado de nuestros equipos de software y de diseño e ingeniería en el Metal Competence Center».
Resultado
Gracias a la estrecha colaboración con Pinarello y el impresionante esfuerzo del equipo interno, Materialise aportó una pieza que permitió a Pinarello alcanzar su meta.
Los expertos de impresión 3D diseñaron la abrazadera del sillín de una forma en la que se aprovecha la libertad de diseño de AM y eligieron el material adecuado para conseguir una importante reducción en el peso. Al final, la pieza de titanio, impresa mediante fusión selectiva con láser (SLS), fue un 42,5 % más ligera que el diseño de aluminio original, fabricado a través de un proceso de producción tradicional.
Con la accesibilidad de la impresión 3D, podemos ofrecer esta tecnología a muchas más personas y no solamente a los mejores ciclistas del mundo que compiten en el Tour de Francia. Podemos ofrecérsela a todo el mundo».
— Maurizio Bellin, Jefe de operaciones de Pinarello
También fue impresionante la velocidad en la que Materialise fabricó las piezas impresas en 3D de esta serie. Al optimizar el diseño y los procesos de fabricación, el equipo pasó de realizar pedidos a entregar 2000 piezas en tres semanas, hasta alcanzar 20.000 unidades. Con el fin de ejemplificar esta velocidad, el proceso de fabricación tradicional necesita que los pedidos de este calado se realicen con una antelación de entre 6 y 12 meses, especialmente en tiempos como estos en los que las cadenas de suministro se han visto afectadas por la escasez mundial en cuanto a materia prima y capacidad de producción. Estar situados en Europa también supuso una ventaja muy importante en este caso. Materialise ofreció plazos de entrega más rápidos y una entrega más sostenible, frente a lo que hubiera supuesto contar con un fabricante al otro lado del mundo.
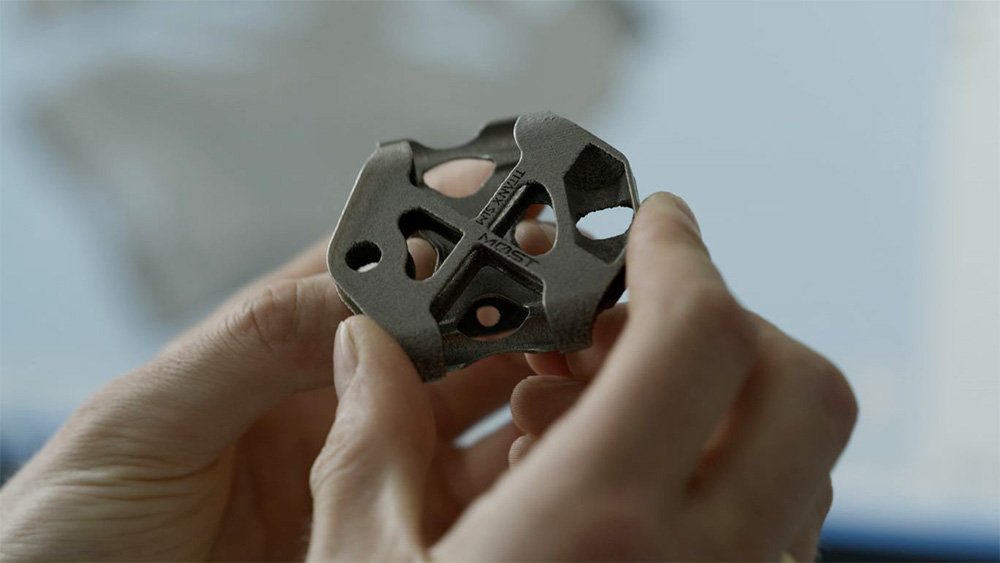
La velocidad y la precisión de la fabricación de impresión 3D unidas a la ligereza final
de la pieza, permitieron el éxito de la bicicleta de vanguardia Dogma F
«Gracias a Materialise y a nuestra atención al detalle, hemos ahorrado 35 gramos solo en la pequeña abrazadera de la tija del sillín», dice Maurizio. «Para ponerlo en perspectiva, eso son 8 gramos más que nos hemos ahorrado en la reducción de peso final de la tija misma». Son los pequeños detalles los que marcan la diferencia. Y gracias a la impresión 3D, podemos demostrarlo realmente.
«Pero no solo se trata del ahorro en cuanto al peso». Con la accesibilidad de la impresión 3D, podemos ofrecer esta tecnología a muchas más personas y no solamente a los mejores ciclistas del mundo que compiten en el Tour de Francia. Podemos ofrecérsela a todo el mundo».
Your Partner for Metal 3D Printing
Leave the complexity to the parts. As for your workflow, our one-stop-shop will keep it simple.