InMotion, un team di studenti di ingegneria della Technical University di Eindhoven, si è posto un obiettivo particolarmente impegnativo: concorrere nella leggendaria 24 ore di Le Mans entro il 2019. A supporto di questa candidatura, si son posti prima un obiettivo: battere il record di pista per le auto elettriche nel circuito del Nürburgring in Germania il prossimo anno.
Se il tuo obiettivo è produrre l’auto elettrica più veloce al mondo, ogni grammo risparmiato conta: così InMotion ha studiato la possibilità di utilizzare bracci oscillanti (detti anche giunti a Y) leggeri stampati in 3D per la sospensione. I bracci oscillanti sono le parti che collegano i mozzi al telaio della macchina. In breve, mantengono le ruote in sede e fanno fronte a tutte le forze in gioco. Un componente dell’automobile a dir poco fondamentale.
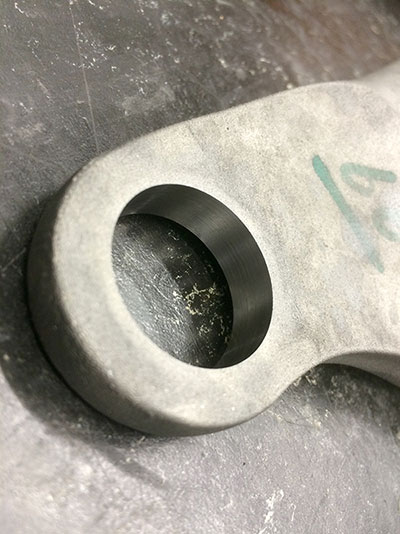
Resistente e leggero: ottimizzazione del peso con il titanio
Sebbene il titanio abbia un peso specifico molto contenuto, il team di progettisti Materialise aveva un suggerimento per rendere ancora più leggera la parte inizialmente progettata da InMotion. Grazie al nostro software proprietario Materialise 3-matic, il team software Materialise è riuscito a riempire le cavità con una struttura a nido d’ape, per rendere la parte ancora più leggera senza sacrificarne la robustezza.
Rapidità e precisione: lo stabilimento per la stampa 3D in metallo
Come ulteriore sfida, InMotion desiderava trovare un sistema per evitare, durante il processo di stampa, l’uso di strutture di supporto che alla fine si sarebbero dovute rimuovere manualmente. I bracci sospensione dell’auto sono collegati ai mozzi tramite testine sferiche, e l’accoppiamento di questi componenti è di fondamentale importanza. InMotion non voleva rischiare che la rimozione di eventuali strutture di supporto ponesse eventuali problemi dell’ultimo minuto all’accoppiamento. Jannis Kranz, progettista per la stampa 3D in metallo in Materialise, afferma:
“Grazie al nostro software, siamo in grado di individuare un orientamento di costruzione che ci permetta di stampare la parte come struttura autosupportata, eliminando la necessità di generare una struttura di supporto. Per il nostro stabilimento di stampa in metallo di Brema è stata una sfida notevole ma, tutto sommato, il tempo di consegna dell’intero progetto è stato inferiore a una settimana lavorativa.”
E non è stato soltanto veloce: è stata anche ottenuta la precisione desiderata. “L’accoppiamento preciso necessario per il montaggio dei bracci della sospensione non ci ha dato alcun problema”, afferma Rogier di InMotion. “La precisione è stata elevata: ogni cosa è andata perfettamente al suo posto fin dal primo momento. Eventuali piccole imperfezioni sarebbero venute fuori durante il montaggio.”
Tenete d’occhio questa macchina quando inizierà a gareggiare il prossimo anno, ma fate attenzione, perché potrebbe andare davvero troppo veloce.
All images copyright of Gerlach Delissen and InMotion Automotive