InMotion, eine Gruppe Studenten der Ingenieurswissenschaften an der Technischen Universität Eindhoven, hat sich ein hohes Ziel gesteckt: die Teilnahme am legendären 24-Stunden-Rennen von Le Mans im Jahr 2019. Um Ihre Teilnahmechancen zu verbessern, wollen sie im kommenden Jahr zunächst den Rundenrekord für elektrische Fahrzeuge auf dem Nürburgring brechen.
Wenn Sie sich das Ziel gesetzt haben, das schnellste elektrische Auto der Welt zu bauen, zählt jede Möglichkeit der Gewichtsoptimierung. Aus diesem Grund hatte InMotion die Idee, leichte, mit 3D-Druck gefertigte Y-Gelenke für die Querlenkeraufhängung zu verwenden. Die Y-Gelenke verbinden die Stützen über die Querlenker mit der Fahrzeugkarosserie. An ihnen sind kurz gesagt die Räder befestigt und sie absorbieren alle einwirkenden Kräfte. Es handelt sich also um ein ziemlich wichtiges Teil.
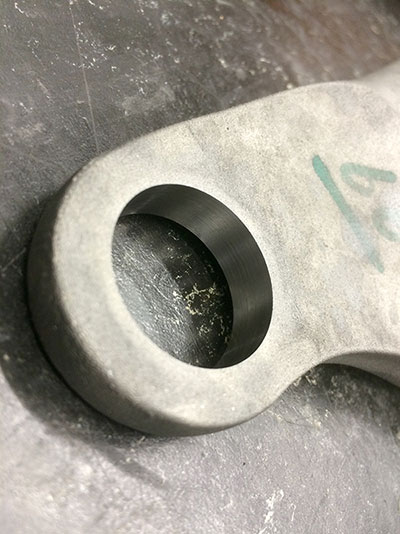
Stark und leicht: Gewichtsoptimierung mit Titan
Obwohl Titan bereits ein äußerst geringes Gewicht hat, unterbreitete das Entwicklungsteam von Materialise einen Vorschlag, um das ursprünglich von InMotion konstruierte Teil noch leichter zu gestalten. Mit unserem eigenen Softwareprogramm 3-maticSTL konnte das Softwareteam von Materialise die Hohlräume mit einer Wabenstruktur ausfüllen, um Gewicht ohne Abstriche bei der Stabilität zu reduzieren.
Schnell und präzise: das 3D-Metalldruckwerk
Eine weitere Herausforderung bestand darin, dass InMotion die Verwendung von Stützstrukturen während des Druckvorgangs vermeiden wollte, da diese letztendlich manuell entfernt werden müssen. Die Querlenker sind über sphärische Kugellager mit den Stützen verbunden und diese müssen eine einwandfreie Passform aufweisen. InMotion wollte nicht, dass sich die Entfernung von Stützstrukturen in letzter Minute negativ auf die Passform auswirkt. Jannis Kranz, Konstruktionsingenieur für 3D-Metalldruck bei Materialise: „Unsere Software ermöglicht es uns, eine Konstruktionsausrichtung zu finden, mit der wir das Teil als selbsttragende Struktur drucken können und keine generierte Stützstruktur benötigen. Das war eine große Herausforderung für unser Metalldruckwerk in Bremen, aber alles in allem lag die Vorlaufzeit für das gesamte Projekt bei weniger als einer Arbeitswoche.“
Und es ging nicht nur schnell, die gewünschte Präzision wurde auch erreicht. „Die für die Montage der Querlenker geforderte präzise Passform verursachte keinerlei Probleme“, so Rogier von InMotion. „Die Genauigkeit war äußerst hoch: alles passte von Anfang an perfekt. Jede noch so kleine Unvollkommenheit hätte sich bei der Montage bemerkbar gemacht.“
Halten Sie Ausschau nach diesem Auto, wenn es ab kommendem Jahr am Rennbetrieb teilnimmt: aber Achtung, es könnte an Ihnen vorbei rauschen.
All images copyright of Gerlach Delissen and InMotion Automotive