InMotion, – zespół studentów–inżynierów z Uniwersytetu technicznego w Eindhoven – postawił sobie trudne wyzwanie: wziąć udział w legendarnym 24-godzinnym wyścigu Le Mans do 2019 roku. Jako wsparcie swojej kandydatury zespół zamierza najpierw pobić rekord na torze elektrycznym w Nürburgring w Niemczech w przyszłym roku.
Jeśli zamierzasz stworzyć najszybszy samochód elektryczny na świecie, znaczenie ma optymalizacja każdego grama masy: InMotion prowadzi badania nad pomysłem przy użyciu wahaczy drukowanych w technologii druku 3D (znanych jako złącza typu Y). Wahacze są częścią łączącą kolumnę z nadwoziem samochodu. W skrócie utrzymują one koło na miejscu i przejmują na siebie wszystkie wywierane siły. Jest to, mówiąc delikatnie, kluczowy element samochodu.
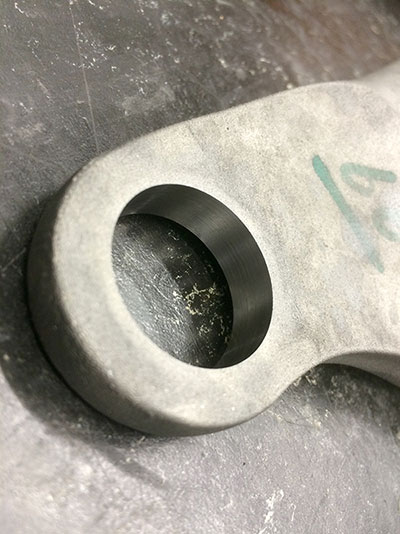
Mocne i lekkie: optymalizacja masy dzięki zastosowaniu tytanu
Pomimo że tytan ma bardzo niski ciężar właściwy, zespół inżynierów z Materialise otrzymał sugestię, aby jeszcze bardziej zmniejszyć masę projektowanych przez InMotion części. Przy użyciu opatentowanego oprogramowania Materialise 3-matic zespół ds. oprogramowania firmy Materialise wypełnił wgłębienia strukturą w kształcie plastra miodu, aby zmniejszyć jej masę bez wpływu na wytrzymałość.
Szybka i precyzyjna: fabryka druku 3D w metalu
Dodatkowym wyzwaniem było uniknięcie konieczności stosowania konstrukcji wsporczej podczas procesu drukowania, które musiałyby być ręcznie usuwane. Ramiona zawieszenia samochodu połączone są z kolumnami przez łożyska kulkowe i dopasowanie tych komponentów ma krytyczne znaczenie. Zespół InMotion chciał uniknąć demontażu jakichkolwiek konstrukcji wsporczych, aby w najmniejszym stopniu nie zagrażać finalnemu spasowaniu. Jannis Kranz, inżynier ds. projektu druku 3D w metalu firmy Materialise, mówi:
“Dzięki naszemu oprogramowaniu możemy precyzyjnie orientować elementy w komorze roboczej, bez konieczności stosowania konstrukcji wsporczej. To było wielkie wyzwanie dla naszejfabryki druku w metalu w Bremen, tym bardziej, że czas realizacji całego projektu wyniósł jeden tydzień roboczy.”
Nie tylko wywiązaliśmy się szybko z zadania, osiągnęliśmy również wymaganą precyzję. „Precyzyjne dopasowanie niezbędne do montażu ramion zawieszenia nie sprawiło żadnego problemu” mówi Rogier z zespołu InMotion. „Dokładność była bardzo wysoka, wszystko pasowało doskonale od samego początku. Jakiekolwiek minimalne niedoskonałości wyszłyby na jaw podczas montażu”.
Miejcie na oku ten samochód, gdy rozpocznie wyścigi w przyszłym roku: być może będzie jednak zbyt szybki.
All images copyright of Gerlach Delissen and InMotion Automotive