CORPORATE
Die Möglichkeiten der Additiven Fertigung erforschen: Optimierung der Produktion mit Hyundai Lifeboats
Der Wert der additiven Fertigung (AM-Fertigung) ist mittlerweile unbestritten. Sie wird selbst in den anspruchsvollsten Branchen wie dem Gesundheitswesen und der Luft- und Raumfahrt regelmäßig eingesetzt, und 90 % der Hersteller halten sie für unerlässlich, um zukunftssicher zu werden. Aber der Weg zum Erfolg in der AM-Fertigung ist keine einfache Aufgabe. Materialise Mindware, unser Beratungsteam für den 3D-Druck, beschreibt die verschiedenen Schritte, die den Kunden auf diesem Weg begleiten. Erfahren Sie, wie sie Hyundai Lifeboats durch die erste Phase – Erkunden – begleitet und maßgeschneiderte Vorrichtungen entwickelt haben, um die Produktion von Rettungsbooten zu optimieren.
Der Erfolgsweg der AM-Fertigung
Wie bei jeder anderen Fertigungstechnologie ist auch die Entwicklung von transformativen Produkten ein komplexer Prozess. Er beginnt immer mit der Identifizierung der richtigen Gelegenheit, geht über die angewandte Forschung und Entwicklung, um die Machbarkeit der Idee zu prüfen, und führt schließlich zur zertifizierten Produktion, um die ursprünglichen Geschäftsziele zu verwirklichen. Das ist bei der additiven Fertigung nicht anders.
Es gibt kein Handbuch, das Ihnen die Integration der AM-Fertigung in Ihr Unternehmen erklärt. Es kann sich verwirrend, riskant und überwältigend anfühlen, weil so viele Faktoren berücksichtigt werden müssen und die nächsten Schritte nicht immer einfach sind.

Das Team von Mindware und sein Drei-Phasen-Modell führen Unternehmen durch ihre Reise im Bereich der AM-Fertigung
In den vergangenen 30 Jahren haben wir bei Materialise diesen Weg von der Ungewissheit bis hin zu vollautomatischen, zertifizierten Fertigungslinien viele Male durchlaufen. Um Sie nun auf diesem Weg zu begleiten, haben wir ein Modell entwickelt, das die in den drei Hauptphasen zu beachtenden Schritte und Schlüsselfragen aufzeigt. Bei der Entwicklung dieses Modells haben wir die einzigartigen Herausforderungen berücksichtigt, die sich aus den Besonderheiten der AM-Fertigung ergeben – zum Beispiel:
-
Wenn Sie gerade erst damit begonnen haben, den 3D-Druck für Ihr Unternehmen zu erforschen, wie können Sie feststellen, ob diese Technologie die Antwort auf die strategischen Anforderungen Ihres Unternehmens ist?
-
Wenn Sie in Forschung & Entwicklung für Ihre 3D-gedruckte Anwendung investieren, mit welchen Experimenten können Sie herausfinden, welche Designvarianten Ihre Produktanforderungen für ein bestimmtes Material oder eine bestimmte Technologie erfüllen?
-
Wenn Sie bereits in einer Phase der routinierten AM-Produktion sind und eine erfolgreiche Skalierung ermöglichen wollen, wie ermitteln Sie dann die optimalen Fertigungsstrategien, um die Ausschussraten zu reduzieren?
Ganz gleich, aus welcher Branche Sie kommen oder was Sie erreichen wollen, Sie werden auf eine der Phasen des Erkundens, Experimentierens oder Aktivierens treffen. Je nachdem, in welcher Phase Sie sich befinden, kann Mindware Sie bei der Bewältigung der vorrangigen Herausforderungen unterstützen und Ihnen helfen, Ihren AM-Zielen einen Schritt näher zu kommen.
Im folgenden Fall konzentrieren wir uns auf die erste Phase, d. h. das Erkunden. In dieser Phase erkunden und erforschen die Kunden die Technologie. Dazu gehören diejenigen, die ihre geschäftlichen Herausforderungen mit der AM-Fertigung lösen wollen, aber noch nicht genau wissen, an welcher Stelle der 3D-Druck einen Mehrwert bieten könnte und mit welcher(n) Anwendung(en) sie beginnen sollen.
Dieser Abschnitt des Modells hebt die wichtigsten Herausforderungen hervor, die in der Erkundungsphase zu bewältigen sind, und geht auf die Fragen ein, bei deren Beantwortung unser Team helfen kann.

In der ersten Phase, d. h. der Erkundungsphase, erforschen Kunden die AM-Fertigung detailliert.
Hyundai Lifeboats: Wo war die Schwachstelle im Produktionsprozess?
Unser Projekt mit Hyundai Lifeboats begann im Februar 2018 mit einer Anfrage der Regierung von Ulsan, Südkorea. Die verarbeitende Industrie in Ulsan boomt, und die Regierung beauftragte uns, mit mehreren Unternehmen Kontakt aufzunehmen, um die Entwicklung von 3D-gedruckten Anwendungen zu beschleunigen.
Dieses Projekt war der Inbegriff der Erkundung. Genauso wie ich, Director of Innovation bei Materialise, und andere Teammitglieder von Mindware keine Erfahrung oder Kenntnisse in der Herstellung von Rettungsbooten hatten, waren dem Hyundai-Team die Möglichkeiten und Grenzen des 3D-Drucks nicht bekannt. Also bestand der erste Schritt in diesem Projekt darin, unsere beiden Welten zusammenzubringen, um eine relevante geschäftliche Herausforderung für Hyundai Lifeboats zu identifizieren, von der wir glaubten, die unserer Meinung nach am besten durch additive Fertigung gelöst werden konnte.
Doch dies war einfacher gesagt als getan. Wir stürzten uns in einen interaktiven Workshop, in dem wir die Perspektiven, Erwartungen und Schwachstellen beider Seiten kennenlernten. Wir erörterten zunächst, wie die AM-Fertigung den Wert eines Bootes steigern könnte – durch höhere Geschwindigkeit, gesteigerte Leistung und erweiterte Funktionalität – doch das Team von Hyundai reagierte zögerlich.
Als wir sie nach ihren Vorstellungen fragten, lenkten sie den Fokus schnell auf die Kosten eines einzelnen Bootes. Sie hofften, dass sie mithilfe des 3D-Drucks einfach einen Knopf drücken, eine Tasse Kaffee trinken und ihre Boote in einem Arbeitsgang drucken könnten – und damit in Sachen Geschwindigkeit den derzeitigen Montage- und Produktionsprozess überholen würden. Aufgrund der Größe des Bootes und der spezifischen Materialien mussten wir diesen Traum in Bezug auf die AM-Fertigung zerstören, aber zumindest haben wir ihr Hauptanliegen verstanden: Produktionseffizienz.
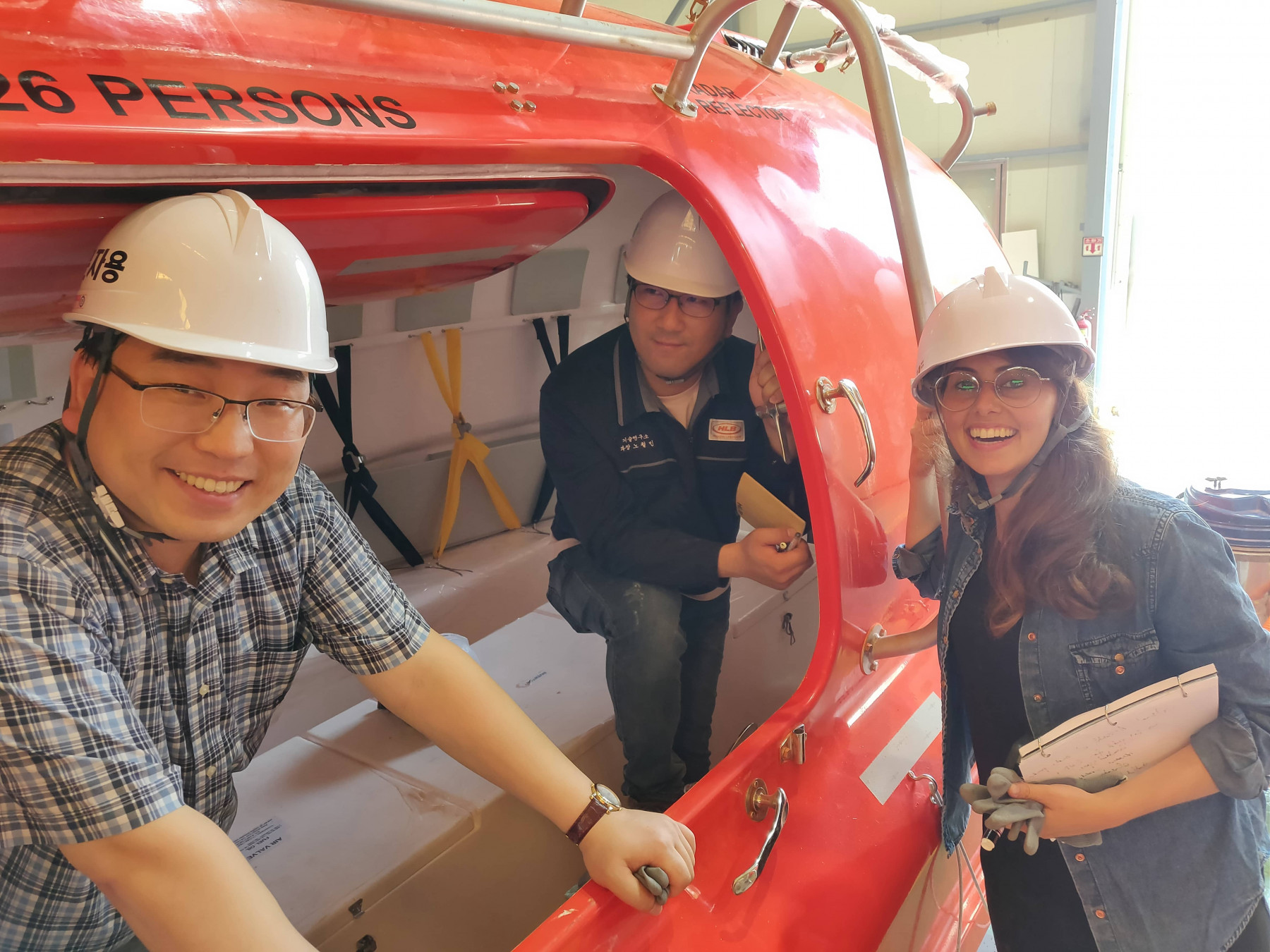
Das Mindware-Team verbrachte drei Stunden mit der Analyse der Produktion, um die Hauptblockaden zu ermitteln
So wertvoll die additive Fertigung auch sein kann, sie ist keine schnelle Lösung. Wie ich bereits erwähnt habe, handelt es sich um eine komplette Reise. Also begann unser Team mit einem Rundgang durch die Produktion. Dabei betrachteten wir ihren Prozess aus einer neuen Perspektive, stellten bei jedem Schritt geschäftliche und technische Fragen und entdeckten, warum Effizienz eines ihrer Hauptanliegen war: Die Rettungsboote wurden zu 100 % von den Arbeitern in der Werkstatt handgefertigt. Bis zu 30 % entfielen auf Nacharbeiten und weitere 30 % auf Ausschussraten.
Als wir nach der Besichtigung wieder zusammenkamen, zeichneten wir alle wichtigen Schritte des gesamten Produktionsprozesses auf, um die größten Ineffizienzen zu ermitteln, und bestimmten den Schritt, bei dem der 3D-Druck unserer Meinung nach die größten Auswirkungen haben könnte: die Türmontage. Bisher mussten die Arbeiter in der Werkstatt jede 20 kg schwere Tür anheben, sie manuell ausrichten und mit dem Rest des Bootes zusammenbauen. Das ließ natürlich Raum für Fehler. Wenn beim Spritzwassertest aufgrund von Fehlern beim Zusammenbau der Tür eine undichte Stelle entdeckt wurde, musste der Prozess von vorne beginnen, wobei die Tür erst zerlegt und dann wieder zusammengebaut werden musste.
Ihr Team hatte sich damit abgefunden, dass jedes Boot diesen Prozess zwei bis drei Mal durchlaufen würde. Und jede Nacharbeit kostete sie wertvolle Zeit und Geld. Aber wir wussten, dass es einen besseren Weg geben musste.
3D-Druck für reibungslose Abläufe
Der Einsatz von 3D-Druck zur Optimierung der Ausrichtung war für uns nichts Neues. Wir hatten bereits Erfahrung mit der Entwicklung von 3D-gedruckten Schablonen, die Chirurgen bei der Durchführung präziserer Operationen helfen. Wir haben Automobilunternehmen geholfen, Buchstaben auf der Rückseite von Autos mit 3D-gedruckten Vorrichtungen auszurichten.
Nachdem wir so viel Zeit damit verbracht hatten, das Problem sorgfältig zu betrachten und unsere Strategie zu planen, waren wir bereit, die Ärmel hochzukrempeln und eine Lösung zu entwickeln. Und genau in diesem Moment ereignete sich mein Lieblingsmoment auf unserer Reise der gemeinsamen Kreation.
Wir fingen an, uns Gedanken zu machen, und mit dem Team von Hyundai Lifeboats kamen wir trotz unserer unterschiedlichen Sprachen, Unternehmen und Rollen zusammen, um die richtige Lösung zu finden. Und dann begannen wir zu entwerfen. Und umzugestalten. Und noch mehr umzugestalten. Bis wir fünf Whiteboards später alle zurücktraten und wussten, dass wir die richtigen Lösungen konzipiert hatten: drei multifunktionale Vorrichtungen, die in den verschiedenen Schritten des Produktionsprozesses eingesetzt werden können. Genauer gesagt, eine Vorrichtung für die Qualitätskontrolle und ein System für Ausrichtungs- und Positionierungsvorrichtungen.
Unter der Leitung von Dries Vandecruys entwarfen die Designer und Ingenieure von Materialise die Lösung mit Blick auf die AM-Fertigung, um die Möglichkeiten der Technologie vollumfänglich zu nutzen
Nachdem unsere drei Tage mit dem Team von Hyundai Lifeboats vorbei waren, kehrten wir nach Belgien zurück, wo unsere Ingenieure das von uns auf dem Whiteboard erstellte Konzept in ein digitales Design umwandelten. Anschließend erbrachten wir den greifbaren Nachweis des Konzepts mit unseren Prototyping-Technologien.
Drei Wochen später kehrten wir mit dem Konzeptnachweis in der Hand nach Korea zurück, um die neuen Systeme zusammen mit dem Team von Hyundai Lifeboats zu messen und zu installieren. Unsere ersten Ergebnisse waren sehr vielversprechend. Die Bediener mussten die schweren Türen nicht mehr in Position heben. Sie konnten die Tür einfach auf dem System positionieren und mithilfe von Knöpfen und Anzeigen die Tür beim ersten Mal richtig ausrichten.
Das war die perfekte Lösung. Durch unsere Hingabe in der Erkundungsphase – Fragen stellen, das Team schulen und herausfinden, welche Herausforderung wir angehen sollten – hatten wir in nur sechs Wochen eine testreife Lösung für ihr jahrzehntelanges Problem gefunden.
Wir kombinierten all unsere einzigartigen Erfahrungen, sei es in der Beratung, im AM-Design oder in der Konstruktion von Rettungsbooten, um eine Schwachstelle von Hyundai in der Produktionslinie ihrer Rettungsboote erfolgreich zu identifizieren und zu beheben. Wir befassten uns eingehend mit ihren Prozessen, Herausforderungen, Zielen und Erwartungen, um mithilfe der additiven Fertigung eine Lösung zu entwickeln, die einen großen Unterschied in ihren Abläufen machen würde.
Entdecken Sie die AM-Fertigung mit Mindware
Wenden Sie sich an unsere Experten und finden Sie heraus, wie wir Sie auf Ihrer AM-Reise unterstützen können.