Es kostet viel Zeit und Mühe, ein neues Material, einen neuen Prozess oder eine neue Maschine für die additive Fertigung von Metall (AM-Fertigung) zu qualifizieren. Es müssen viele Experimente durchgeführt werden, um die Abhängigkeiten verschiedener Parameter wie Laserleistung, Abtastgeschwindigkeit, Schraffurabstand, Schichtdicke usw. zu testen. Sie können sich vorstellen, wie viel Zeit für die Einrichtung der Tests, die Aufzeichnung der Daten, die Analyse der Ergebnisse und vieles mehr benötigt wird. Rosswag Engineering hat mehr als 40 Werkstoffe qualifiziert, sodass das Team mit diesen Aufgaben und den damit verbundenen Schwierigkeiten bestens vertraut ist. Doch seit der Einführung von Materialise Process Tuner in den Arbeitsablauf hat sich dieses Unterfangen erheblich verbessert.
Herausforderung
Reduzierung des Zeitaufwands für die Einrichtung von Experimenten zur Parameterqualifizierung
Lösung
Process Tuner automatisiert die Einrichtung von komplexen Parameterstudien
Ergebnis
Das Einrichten von Experimenten, was früher fast einen ganzen Tag in Anspruch nahm, dauert jetzt nur noch 20 bis 30 Minuten
Herausforderung
Mit über 100 Jahren Erfahrung in der Verarbeitung von mehr als 400 Metallwerkstoffen war Rosswag gut positioniert, um in den Bereich des 3D-Drucks zu expandieren. Seit 2014 hat das Team von Rosswag über 40 Metallwerkstoffe für die AM-Fertigung qualifiziert und mehr als 60.000 Teile hergestellt.

Ohne Process Tuner erfordert der Arbeitsablauf der Entwicklung von Prozessparametern einen hohen manuellen Aufwand.
Innerhalb seiner Rolle bei der Qualifizierung von Metallwerkstoffen verbringt das Team einen Großteil seiner Zeit mit dem Testen und Validieren von Parametern. Aber, wie bereits erwähnt, bringen diese Aufgaben auch eine Reihe von Herausforderungen mit sich.
„Das Datenhandling und die Produktionsplanung zur Parameteroptimierung waren schon immer mit viel manuellem Aufwand verbunden“, erklärt Philipp Schwarz, Business Development Manager bei Rosswag. „Für jeden Test mussten wir die Werte für alle unterschiedlichen Parameterkombinationen manuell einstellen und dokumentieren. Je mehr Tests erforderlich sind, desto zeitaufwendiger wird diese Aufgabe. Wir hatten zum Beispiel eine Studie mit mehr als 400 Würfeln, die mithilfe der üblichen Arbeitsweise mindestens einen ganzen Tag in Anspruch nehmen würde.“
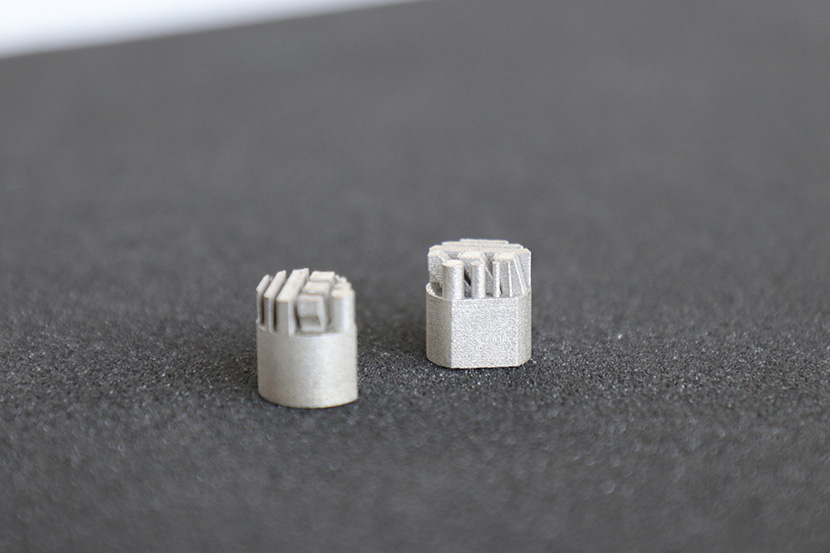
Für solche Experimente werden oft 20 bis über 100 gedruckte Proben benötigt – je nachdem, ob die neuen Parameter für eine bekannte oder eine brandneue Legierung entwickelt werden.
Doch dieser enorme Zeit- und Arbeitsaufwand war nicht die einzige Herausforderung, mit der sie konfrontiert waren. Das Einrichten und Verfolgen von Daten ohne eine geeignete Datenbank erhöhten das Risiko menschlicher Fehler erheblich. Ein Fehler, wie z. B. die falsche Beschriftung eines Parameterwerts, konnte die gesamte Studie zum Scheitern bringen.
Lösung
In Zeiten, in denen ein Übermaß an manueller Arbeit den Unternehmen Probleme bereitet, ist die Automatisierung von Aufgaben oft die ideale Lösung. Aus diesem Grund war die Additivabteilung von Rosswag, als sie von den Möglichkeiten von Materialise Process Tuner erfuhr, begeistert von dem Potenzial, das es für die Durchführung ihrer Versuchsanordnung (DOE) bietet. Der Process Tuner ist eine neue Softwarelösung von Materialise, mit der die kollaborative Entwicklung von Prozessparametern durch automatisierte Arbeitsabläufe, gewonnene Einsichten und eine eingebettete Datenbank optimiert wird.
Die Arbeit mit dem Process Tuner ist sehr einfach, und aufgrund der Automatisierung besteht keine Gefahr Fehler zu machen.
- Philipp Schwarz, Business Development Manager bei Rosswag
„Als wir uns mit dem Team von Rosswag trafen und von ihren Projekten erfuhren, wussten wir, dass sie perfekt für unser Validierungsprogramm von Process Tuner geeignet sind“, sagt Vivek Chowdary Penumarthi, Produktmanager bei Materialise. „Dank dieser Zusammenarbeit konnten sie unsere frühen Versionen der Software zur Verbesserung ihrer Arbeitsabläufe nutzen, und wir konnten ihr wertvolles Feedback nutzen, um die Lösung kontinuierlich zu verbessern.“
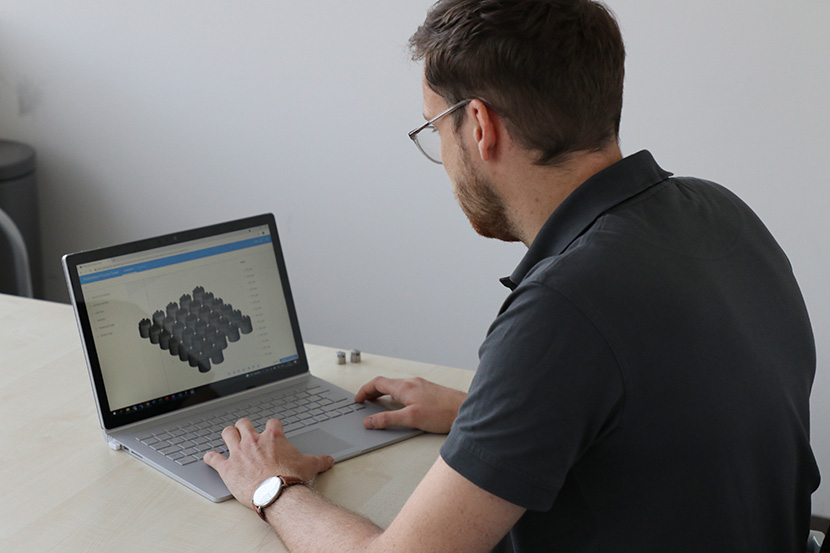
Das Team von Rosswag ist Teil unseres Validierungsprogramms und gibt wertvolles Feedback über den Process Tuner.
Der Process Tuner war genau das Richtige für die Projekte von Rosswag, weil damit die Erstellung eines jeden Experiments automatisiert und verfolgt werden kann. „Mit dieser Software können wir komplexe multidimensionale Parameterstudien viel schneller und effizienter vorbereiten und durchführen. Die Arbeit mit dem Process Tuner ist sehr einfach, und aufgrund der Automatisierung besteht keine Gefahr von Fehlern“, erklärt Philipp Schwarz.
Dank der nahtlosen Integration mit Build Processors. kann der Benutzer die in mehrere Schichten unterteilte und schraffierte Auftragsdatei mit einem Mausklick erzeugen. Anschließend werden alle für den Druck erforderlichen Informationen – einschließlich der Auftragsdatei, der Plattformdateien und der Parameter – automatisch in der integrierten Datenbank gespeichert.

Process Tuner vereinfacht die Prozessentwicklung dank automatisierter Schritte und einer integrierten Datenbank. Darüber hinaus ermöglicht ZEISS AM Parameter eine schnelle, wirtschaftliche und automatisierte Analyse von Defekten und Verformungen der Proben.
Die Durchführung von Studien zur Material- und Parametervalidierung wurde durch die Kombination dieses Arbeitsablaufs mit Lösungen von ZEISS. noch weiter vereinfacht. Rosswag nutzt die Innovation von Zeiss, um die Porosität schnell und automatisch an verschiedenen Stellen des Prüfkörpers zu messen, z. B. an der Hauptfläche, an dünnen Wänden, Überhängen, Zylindern und Konturen. Die Eigenschaften des Prüfkörpers können je nach zu druckendem Endteil angepasst werden. Diese Zusammenarbeit bedeutete einen enormen Unterschied im Aufwand für die Labortests und die Analyse der Ergebnisse.
Ergebnis
Rosswag konnte schnell eine enorme Verbesserung der DOE-Arbeitsabläufe feststellen. Die Datenvorbereitung, die normalerweise etwa 3 Stunden und manchmal sogar mehr als einen Tag in Anspruch nahm, konnte in 20 bis 30 Minuten erledigt werden. Die Anzahl der Proben hatte früher einen enormen Einfluss auf den Zeit- und Arbeitsaufwand des Datenaufbereitungsprozesses. Doch mit den Funktionen von Process Tuner kann die Datenaufbereitung unabhängig von der Anzahl der Proben in 20 bis 30 Minuten abgeschlossen werden.
Insgesamt spart das Team von Rosswag nun durchschnittlich mehr als 20 Stunden Entwicklungszeit pro Monat. „Wir bieten unseren Kunden eine Erstqualifizierung neuer Legierungen von der Pulverzerstäubung bis zu den mechanischen Eigenschaften der gedruckten Proben in weniger als zwei Wochen. Diese extrem schnellen Entwicklungszyklen erreichen wir nur dank des Process Tuners“, erklärt Philipp Schwarz.
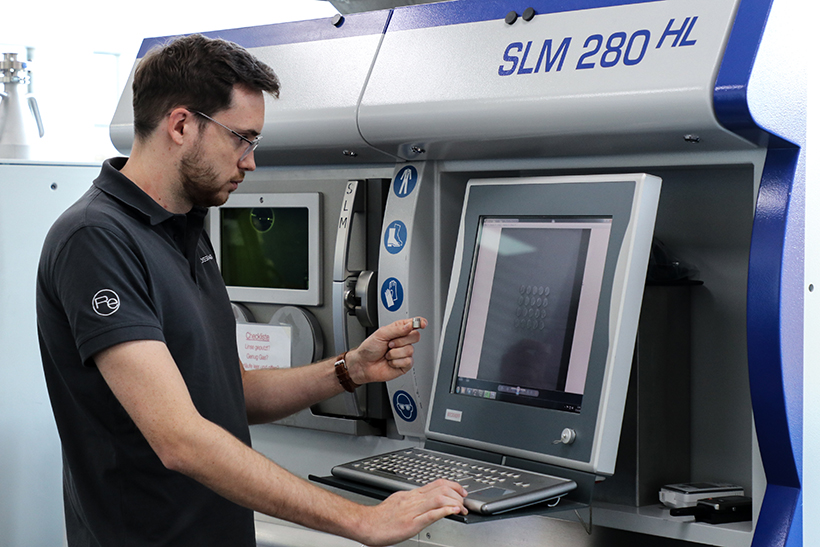
Durch die Integration mit Build Processor können Anwender mit einem Mausklick in mehrere Schichten unterteilte und schraffierte Auftragsdateien erzeugen.
„Kooperationen wie diese sind entscheidend für eine schnelle Industrialisierung der additiven Fertigung“, sagt Schwarz abschließend. „Es ist wichtig, mit anderen in der Branche zusammenzuarbeiten, die die Möglichkeiten dieser erstaunlichen Technologie ausreizen wollen.“
Derzeit validiert Rosswag auch die Betaversion von Process Tuner Simulation. Sowohl das Team von Materialise als auch das von Rosswag sind sehr zuversichtlich, dass dieses 2D-Simulationstool die Gesamtzahl der gedruckten Bauteile reduzieren kann, die für ein optimales Prozessfenster notwendig sind.
ZEISS® ist eine eingetragene Marke der Carl Zeiss AG
Beschleunigung der Prozessentwicklung
Einfache und schnelle Qualifizierung von Materialien und Maschinen für die AM-Fertigung.