MANUFACTURING
3DP-Erprobung: Schnelle Entwicklung einer leichteren und präziseren Prüfvorrichtung für die Automobilindustrie
In diesem Blog erfahren Sie, wie die Berater von Mindware die Hyundai Motor Company (HMC) bei der Erforschung und Entwicklung einer Prüfvorrichtung mit beeindruckenden Verbesserungen unterstützt haben, wie z. B. einer Gewichtsreduzierung von über 50 % und bis zu dreimal schnelleren Durchlaufzeiten. Die Einbindung der additiven Fertigung (AM) in Unternehmen ist nicht einfach; HMC benötigte die Unterstützung unserer Experten, um diese Erfolge zu erzielen.
Schritt zwei auf dem Erfolgsweg der AM-Fertigung: Experimentieren
In unserem letzten Blog dieser Serie haben wir ein von unseren Mindware-Beratern entwickeltes Modell vorgestellt, das die Schritte und Schlüsselfragen auf dem Weg zum Erfolg in der additiven Fertigung skizziert. Ganz gleich, aus welcher Branche Sie kommen oder was Sie erreichen wollen, Sie werden auf eine der Phasen des Erkundens, Experimentierens oder Aktivierens treffen. Je nachdem, in welcher Phase Sie sich befinden, kann Mindware Sie bei der Bewältigung der wichtigsten Herausforderungen unterstützen und Ihnen helfen, Ihren AM-Zielen einen Schritt näher zu kommen.

Das Team von Mindware und sein Drei-Phasen-Modell führen Unternehmen durch ihre Reise im Bereich der AM-Fertigung.
Konzentrieren wir uns auf die zweite Phase des Modells: die Stufe des Experimentierens bzw. der angewandten F&E. In dieser Phase befinden sich Kunden, die mit der Erkundung abgeschlossen haben und sich nun darüber im Klaren sind, welche Möglichkeiten der AM-Fertigung sie verfolgen und welche Anwendungen sie zuerst entwickeln sollten. Dies gibt natürlich eine gute strategische Orientierung und Ausrichtung vor, aber es ist keine Garantie dafür, dass die Ideen und die Strategie aus geschäftlicher und technischer Sicht realisierbar sind. Hier kommt die Experimentierphase ins Spiel, in der wir diese Ideen auf Herz und Nieren prüfen und sie in konkrete Anwendungen umsetzen, die ein breites Spektrum von Anforderungen erfüllen.

Dieser Abschnitt des Modells hebt die wichtigsten Herausforderungen hervor, die in der Experimentierphase zu bewältigen sind, und geht auf die Fragen ein, bei deren Beantwortung unser Team helfen kann.
Auswahl der besten AM-Anwendungsmöglichkeit: Handgehaltene Prüfvorrichtungen
Für die Hyundai Motor Company (HMC) war der 3D-Druck nichts Neues. Seit vielen Jahren setzt das Unternehmen den 3D-Druck für das Rapid Prototyping ein, und sein F&E-Team entwickelte mehrere Anwendungsfälle für den Fertigungsbereich. Für diese Zusammenarbeit mit Mindware hatte HMC eine ganz bestimmte Anwendung im Sinn, deren Umsetzung schwierig war: ein tragbares Lampenprüfgerät für die Arbeiter am Fließband.
Bei HMC gibt es für jedes Automodell dutzende von internen und externen Lampenbaugruppen, die bündig mit der Fahrzeugkarosserie abschließen müssen. Um dies zu gewährleisten, müssen die Montagearbeiter Handgeräte, sogenannte Inspektionsvorrichtungen, verwenden, um die Fahrzeugkarosserie zu prüfen und Spaltmaße zu messen. Diese Vorrichtungen werden nicht nur am Fließband verwendet, sondern spielen auch in der letzten Phase der Vorproduktion eine wichtige Rolle. Sie werden genutzt, um zu beurteilen, ob bei den neuen Fahrzeugmodellen Konstruktionsfehler gemacht wurden. Durch diese Kontrollen kann verhindert werden, dass Konstruktionsfehler unentdeckt in die Massenproduktion einfließen – ein Problem, dessen Behebung sehr kostspielig wäre.
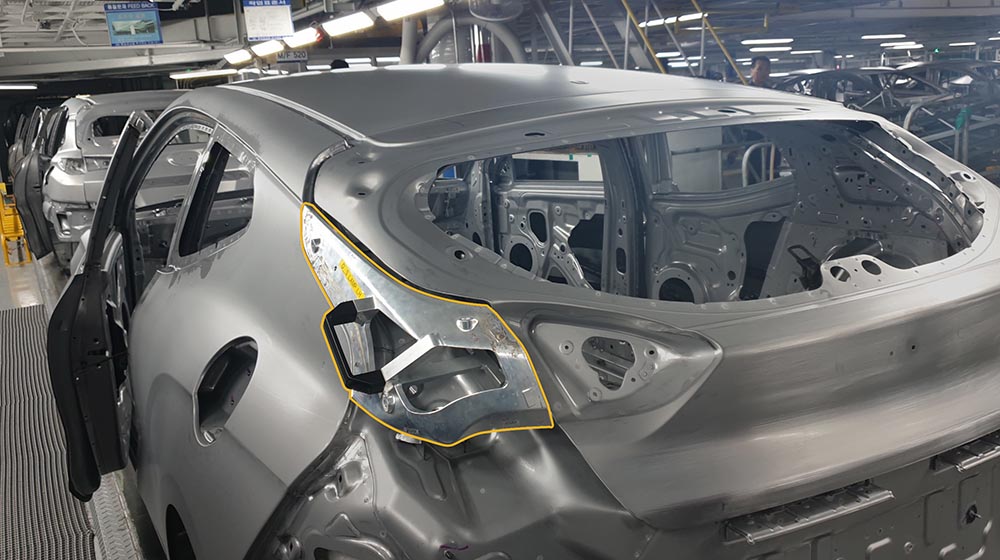
HMC wollte die Inspektion in der Produktion durch eine 3D-gedruckte Prüfvorrichtung optimieren.
Definition der Herausforderung von HMC: Geschwindigkeit, Genauigkeit und Gewichtsreduzierung erreichen
Während eines ersten Klärungsworkshops erläuterte HMC, dass es mehrere Probleme mit den konventionell hergestellten Aluminiumvorrichtungen gab, die man durch den 3D-Druck zu lösen hoffte. Zu den gewünschten Verbesserungen gehörten eine schnellere Durchlaufzeit, eine höhere Präzision und eine Gewichtsreduzierung. Gleichzeitig wollten sie die Stückkosten senken und die mechanische Festigkeit der Vorrichtung beibehalten.
- Vorlaufzeit: Die dreimonatige Vorlaufzeit für die ursprünglichen Vorrichtungen überstieg die Lieferfrist für neue Fahrzeugmodelle in der Vorproduktionsphase. Dies war vor allem bei den kritischen Vorrichtungen problematisch, die bei der Endprüfung vor der Massenproduktion eingesetzt werden mussten. Wenn diese nicht rechtzeitig zur Verfügung standen, war eine ordnungsgemäße Endprüfung vor der Massenproduktion nicht möglich, was hohe Risiken und versunkene Kosten verursachte.
- Präzision: Die Präzision der Vorrichtungen betrug 0,15 mm und musste für die Massenproduktion auf 0,1 mm gesenkt werden. Andernfalls könnte dies zu suboptimalen Inspektionen führen, gefolgt von einem Verlust an Ansehen und Markenwert für HMC.
- Gewicht: Das derzeitige Gewicht von 1,8 kg war zu schwer. Die Arbeiter müssen diese Vorrichtung 100-mal anheben, jeweils einmal pro Minute. Die Gewichtsreduzierung war ein wichtiger Werttreiber und entscheidend für eine gute Beziehung zur Gewerkschaft.
Am Ende dieses Workshops war das Ziel klar. HMC und Mindware würden gemeinsam ein 3D-gedrucktes Prüfgerät entwickeln, das aufgrund seiner hohen Präzision, seines geringen Gewichts und seiner kürzeren Vorlaufzeiten eine 2-in-1-Lösung für die Vor- und Massenproduktion darstellt. In nur wenigen Wochen entwickelten wir einen Konzeptnachweis für die hintere Außenleuchte und testeten es direkt mit HMC-Mitarbeitern an der Produktionslinie.
Fundierte Entscheidungen für die optimale Konstellation der AM-Fertigung treffen
Sobald die Akzeptanzkriterien für eine bestimmte Anwendung definiert sind, besteht der nächste Schritt darin, die optimale Kombination aus 3D-Design, Material, AM-Technologie und Nachbearbeitungstechnik zu ermitteln.
Als Erstes musste das derzeitige Design der Vorrichtung überdacht werden. Zuvor war die Vorrichtung ein massives Bauteil, das 1,8 kg wog und viel Leergewicht aufwies. Das Ziel war eine Gewichtsreduzierung von 30 % durch ein leichtes Design basierend auf einer Wabenstruktur, die die Menge des verwendeten Materials minimiert und gleichzeitig die Festigkeit des Teils bewahrt.
Nachdem das Designkonzept das Ziel der Gewichtsreduzierung erreicht hatte, mussten wir prüfen, welche Kombination aus Material, Technologie und Endbearbeitung die Anforderungen an Präzision und Festigkeit am besten erfüllen würde. Die Tatsache, dass diese Parameter jeweils 5-10 Optionen haben können, führt oft zu einer überwältigenden Vielfalt an Optionen, die für Unerfahrene sehr schwierig zu durchschauen ist. Die Berater von Mindware halfen Hyundai, die Optionen auf drei mögliche Kombinationen einzugrenzen.

Design, Technologien, Materialien und Endbearbeitungsverfahren der AM-Fertigung beeinflussen sich gegenseitig und machen die Wahl der Konstellation komplex.
Die erste Option, FDM/ABS, war nicht realisierbar, da die Präzision der Teile nicht 0,1 mm erreichen würde. Außerdem war die Anwendung von Nachbearbeitungstechniken wie Fräsen ohne eine Beschädigung der Teile nicht möglich. Daraufhin zogen wir den Metall-3D-Druck in Betracht. Die Präzision könnte durch die Anwendung von Nachbearbeitungstechniken erreicht werden, aber diese Option wäre in Bezug auf Gewicht und Preis nicht besonders wettbewerbsfähig. Letztendlich landeten wir auf dem vielversprechendsten Weg - einer Kombination aus selektivem Lasersintern (SLS) und PA-AF-Material.
Herkömmliche, per SLS gedruckte Teile aus Polyamid (PA) wären nicht präzise genug, und eine Endbearbeitung mit maschinellen Verfahren wäre nicht möglich. Allerdings könnten diese SLS-Teile durch den Austausch von PA gegen PA-AF, einer Materialkombination aus Aluminium- und Polyamidpartikeln, nun auch mit Frästechniken nachbearbeitet werden, um die gewünschte Präzision von 0,1 mm zu erreichen.
Die Kombination aus SLS/PA-AF/Fräsen brachte die Lösung: Leichtbauweise, ein leichtes und kostengünstiges Material und eine Nachbearbeitungstechnik, mit der die strengen Präzisionsanforderungen erfüllt werden können. Mit der Definition des Designs und der optimalen Konstellation der AM-Fertigung konnten wir zu den nächsten Schritten in der Experimentierphase übergehen: Entwurf, Konstruktion, Fertigung und Prüfung des Teils.

Beim Vergleich der drei vielversprechendsten 3D-Druck-Kombinationen war SLS/PA-AF/Fräsen der eindeutige Sieger.
Ein erfolgreicher Konzeptnachweis weist auf das Potenzial für eine groß angelegte Vorrichtungsproduktion hin
Nach dem zweitägigen Workshop vor Ort kehrte das Team von Mindware nach Belgien zurück und bediente sich des Fachwissens und der zertifizierten Fertigungskapazitäten von RapidFit, einer Tochtergesellschaft von Materialise, um den funktionalen Prototyp zu entwerfen und herzustellen.
Bei diesem Experiment wurde ein entscheidender Vorteil der additiven Fertigung deutlich: die kurzen Vorlaufzeiten. Dank des digitalen Charakters konnten wir die Konzeptdurchläufe beschleunigen und den gesamten Entwicklungsprozess von drei Monaten auf einen Monat verkürzen. Unsere Ingenieure konnten direkt mit der CAD-Datei der Lampe beginnen und integrierten sogar die Funktion des Positionsgebers in das Design, um die Montagearbeiten zu reduzieren.

Die 3D-gedruckte Vorrichtung erfüllte alle Ziele der HMC und ermöglichte zusätzliche integrierte Funktionen.
Sobald das Teil gedruckt war, führten wir eine detaillierte Qualitätsprüfung durch, indem wir es alle 15 mm scannten - eine Prüfung, die bei der Herstellung der ursprünglichen Aluminiumvorrichtungen nicht vorgesehen war. Drei Wochen später wurde die 3D-gedruckte Prüfvorrichtung an HMC geliefert und von deren Team erfolgreich in der Vor- und Massenproduktion getestet. Die Mitarbeiter am Fließband, die täglich damit arbeiten würden, waren beeindruckt.
Weltweit führende Automobilhersteller wie HMC produzieren jedes Jahr dutzende einzigartiger neuer Fahrzeugmodelle, die nicht nur dutzende einzigartiger Lampenvorrichtungen, sondern auch dutzende von Vorrichtungen für die anderen 20 Fahrzeugteile erfordern. Dank der Unterstützung von Materialise Mindware gelang es dem Unternehmen, das Potenzial des 3D-Drucks in der Produktion zu nutzen, was erhebliche Vorteile für das Geschäft und den Ruf der Marke mit sich brachte und gleichzeitig der Gesundheit und Sicherheit der Mitarbeiter in der Fertigung zugutekam.
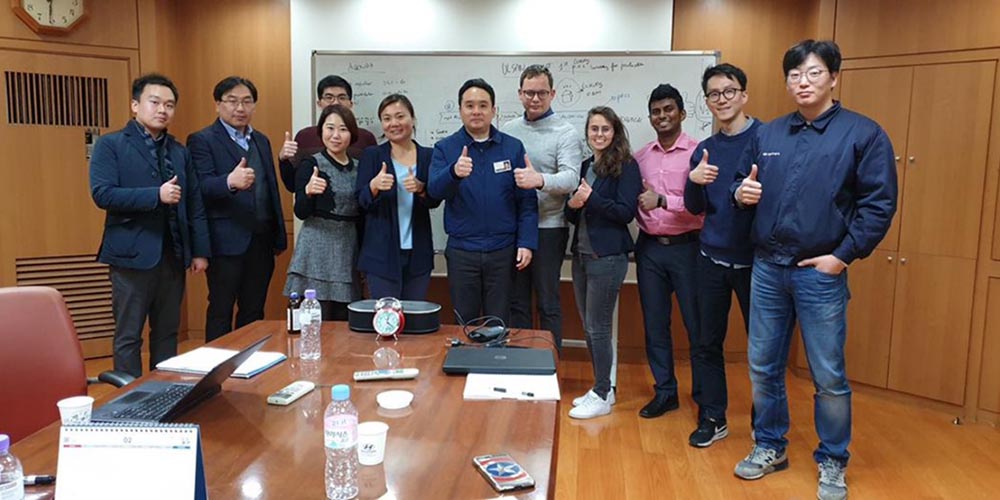
Beide Teams kombinierten ihr Know-how, um eine erfolgreiche 3D-gedruckte Prüfvorrichtung zu entwickeln.
Durch die Kombination der umfassenden Kenntnisse der Berater von Mindware in Sachen 3D-Druck-Prozesse mit den klaren Anwendungszielen von HMC konnten die Teams in diesem Fall schnell und effizient den effektivsten Weg zum Einsatz des 3D-Drucks finden. Fälle wie dieser zeigen, warum eine fachkundige Beratung in der Experimentierphase entscheidend ist, um die Effektivität der Technologie zu maximieren und versunkene Kosten zu minimieren.
Effizientes Experimentieren mit Experten von Mindware
Sparen Sie Zeit und Geld in der Phase der angewandten Forschung und Entwicklung.